WHAT DOES A FACILITIES ENGINEER DO?
Updated: Jul 8, 2025 - The Facilities Engineer enhances equipment reliability and plant availability by monitoring systems, analyzing data, and proposing continuous improvements. This role involves managing plant documentation, coordinating engineering projects, ensuring regulatory compliance, and preparing contracts for equipment upgrades and maintenance. Additionally, the engineer tests machinery, estimates costs, and prioritizes projects to optimize maintenance operations and production efficiency.
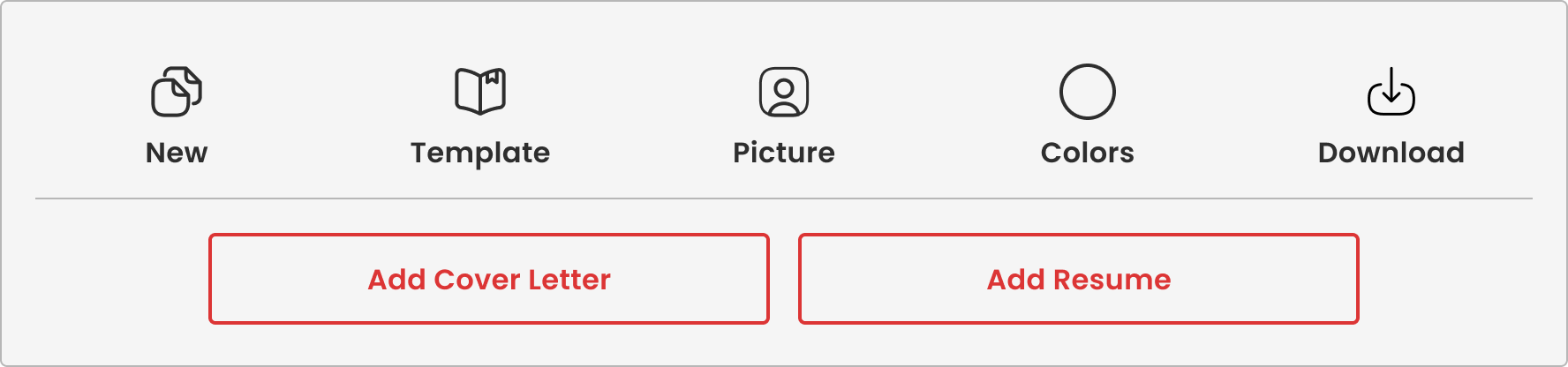

A Review of Professional Skills and Functions for Facilities Engineer
1. Facilities Engineer Duties
- Governance and Performance Management: Work to improve control and governance of the operations and performance management of various contractual parties.
- Energy Management: Review and enhance the energy management plans & utility performance of the facility in line with the sustainability theme.
- FM Coordination: Single point of contact for FM function.
- MEP and Soft Services Assessment: Assess the current conditions of MEP and A/C systems and other essential FM equipment in addition to soft services management within the portfolio.
- Service Management: Manage the service in accordance with the property management and facilities companies.
- Facility Maintenance: Maintain the efficiency and good working conditions of the facilities.
- Strategic and Operational Planning: Review and propose enhancement measures on the strategic plan as well as the day-to-day operations.
- FM Service Provider Coordination: Follow up with FM SPs on technical and completion reports, review quotations received from FM service providers, and ensure that rates are in line with the price book.
- Inspection and Compliance: Conduct move-in and move-out inspections, verify issues reported by service providers, follow up and monitor reinstatement progress, conduct ad hoc inspections, advise the concerned department on PO preparation, and provide supporting documents required.
- KPI Management: Review and enhance the KPIs on a periodic basis.
- Event Facilities Management: Plan the delivery of facilities management services for all event operations within the site and successfully implement effective management across the functional areas.
2. Facilities Engineer Details
- Area Monitoring: Monitor the needs of the assigned area based on defined criteria.
- Teamwork and Maintenance Execution: Collaborate with co-workers for the execution of preventive maintenance of the building.
- Equipment Issue Resolution: Monitor equipment problems and develop action plans to correct them.
- Maintenance Planning: Assess maintenance needs and create direct plans to address them.
- Contractor Coordination: Schedule activities with contractors and suppliers specialized in construction and building modifications.
- Work Permit and Risk Evaluation: Create work permits for contractor activities and evaluate risk analysis for routine and non-routine activities.
- Maintenance Execution: Perform corrective, preventive, and productive maintenance.
- System Diagnosis: Apply theoretical knowledge to diagnose hydraulic, pneumatic, and electrical systems.
- Maintenance Planning and Development: Develop autonomous, preventive, and predictive maintenance plans.
- Equipment Functionality: Ensure the proper functioning of equipment in the work area.
- Safety Procedures: Develop security procedures in compliance with company guidelines.
3. Facilities Engineer Responsibilities
- Health and Safety Compliance: Ensure buildings meet health and safety requirements and that facilities comply with legislation, coordinating closely with traffic, security, emergency medical services, and other parties for smooth operations.
- Asset Handover Management: Coordinate the planning and management of the asset handover, including asset register management and access system/key allocation and distribution.
- Budget and Cost Control: Manage budget control and cost management, ensuring responsibility for related cost budgets.
- Performance Management: Introduce and apply rewards and penalties associated with the Performance Management System.
- Contractor Compliance and Reporting: Provide evaluations and reporting for decision-making on contractor compliance, performance, and quality.
- Operational Support and Root Cause Analysis: Provide support for operational issues and root cause analysis with basic knowledge of the systems.
- System Capability Analysis: Analyze system capabilities and future requirements during scenario evaluations, supporting lead engineers.
- Scope of Work Documentation: Complete scope of work documents for scenario analysis, corresponding to estimated cost estimates in support of lead engineers.
- Base Build Design Review: Support design reviews for base build systems in the area of responsibility, ensuring specifications are met and cost reduction improvements are identified.
- Tool Install Design Support: Support tool install designs for systems that connect to those tools, ensuring specifications are met and cost reduction improvements are identified.
- Capacity Analysis and Data Tracking: Review and support capacity analysis for systems, tracking against actual facility data and inputting this data into the CUPS system.
4. Facilities Engineer Job Summary
- Facilities Engineering Projects: Support site Facilities Engineering team projects, including Sustainability (Carbon Footprint Reduction), installation of a new CMMS, Building Management System, and on-site expansion projects.
- Continuous Improvement: Support the site facilities department with Predictive Maintenance, Planned Maintenance, and Spare Parts Program development.
- Collaboration and Problem-Solving: Collaborate with internal and external business partners to develop creative solutions for facility infrastructure challenges and opportunities.
- Process and Equipment Optimization: Identify facility process and equipment improvements/replacement opportunities using engineering principles.
- Equipment Specification and Vendor Selection: Develop detailed equipment specifications, performance expectations, and vendor selection in coordination with the Facilities Engineering team.
- Equipment and System Selection: Perform a selection of equipment/systems that support site facility operations, infrastructure, and building systems.
- Capital Business Case Development: Develop and present capital business cases to the Facilities Engineering Team and site leadership for approval.
- Testing and Qualification: Write protocols, conduct factory acceptance testing, and lead qualifications (IQ/OQ/PQ) across engineering, manufacturing, facilities, maintenance, and quality functions.
- Technical Assessment and Validation: Provide technical assessment and validation review/approval for engineering changes.
- Project Management: Ensure project completion within budget and on time.
- Technology Research and Application: Participate in industry events and research to identify technologies for potential application.
- Regulatory Compliance Support: Support customer and regulatory inspections/inquiries.
- Policy Interpretation and Improvement: Interpret, execute, and recommend modifications to site policies.
5. Facilities Engineer Accountabilities
- Department Operations Support: Support the day-to-day running of the department in terms of workload while ensuring safe working practices are adhered to.
- Regulatory Compliance: Complete works to meet current regulations to ensure compliance is maintained and audits are passed.
- Communication and Coordination: Use good communication skills to liaise with both internal/external customers and contractors.
- Infrastructure and Asset Maintenance: Assist with infrastructure upgrades and modifications/repairs to business assets.
- Independent Project Execution: Ability to work independently on projects and work assignments.
- Adaptability and Flexibility: Easily adjust to changes in priorities and respond flexibly to varying works/projects.
- Team Collaboration and Problem-Solving: Work well in cross-functional teams and workgroups to identify and resolve problems by proposing unique and innovative solutions.
- Progress Reporting: Keep the Manager informed of progress on assignments, projects, and repairs.
- Health and Safety Promotion: Promote a positive H&S culture within the business.
- Customer Service and Emergency Response: Resolve customer complaints and respond to emergencies.
- Documentation Management: Create, develop, and sustain departmental documentation.
6. Facilities Engineer Key Accountabilities
- Issue Resolution: Identify system operational issues and justify the implementation of the resolution.
- Tool Refinement: Refine current operational tools, programs, and other documentation.
- Process Efficiency: Increase process functionality, efficiency, and energy conservation.
- Asset Improvement: Facilitate the implementation of improvements in asset effectiveness, availability, and maintainability.
- Program Auditing: Audit operational programs and improve them.
- Metric Driving: Drive Overall Equipment Effectiveness (OEE) or Statistical Process Control (SPC) metrics.
- Outage Planning: Assist Operations and Maintenance in planning outages.
- Impact Guidance: Guide Operations by identifying areas of impact on work authorization requests.
- Program Maintenance: Maintain and continuously improve the program.
- Uptime Maximization: Increase process uptime and minimize equipment downtime for assigned assets.
- Failure Analysis: Drive root cause analysis on process or asset failures.
- Asset Coordination: Work with Operations, Manufacturing, and other site tenants to ensure process/equipment/asset availability to best meet customer requirements.
- Support Documentation: Develop tools, workflows, and other documentation to support maintenance and reliability.
- Initiative Leadership: Identify and champion reliability initiatives.
- Maintenance Auditing: Audit maintenance programs and improve them.
7. Facilities Engineer General Responsibilities
- Program Implementation: Develop and implement a facility management program, including preventative maintenance and life-cycle requirements.
- Facility Inspection: Conduct and document regular facility inspections.
- EHS Compliance: Partner with the EHS Manager to ensure compliance with health and safety standards and industry codes.
- Space Allocation: Collaborate with process engineering to allocate and manage facility space for maximum efficiency.
- Equipment Supervision: Supervise maintenance and repair of facilities equipment, such as fire suppression system maintenance, and the Automated Fulfillment Center.
- Facility Renovation: Oversee facility refurbishment and renovations.
- Process Improvement: Implement best practice processes to increase efficiency.
- Vendor Quotation: Obtain quotes and tenders from vendors and suppliers.
- Cost Comparison: Calculate and compare costs for goods and services to maximize cost-effectiveness.
- Contract Negotiation: Negotiate contracts to optimize delivery and cost savings.
- Activity Monitoring: Coordinate and monitor activities of contract suppliers.
- Vendor Management: Manage contractor and vendor relationships.
- Schedule Compliance: Ensure delivery schedules, quantity, and quality criteria are met.
- Work Verification: Check completed work by contractors and vendors.
- Invoice Verification: Verify payment and invoicing match contract pricing.
- Staff Planning: Plan and monitor appropriate facility management staffing levels.
8. Facilities Engineer Role Purpose
- Emergency Management: Manage and escalate critical facility-down equipment and facility-related emergencies.
- Access Control: Manage Key and Card Access Requests.
- Documentation Management: Update and manage all facility-related PM documentation.
- Spare Parts Management: Develop and maintain spare parts for facility-related equipment.
- Standard Work Development: Create and maintain all standard work related to facility activities.
- Contractor Compliance: Own Contractor Management process and compliance for the site, including developing standards, training, data management, and monitoring of compliance with the standard by contractor coordinators and all parties involved.
- Procurement Support: Purchase parts to support facility equipment and maintenance.
- Issue Resolution: Ensure closure of all actions resulting from facility-related safety issues, audit findings, PM findings, etc.
- Records Management: Manage all facility-related documentation.
- Layout Accuracy: Maintain site master ACAD layouts to ensure accuracy.
- PM Coordination: Coordinate facility-related PM activities with maintenance and external contractors.
- Utility Management: Manage site utility costs, usage, and sustainability goals.
- Infrastructure Oversight: Manage site infrastructure in I-Vu Building Automation Systems (BAS).
9. Facilities Mechanical Engineer Essential Functions
- Operational Alignment: Interface with the business and operations teams, design engineers, facilities teams, and other support teams to determine their operational needs for both current and future installations.
- Team Collaboration: Work as an integral member of the Facilities Supply Chain Manufacturing Implementation Team (Sci), and project teams that may include electrical, mechanical, and software engineers, external vendor design, external consultants, skilled trades, and EH&S to design, construct, commission, qualify, and maintain facilities support equipment and process interfaces.
- Regulatory Support: Provide technical support for the interpretation and response to facilities-related regulatory requirements in partnership with EH&S and the EFS Regulatory and Compliance COE.
- System Documentation: Develop and maintain system documentation as a tool to understand the operation, capacities, and drive failure analysis of the plant systems using tools such as process and instrumentation diagrams (P&ID), single line diagrams, capacity and load spreadsheets, functional and design specifications, installation and operational qualification (IQ/OQ), commissioning documentation, etc.
- Technical Review: Partner with EFS project managers and design teams to provide technical review for the construction process, which includes specifying consistent solutions, ensuring process and facilities operational needs are met, and supporting the commissioning and validation of new and modified systems.
- System Maintenance: Design, install, operate, troubleshoot, and maintain facility process support systems including Pollution Control, Dust Collection, General Process Exhaust, Bulk Solvent storage and distribution, Industrial Waste Water, and Water Systems.
- Equipment Integration: Design and install facility tie-ins for new and modified process equipment, including CA, CHWS&R, HWS&R, Steam, process solvents, industrial ventilation, pollution control, electrical, controls, and structural building modifications.
- Quality Execution: Utilize different business Quality Systems to facilitate the execution and implementation of new equipment or changes to existing equipment and systems.
- Project Execution: Drive projects to completion, within time and cost estimates using Gore's internal engineering project management practices, including driving technical reviews, developing specifications and drawings, customer acceptance testing, factory acceptance testing, functional verification, installation, and operation documentation of equipment and systems.
- Design Updates: Work closely with the Maintenance Supervisor to monitor any equipment design changes that may be needed and incorporate them into future designs and builds.
- Technical Collaboration: Regularly collaborate and provide technical support to Field Production and Facilities Construction personnel on upcoming facilities design.
10. Facilities Engineer Additional Details
- Facility Coordination: Cooperate with 3rd party facility engineer, security, and cleaning staff (all from admin) to provide full-functional labs and offices, in terms of sufficient utilities (HVAC, electricity, IT, PW, air compressor, gases, automation, etc), stable network, waste disposal, etc. by using daily cleaning, daily inspection, emergency handling, and troubleshooting.
- Team Collaboration: Cooperate with corporate supporting teams, such as IT, administrative, financial, sourcing, planning, procurement, supply chain, and EHS, to fulfill related facility engineering works.
- Equipment Maintenance: Manage equipment maintenance in BDC, including asset inventory, precaution maintenance, measurement, qualification, validation, etc.
- Cost Planning: Analyze and define a cost plan for facility running, covering all aspects of facility maintenance in the planned OPEX, with the help of the BDC lab manager and the finance BP.
- Expense Control: Make sure the actual expense is within the OPEX.
- Service Improvement: Be responsible for continuously improving service and driving down costs.
- EHS Compliance: Comply with the requirements of the SOP, including safety and environmental procedures (EHS).
- Property Management: Be responsible for handling matters related to facility property management.
- Strategic Planning: Participate in BDC AR (business plan) composing, AOP (Annual Operating Planning), and STRAP (Strategic Plan) alignment.
- Project Participation: Participate in BDC Phase II design and construction.
- Maintenance Handover: Take over facility maintenance after Phase II starts.
- Project Management: Manage consultants and local teams to ensure timely completion and maintenance of the global standard for all projects.
11. Facilities Engineer Roles
- Reliability Monitoring: Maximise equipment reliability and availability through monitoring plant reliability.
- Improvement Proposals: Propose improvements for consideration by line management.
- Data Analysis: Gather, collate, and analyze data in the maintenance management system, identify opportunities, and make proposals for continuous improvement in maintenance service delivery, reliability, and availability.
- Documentation Management: Ensure all plant documentation is available to plant management, including plant specifications, certificates, and process documentation, to ensure plant and equipment can be used and function according to standard operating procedures.
- Project Coordination: Plan, direct, and coordinate activities concerned with the design, construction, modification, and maintenance of plant, equipment, and machinery to improve productivity, reliability, and availability.
- Compliance Monitoring: Monitor pollution control, installation, modification, quality control, testing, operating procedure, inspection, and maintenance of plant and equipment, and report areas or instances of non-compliance.
- Contract Preparation: Prepare bid sheets and contracts for the supply of new or modification and extension of existing plant and equipment to improve functionality or performance.
- Machine Testing: Test newly installed machines and equipment to ensure fulfillment of contract specifications.
- Cost Estimation: Estimate the cost of products, services, and facilities of plant and equipment, and evaluate and implement cost-savings and cost-saving methods for plant and equipment.
- Schedule Review: Review existing production schedules and prioritize projects based on resources, current methods, and company requirements.
12. Facilities Engineer Tasks
- Team Leadership: Develop solid and positive relationships with team members and lead the team to the successful completion of projects.
- Project Planning: Establish initial scope, schedule, and budget for major electrical infrastructure renewal and remodel projects.
- SOW Preparation: Prepare design and engineering Statements of Work (SOW) for obtaining proposals from outside designers and manage design consultants to deliver the project within budget and schedule.
- Design Review: QA design documents from outside designers for compliance with SOWs, company standards, and code compliance.
- Approval Coordination: Coordinate the plan check approval process with the Local Jurisdiction.
- Standards Development: Work with Facilities Maintenance and the design team to create and maintain company electrical standards.
- Technical Support: Provide technical expertise to support Construction Project Managers during the construction of projects, including periodic site visits for verification of compliance with contract documents, codes, and standards.
- Scope Coordination: Coordinate design project scopes with Construction Managers and internal architectural and mechanical engineer team members.
- Cost Analysis: Develop a life cycle cost analysis for major equipment and infrastructure renewal projects.
13. Facilities Engineer Roles and Details
- Design Evaluation: Evaluate current facility designs and provide recommendations for enhancements to improve productivity, economics, and/or regulatory compliance.
- PFD Development: Develop PFDs for all existing and new facilities in compliance with GLO and production reporting requirements.
- Project Management: Perform feasibility studies, scope development, AFE cost estimates, bid preparation and review, economic analysis, and overall project management of assigned projects.
- Emission Control: Support efforts on production equipment design and specification to meet current and future air regulations, with a focus on economically capturing emissions and frequent collaboration with the Air Quality department.
- Pipeline Coordination: Coordinate with Production, Construction, and Midstream on oil and gas pipeline gathering installation for new horizontal facilities.
- Sand Management: Understand and support the development of a sand management strategy in conjunction with well integrity and maintenance, including a chemical treatment program.
- Safety Training: Partner with EHS on safety training related to production equipment and facilities, and support the creation and review of Standard Operating Procedures and the Operations & Maintenance Plan.
- Engineering Support: Provide engineering support on any future production, gathering, electrical, processing, or disposal facilities needed.
- Compliance Commitment: Demonstrate commitment to safety and environmental compliance in all job aspects.
- Spare Verification: Verify critical spares for assigned assets.
14. Facilities Engineer Responsibilities and Key Tasks
- Template Creation: Create a Job Book template on a per-pad basis, including construction drawings, modeling, and vendor as-built documents.
- Material Procurement: Assist with the bidding process and work together with the Field Production team and Procurement department to acquire facilities and construction materials on a highly competitive basis, such as cost savings, superior quality, quicker supply schedule, etc.
- Document Development: Develop Company standard documents for production facilities.
- Startup Participation: Document and participate in the Production facilities start-up, especially when a new design, equipment, or facilities are to be implemented.
- Timeline Coordination: Provide input to the Director of Production Operations, managers, other supervisors from the Field Operation (D&C), and Midstream teams, regarding timelines for construction.
- Risk Mitigation: Actively participate in critical path meetings and CONOP planning sessions, and assist with risk identification and mitigation strategies.
- Standards Compliance: Responsible for understanding and applying relevant Engineering standards, including the American Petroleum Institute (API), American Society of Mechanical Engineers (ASME), and GPSA standards and recommendations, specifically related to production facilities.
- Design Improvement: Consistently stay apprised of improvements to existing production facilities design and bring a proposal to incorporate into future or existing production facilities at least once a month in the team Operations meeting.
- Facility Maintenance: Maintain and check facilities and equipment regularly, and keep the related records.
- Equipment Inspection: Inspect and record facilities and equipment.
- Issue Resolution: Solve some facility issues and repairs on time.
- Information Update: Check and update the availability of the infrastructure information on time.
- Equipment Care: Maintain peripheral equipment regularly.
15. Facilities Engineer Duties and Roles
- Team Management: Responsible for the daily management of the maintenance team to ensure all maintenance and repair activities, including team member behaviors in compliance with the company’s policies, rules, and regulations for discipline, EHS, Quality, etc.
- TPM Development: Responsible for the development and continuous improvement of the TPM system, including procedures, standards, plans, and execution.
- Maintenance Leadership: Responsible for leading and supervising the team to implement AM and PM to a high quality.
- Troubleshooting Oversight: Responsible for leading and organizing the emergency troubleshooting to ensure 100% on-time delivery.
- Root-Cause Analysis: Responsible for leading the team to analyze complex issues to work out ICA and PCA.
- Performance Improvement: Responsible for the continuous improvement of equipment performance to meet higher and higher requirements of process capability, quality, safety, efficiency, cost, unplanned stop time, etc.
- Resource Coordination: Responsible for member echelon building, KPI management, communication, coordination, and cooperation within the team and outside of the team to leverage and optimize the resources.
- Spare Management: Responsible for the management and continuous optimization of spare parts to ensure a reasonable and economic spare parts level.
- Budget Planning: Responsible for the budget planning of spare parts, annual improvement projects, and investments to control a reasonable total maintenance cost level.
- Project Support: Cooperate with other teams to support the facility project, including proposal assessment, AM/PM planning and execution, and issues follow-up.
- Parts Execution: Spare parts planning and execution, equipment acceptance, etc.
- Design Review: Support design reviews for base build systems in the area of responsibility, ensuring specifications are met and cost reduction improvements are identified.
- Tool Installation: Support tool install designs for the systems that connect to those tools, ensuring specifications are met and cost reduction improvements are identified.