FACILITIES MAINTENANCE MANAGER JOB DESCRIPTION
Updated: Jun 12, 2025 - We are seeking a Facilities Maintenance Manager to lead and motivate a maintenance team, enhancing equipment reliability and optimizing resources through strategic engineering improvements and sustainable practices. This role involves overseeing technicians, collaborating across departments, and maintaining high morale and integrity among staff by fostering positive development and training. Additionally, the manager will handle maintenance costs, strategize resource allocation, and ensure the timely and budget-compliant achievement of maintenance goals.
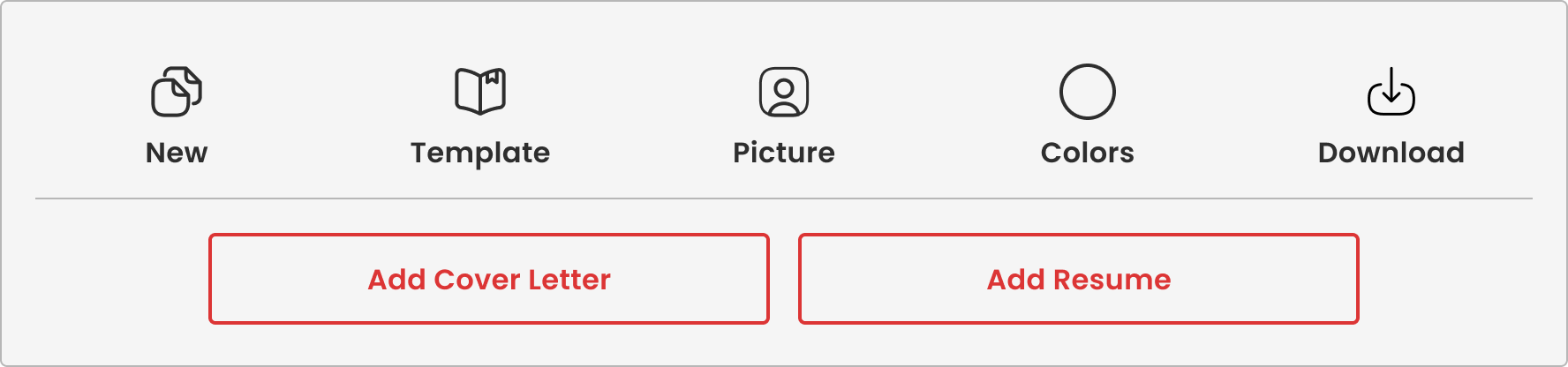

An Overview of Facilities Maintenance Manager Job Description Responsibilities and Qualifications
1. The Facilities Maintenance Manager role is essential in supporting our logistics operations within a vast 500,000+ square foot facility by ensuring all equipment, both automated and mechanized, is maintained to the highest standards. This position not only oversees maintenance management but also acts as a technical expert across all maintenance disciplines. The role is crucial in analyzing, recommending, and implementing maintenance initiatives aimed at enhancing safety, compliance, production integrity, and equipment availability. By establishing robust programs, the Maintenance Manager ensures the integrity of mechanical, electrical, and instrumentation systems through strategic planning, scheduled shutdowns, and both preventative and predictive maintenance efforts.
Facilities Maintenance Manager Roles:
- Leadership of the maintenance team in applying best maintenance practices to maximize equipment reliability & resource availability through engineering improvement and sustainability programs
- Direct, lead and coach a team of technicians who manage the facilities maintenance as well as interface with managers of other departments and ensure an efficient, fully utilized operation
- Maintain a high level of employee morale and integrity in the department through positive motivation, development, and training
- Evaluate and benchmark (gap analysis) existing plant procedures/practices/performance measures versus internal & external industry specific benchmarks
- Conduct “root cause” failure analysis on chronic maintenance and repair issues and initiates corrective actions to equipment design and / or work practices
- Develop detailed planning to control departmental elements, including spending, staffing, etc.
- Collaborate with supplies/purchasing teams to identify and negotiate purchase of needed components, equipment and contract services
- Oversight of maintenance cost center and accountability to ensure all maintenance objectives are completed on time and within budget / forecast
- Achieve synergies with vendors / contractors supporting maintenance initiatives
- Assess and document success / failure of completed work orders, creating feedback to further drive effective work order execution
- Establish work schedules to include preventive maintenance, cleaning and inspection routines and operational support
- Optimize spare parts carrying costs and ensure spare parts availability
- Analyze historical equipment data and apply the understanding to prevent future outages or failures
- Develop an on-going replacement analysis program for capital equipment based on work order and preventative maintenance histories, reliability performance and cost
- Manage maintenance projects from concept to implementation, including personnel oversight, sketching, reviewing detailed drawings, vendor negotiations, supervising contractors, and documenting final results
- Conduct cost / benefit analysis, oversees development of key maintenance initiative justification, presents projects to superiors and gains approval / guidance
- Communicate the status of a wide range of maintenance activities to key stake holders
- Anticipate questions and prepare technical and business correspondence pertaining to the business case for each maintenance initiative from all affected parties, including senior management members
- Identify maintenance constraints (manufacturing process, budget, schedule, etc.) and appropriately address
Facilities Maintenance Manager Experience and Qualifications:
- Bachelor’s Degree; or equivalent training, education and applicable experience
- Experience in implementing and managing organized maintenance management, work management, and reliability improvement programs
- Minimum 7 years of experience in a heavy industrial environment with various types of mechanized automation and system controls
- Minimum 5 years of experience supervising personnel
- Experience with MHS as well as PLC and Conveyor maintenance
- Proficiency with Microsoft office computer software
- Ability to effectively utilize maintenance software to input data and research parts; i.e. Computerized Maintenance Management Systems
- Comfortability in a variable environment, including (but not limited to) frequent walking, standing, sitting, and exposure to all seasonal climatic conditions
- Experience with a variety of personalities and discipline fields and able to manage and react to ongoing and changing operational requirements
- Excellent communication skills including technical writing, presentation skills and ability to interface with all levels of management and diverse staff and guests.
- Working knowledge of Windows, Microsoft Word, Project, Access, AutoCAD and other job related computer programs.
- Occasionally lifting, carrying, and/or pulling objects up to 50 lbs.
- On call availability during all hours of operations to support as needed with equipment failures
- WMS,WCS, SCS experience preferred