HEAD OF MAINTENANCE RESUME EXAMPLE
Published: Apr 24, 2025 - The Head of Maintenance manages maintenance across three sites, covering mechanical, electronic, and infrastructure services. This role ensures efficient maintenance planning and spare parts availability to support production uptime. The head drives continuous improvement through root cause analysis and World Class Manufacturing practices.
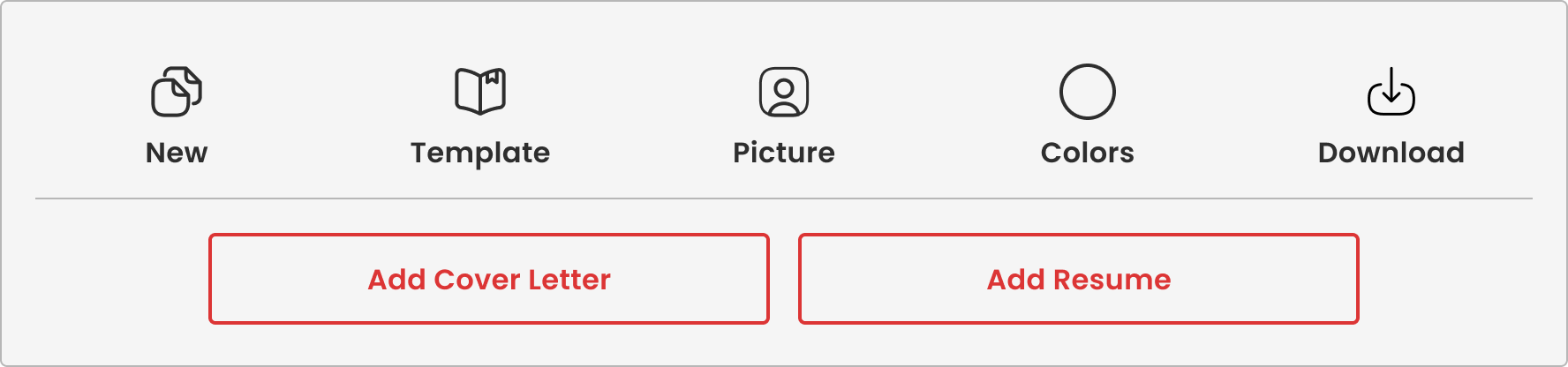
Tips for Head of Maintenance Skills and Responsibilities on a Resume
1. Head of Maintenance, GreenTech Components, Fort Wayne, IN
Job Summary:
- Supervisory work on aircraft status, maintenance scheduling, and other maintenance operations
- Maintaining the overall condition of the aircraft fleet, workshop and hangar facilities
- Oversee the Airworthiness of the aircraft fleet
- Reviews and ensures all required entries into the aircraft logbooks and records are accurate and by company and regulatory bodies
- Ensures all required scheduled maintenance and aircraft are maintained safely and efficiently per established company policies, standards, regulations, and well as manufacturer recommendations
- Plans and assigns work schedules and work orders for scheduled and unscheduled maintenance and calendar items
- Oversees and reviews work orders while jobs are in progress, monitoring for proper sign-offs, supervising and inspecting
- Communicates effectively and accurately by closely working together with all other departments, aircraft manufacturers' representatives, parts suppliers, and approved repair stations
- Maintain a culture of safety with efficient procedures that support customer service and budgets
- Oversees WOA flight software to schedule maintenance activities
- Develop and set maintenance policies, standards, tools and processes, including determining safety procedures and processes
- Maintains a safe work environment and reports and improves any unsafe conditions
- Schedules maintenance personnel hours to maintain efficient operations of the maintenance department
- Overall responsibility for the financial performance of the aircraft maintenance part of the business
Skills on Resume:
- Maintenance Scheduling (Hard Skills)
- Fleet Oversight (Hard Skills)
- Airworthiness Supervision (Hard Skills)
- Logbook Accuracy (Hard Skills)
- Team Coordination (Soft Skills)
- Safety Compliance (Hard Skills)
- Policy Development (Hard Skills)
- Cross-Department Communication (Soft Skills)
2. Head of Maintenance, Blue Ridge Food Solutions, Roanoke, VA
Job Summary:
- Implement the CAFM solution and required maintenance processes
- Ensure that all maintenance is carried out as agreed
- Ensure that all PPM Maintenance is carried out as agreed, according to statutory requirements
- Manage all contractors against predetermined targets regarding service levels, quality, cost, and H&S
- Manage both reactive and PPM budgets
- Liaise with Restaurateurs, ensuring good communication throughout maintenance processes
- Liaise with external bodies (Landlords, LA – EHO, etc)
- Ensuring maximum operational availability of machinery and equipment
- Planning and managing maintenance costs
- Management of internal and external projects and use of project management methods
- Organizing processes optimally, according to the set goals and achieving maximum efficiency
- Manage maintenance processes on machine devices
- Working closely with the Engineering Function and reporting directly to the Operations Director
- Responsible for planning, organising and directing the maintenance, repair and alteration of production-related machinery, equipment, facilities and buildings
Skills on Resume:
- CAFM Implementation (Hard Skills)
- PPM Management (Hard Skills)
- Contractor Oversight (Hard Skills)
- Budget Control (Hard Skills)
- Stakeholder Communication (Soft Skills)
- Project Management (Hard Skills)
- Process Optimization (Hard Skills)
- Equipment Availability (Hard Skills)
3. Head of Maintenance, Titan Plastics Group, Macon, GA
Job Summary:
- Responsible for leading the team to achieve performance, quality and efficiency of the equipment M&R
- Ensure availability, reliability, safety and effective daily operation of all Quay Cranes, RTGs and Mobile Equipment
- Manage CAPEX and OPEX within the essential needs and the budget given
- Responsible for Staff Management and Development
- Ensure competency development plans for the direct reports and the workforce
- Works closely with HR to assess skills and competencies of M&R staff and advise on closing technical and managerial skills gaps
- Ensures appropriate Managerial, Technical and HSE level of performance and training is provided to staff
- Anticipate effectively, practically, demonstrate and implement Way of Working Transformation and ensure alignment with the annual department targets and plans
- Responsible for providing complete and accurate reports to the Head of Division, SMT
- Responsible for setting goals and objectives for the Department and respective sections
- Responsible for preparing and managing the Yearly Budget for the Department
- Oversees all types of machinery performance to improve efficiency and safety
- Establishes appropriate communication channels with the Operations division to optimize equipment downtime (planned and unplanned)
- Establishes appropriate internal communication channels with other departments within the Engineering and Facilities Division
- Responsible for the successful delivery of PPM and Site Repair projects
- Be involved with the successful delivery of CAPEX Projects
Skills on Resume:
- Team Leadership (Soft Skills)
- Equipment Reliability (Hard Skills)
- Budget Management (Hard Skills)
- Staff Development (Soft Skills)
- Competency Assessment (Soft Skills)
- HSE Training (Hard Skills)
- Project Delivery (Hard Skills)
- Cross-Department Communication (Soft Skills)
4. Head of Maintenance, Ironwood Metalworks, Grand Rapids, MI
Job Summary:
- Ensure adequacy of departmental processes to minimize breakdowns and downtimes
- Efficient running of equipment and utilities, including continuous improvement of the processes based on breakdown analyses and potential failure mode analyses
- Ensure effective implementation and continuous improvement of Autonomous, Preventive and Predictive Maintenance
- Training and development to ensure an adequate skill level in the department
- Representative of PMT in external interactions - Management Meetings, Inter-department coordination
- Timely execution of Utilities and Equipment projects
- Approvals from and liaising with government agencies / statutory bodies
- Continuously improve on cost of maintenance to achieve management targets
- Ensure speedy and quality addressing of breakdowns
- Continuous Improvement in the consumption of energy, power & other utility inputs to meet management targets
- Ensures HSE policies are met as well as international Safety of Machinery standards
- Lead team and responsible for ensuring that budgets, forecasts and execution of work against budgets and forecasts are accurate and supporting the business needs
- Actively seeking new business opportunities to sustain and grow the maintenance, hangar and workshop business
- Introduce procedures to underpin continuous improvement
Skills on Resume:
- Process Efficiency (Hard Skills)
- Failure Analysis (Hard Skills)
- Maintenance Strategy (Hard Skills)
- Skill Development (Soft Skills)
- Stakeholder Representation (Soft Skills)
- Cost Optimization (Hard Skills)
- HSE Compliance (Hard Skills)
- Business Growth (Soft Skills)
5. Head of Maintenance, Solaris Packaging, Fayetteville, AR
Job Summary:
- Coordinate and manage maintenance activities of three sites, leading the different maintenance segments, mechanical, electronic, new technologies and infrastructures/external services
- Define and ensure minimum spare parts to guarantee quick reactiveness to restore production and to perform planned preventive maintenance
- Define, deploy and assure the fulfillment of preventive, corrective and predictive maintenance plans
- Analyze corrective maintenance to determine root causes by developing new preventive or predictive maintenance
- Cooperation with linked areas as production, logistics, and process development
- Ensure that safety and quality requirements are met
- Participate in the process development to assure maintenance definition and design for better and quicker maintenance
- Manage and improve the availability and reliability of production assets and services
- Analyse asset performance trends and implement corrective action and improvement opportunities
- Implement and manage the improvement of Asset care and introduce a culture of Reliability Engineering
- Create Sops and entrench a culture aimed at the utilisation of World Class Manufacturing practice
- Interacts with HR for continuous updates on company policies and procedures, labor law and new staff employment
- Ensures the contractor’s effectiveness and high performance based on the business needs
Skills on Resume:
- Site Coordination (Hard Skills)
- Spare Planning (Hard Skills)
- Plan Fulfillment (Hard Skills)
- Cause Analysis (Hard Skills)
- Team Collaboration (Soft Skills)
- Safety Compliance (Hard Skills)
- Asset Reliability (Hard Skills)
- Contractor Oversight (Soft Skills)