Published: September 13, 2024 – The Customer Quality Engineer analyzes return goods data, consumer reviews, and call center information to support continuous improvement efforts and new product development. This role involves leading root cause analysis and cross-functional meetings and driving continuous improvement initiatives in manufacturing processes and consumer products. The engineer also supports quality in supplier interactions, product inspections, system audits, and the development of inspection instructions and procedures.
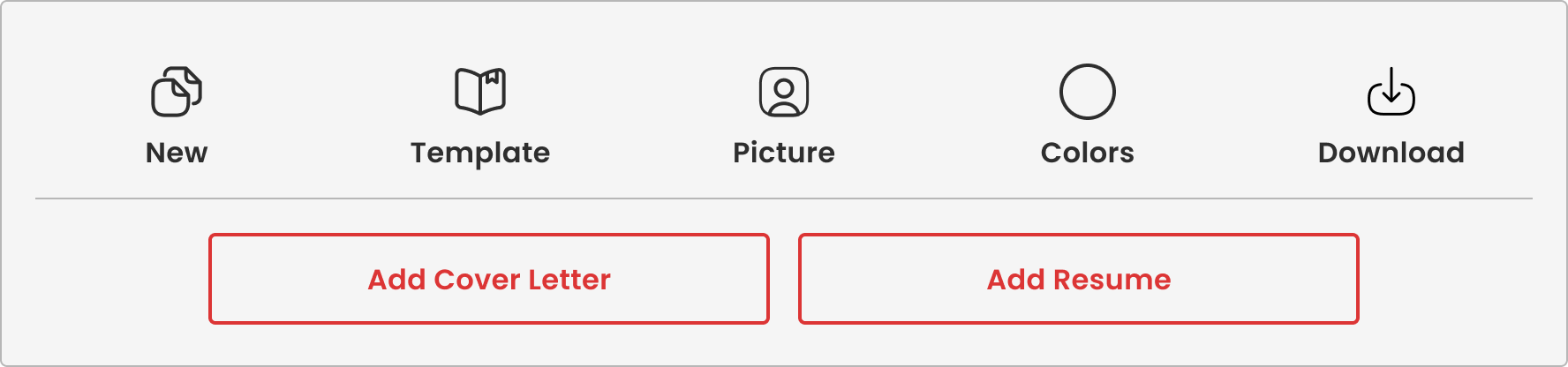
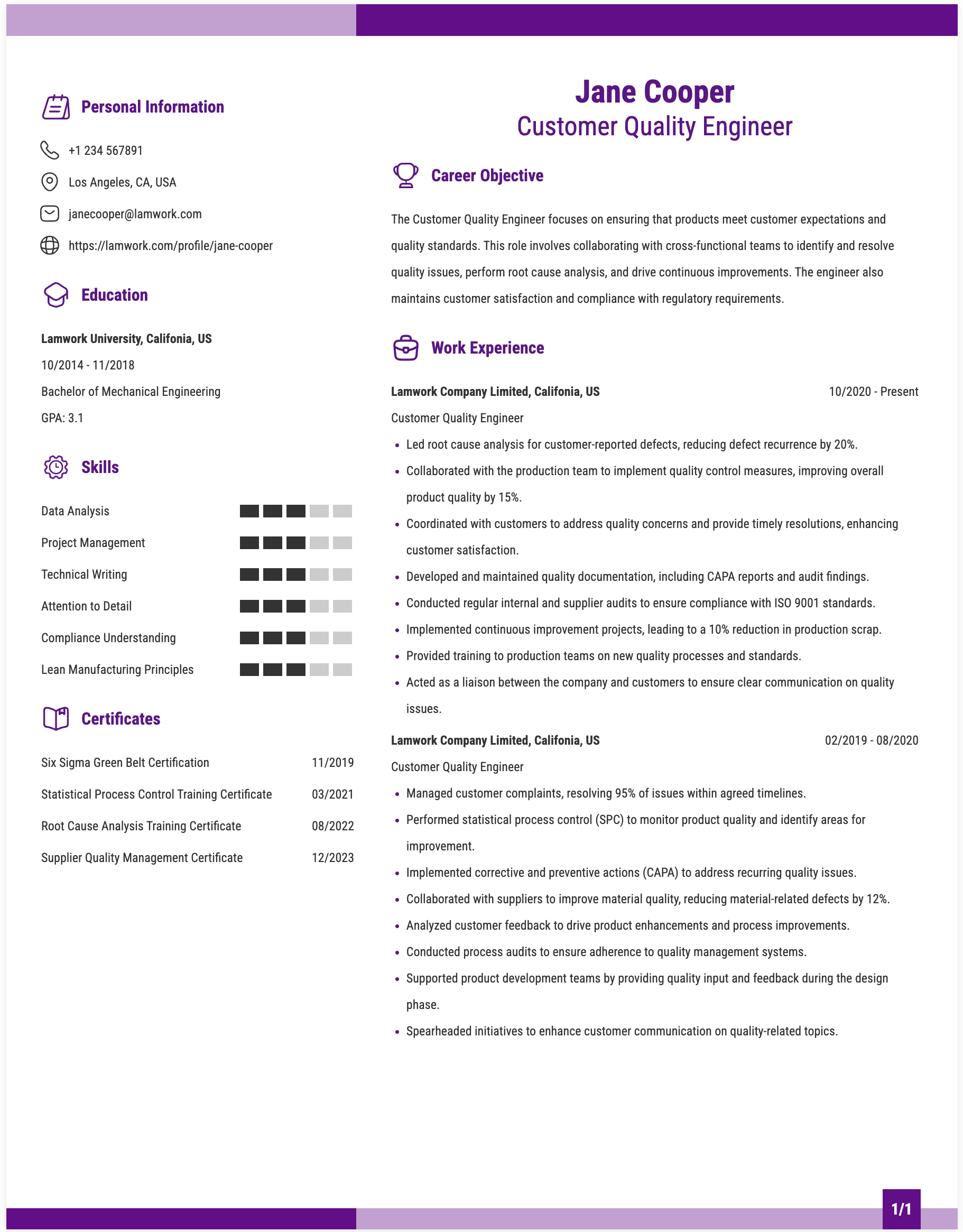
Tips for Customer Quality Engineer Skills and Responsibilities on a Resume
1. Customer Quality Engineer, Alpha Precision Manufacturing, Tacoma, WA
Job Summary:
- Own and drive key quality metrics
- Provide regular VP-level communication of product quality
- Monitor Outgoing Quality Control (OQC) and Final Quality Assurance (FQA) processes at OEM sites
- Monitor Customer Experience metrics in the field
- Lead quality critical issues and investigations
- Drive ongoing product improvements with Manufacturing, AppleCare, and Engineering teams
- Conduct periodic reviews of Field/Factory Quality Data with OEM partners
- Lead weekly Quality Improvement Forums
- Generate Product Health summaries regularly
- Conduct data collection and analysis to identify emerging quality issues and assess the impact of corrective actions
- Develop automated reporting tools for cross-functional communication
Skills on Resume:
- Quality Metrics (Hard Skills)
- VP-Level Communication (Soft Skills)
- OQC Monitoring (Hard Skills)
- Customer Metrics (Hard Skills)
- Issue Investigation (Soft Skills)
- Product Improvement (Soft Skills)
- Data Analysis (Hard Skills)
- Reporting Tools (Hard Skills)
2. Customer Quality Engineer, Beta Systems LLC, Dayton, OH
Job Summary:
- Communicate customer requirements and expectations within the company
- Works with the involved parties to enable the success of new product development and sub-projects within the product development schedule
- Work with Product Engineering, Design, and Manufacturing teams to determine root cause and assess potential reliability risks related to quality and yield excursions
- Review, refine and publish FA and 8D reports to customers for quality incidents
- Coordinate cross-functional teams and publish high-quality customer reports on yield and customer return issues
- Be responsive to customer needs
- Interact with customers and sales on quality topics and close all issues promptly
- Travel both domestically and internationally to customer and supplier sites to assist in product quality problem-solving and communication of issues
- Establish systems and processes to enhance responsiveness to customer requirements and assist in driving overall quality improvement for the company
- Review contracts including any changes, and complete the contract review summary form.
- Review compliance, SDRL, unique flow downs, PPQs & updated RIOSs need to be verified.
Skills on Resume:
- Communication (Soft Skills)
- New Product Development Support (Soft Skills)
- Root Cause Assessment (Hard Skills)
- FA and 8D Reporting (Hard Skills)
- Cross-Functional Coordination (Soft Skills)
- Customer Responsiveness (Soft Skills)
- Quality Problem-Solving (Hard Skills)
- Contract Review (Hard Skills)
3. Customer Quality Engineer, Cascade Engineering Solutions, Boulder, CO
Job Summary:
- Support local QMS training, deployment, and maintenance (ISO/IATF 16949)
- Support internal audit program and surveillance including meaningful Layered Process Audit (LPA) structure/content
- Champion Reverse PFMEA effort
- Lead/Support cross-functional PFMEA/Control Plan “Walks” to assess manufacturing practice versus requirements, and drive corrective actions
- Manage customer complaints and drive real root cause determination (0km and Warranty)
- Implement effective corrective/preventive actions with appropriate teams
- The primary interface for Customer Portal and Scorecard surveillance
- Guarantee Customer Specific Requirements (CSRs) are understood, and well executed, and adequate embedded tests are in place
- Lead critical manufacturing process improvement and problem-solving efforts
- Aspire to be a Subject Matter Expert (SME) for manufacturing processes
- Collaborate with key internal stakeholders to ensure high-quality new product release
Skills on Resume:
- QMS Training and Maintenance (Hard Skills)
- Internal Audit Support (Hard Skills)
- Reverse PFMEA Leadership (Hard Skills)
- PFMEA and Control Plan Walks (Soft Skills)
- Customer Complaint Management (Soft Skills)
- Corrective/Preventive Actions (Hard Skills)
- Customer Portal and Scorecard Monitoring (Hard Skills)
- Manufacturing Process Improvement (Soft Skills)
4. Customer Quality Engineer, Delta Tech Industries, Green Bay, WI
Job Summary:
- Host Customer Visits/Audits and submit quality assessments
- Update customers on time regarding the status of quality requests
- Train and help guide the plant in identifying and developing problem-solving methodologies to resolve quality issues.
- Assist and support the New Product Introduction (PPAP Submissions, APQP) programs for Tenneco at the site levels
- Conduct internal audits of the quality management system
- Maintain a list of customer-related issues and drive for improvements
- Assist with various activities for the plant such as training, tours, etc.
- Develop and maintain various quality systems for document control, metrics, and based forms
- Support Continuous Improvement activities throughout the organization
- Understand customer-specific requirements and how they translate to the plant
Skills on Resume:
- Customer Visits and Audits (Soft Skills)
- Quality Request Updates (Soft Skills)
- Problem-Solving Training (Soft Skills)
- New Product Introduction Support (Hard Skills)
- Internal Audits (Hard Skills)
- Customer Issue Management (Soft Skills)
- Quality System Development (Hard Skills)
- Continuous Improvement Support (Soft Skills)
5. Customer Quality Engineer, Echo Components Group, Des Moines, IA
Job Summary:
- Own and execute the roadmap to achieving best-in-world quality and warranty on assigned products
- Coordinate with warranty returns center personnel and other cross-functional partners to steward Energy and Charging products from failure triage through to permanent corrective action
- Stand up a variety of warranty, quality, and reliability processes to scale with the business
- Develop warranty, quality, and reliability metrics and dashboard capability with data science teams
- Collaborate with supplier quality and reliability teams to drive component-level improvements
- Provide quality and warranty perspectives and requirements for product and manufacturing process design
- Conduct field reliability analysis
- Coordinate and support customer care field programs
- Assist the Program Manager/Contract Administrators in reviewing RFPs/RFQs quality requirements ensuring all is clearly defined.
- Engage in compliance matrix activities, should a First Article Inspection (FAI) plan be required, and draft the plan for submittal/approval by the customer.
Skills on Resume:
- Quality and Warranty Roadmap Execution (Hard Skills)
- Cross-Functional Coordination (Soft Skills)
- Warranty and Quality Process Scaling (Hard Skills)
- Metrics and Dashboard Development (Hard Skills)
- Supplier Quality Improvement (Soft Skills)
- Product and Process Quality Requirements (Hard Skills)
- Field Reliability Analysis (Hard Skills)
- Customer Care Program Support (Soft Skills)
6. Customer Quality Engineer, Falcon Machining Corp, Knoxville, TN
Job Summary:
- Support new project development activities including Assembly PPAPs, Product/ Process Deviations and any other PDP-related activity.
- Coordinate project activities with the cross-functional team including Project Management, Sales, Engineering, Plant QA, Procurement and Manufacturing.
- Track performance with all main OEM customers and review those results monthly with the US Manufacturing plants and leadership.
- Follow up to ensure customer complaints are answered promptly.
- Support the Quality Management System (QMS) to ensure compliance with ISO/IATF16949 requirements.
- Support internal audits, follow up on audit findings and support the ISO/IATF6949 audit process and follow-up.
- Supporting region quality team daily operation.
- Responsible for maintaining customer return process and data analysis/reporting.
- Responsible for driving region quality service procedures to meet customer's requirements.
- Deeper data analysis to find the opportunity to improve the problem-solving process.
- Conduct and coordinate containment actions when quality concerns are identified by issuing QA Hold communications, conducting and/or coordinating sorting activities and following up to assure closure of the concern.
Skills on Resume:
- Project Development Support (Hard Skills)
- Cross-Functional Coordination (Soft Skills)
- OEM Performance Tracking (Hard Skills)
- Customer Complaint Follow-Up (Soft Skills)
- QMS Compliance (Hard Skills)
- Internal Audit Support (Hard Skills)
- Customer Return Process Management (Hard Skills)
- Containment Action Coordination (Soft Skills)
7. Customer Quality Engineer, Gamma Industrial Tools, Little Rock, AR
Job Summary:
- Test, and provide Quality Assurance, for finished inspection systems
- Perform special/supplemental test requirements in live demonstrations
- Perform data and statistical analysis for performance criteria
- Review Sales Orders, verifying machine configuration for features, options, and specials
- Work with Sales Ops, Marketing, and Applications Engineers to coordinate success criteria
- Class-100 cleanroom environment, with an understanding of cleanliness and contamination control
- Perform quality audits within manufacturing for compliance with established internal and external standards.
- Facilitate or lead kaizen events and 8Ds to drive continuous improvement and resolve significant deviations from the standard.
- Use lean Six Sigma methodology to drive continuous improvement projects.
- Provide governance of corrective and preventative actions.
- Collaborate with Supplier Quality Engineers and Onsite Technical Representatives to contain Supplier non-conformance and ensure 8D effectiveness.
Skills on Resume:
- Finished Inspection QA (Hard Skills)
- Live Demonstration Testing (Hard Skills)
- Data and Statistical Analysis (Hard Skills)
- Sales Order Review (Hard Skills)
- Success Criteria Coordination (Soft Skills)
- Cleanroom and Contamination Control (Hard Skills)
- Quality Audits (Hard Skills)
- Continuous Improvement Leadership (Soft Skills)
8. Customer Quality Engineer, Horizon Tech Solutions, Augusta, GA
Job Summary:
- Responsible for helping the regional CQE team with QTS/QAS generating and customer sample handling.
- Follow-up QTS# priority and highlight to RCQE team to get W/W CQE’s support promptly.
- Provide CQE information Matrix and update CQE’s operation indices monthly & consolidate team metrics Monthly/quarterly.
- Periodically attend Customer Quality review meetings, and execute activities of CQE team functional group decisions to achieve customer quality requirements.
- Aid in the investigation of Customer quality non-conformances caused by manufacturing.
- Mentor and train Quality Technicians on existing and new standards as well as adoption of industry best-known methods.
- Ensure compliance with in-house and/or external specifications and standards (i.e. GMP and ISO standards).
- Provide a quality interface for customers, own the relationship with the customer’s quality department to understand needs and expectations, help to ensure and increase customer satisfaction
- Support the business team in specification and purchase order reviews regarding quality-related customer requirements and support negotiation with the customer
- Participate in development projects and own work packages
- Provide quality support during the development phases, ensuring appropriate test planning and validation and other APQP activities
Skills on Resume:
- Customer Sample Handling (Hard Skills)
- QTS Priority Follow-Up (Hard Skills)
- CQE Metrics Consolidation (Hard Skills)
- Customer Quality Review Participation (Soft Skills)
- Non-Conformance Investigation (Hard Skills)
- Quality Technician Mentorship (Soft Skills)
- Compliance with Standards (Hard Skills)
- Quality Support in Development (Hard Skills)
9. Customer Quality Engineer, Innovate Manufacturing, Billings, MT
Job Summary:
- Responsible for post-market quality-related activities.
- Design, implement and maintain service center processes and methods for servicing finished products.
- Build strong relationships with global service center staff.
- Managing customer complaints, reviewing for internal investigations, customer reporting and vigilance escalations ensuring we meet regulatory compliance and standards.
- Engineering investigations for field product failures.
- Review post-market field and service activity data to detect trends and recommend actions to improve the usability, performance and safety of devices when necessary.
- Determine whether to launch a complaint investigation by the design authority, initiate containment actions and/or launch corrective actions based on risk and root cause.
- Take a leadership role in closing complaints, and facilitating activities such as investigations, containment actions, corrective actions and inter-regional regulatory reporting.
- Responsible for planning, implementing and managing compliance of servicing processes with internal and external safety, quality and regulatory standards requirements for global distribution.
- Works closely with research and development on any suggested design changes and reports defects and tracks until resolution.
- Interact with product development teams to ensure quality and operation input for new products.
Skills on Resume:
- Post-Market Quality Activities (Hard Skills)
- Service Center Process Design (Hard Skills)
- Global Relationship Building (Soft Skills)
- Customer Complaint Management (Soft Skills)
- Field Product Failure Investigations (Hard Skills)
- Trend Detection and Improvement Actions (Hard Skills)
- Complaint Investigation Leadership (Soft Skills)
- Compliance Management (Hard Skills)
10. Customer Quality Engineer, Jetstream Solutions, Reno, NV
Job Summary:
- As part of the Project Team, attend all NPI project meetings and guarantee the completion of quality-related deliverables
- Ensure that Customer requirements are implemented
- Define the quality control plans (pre-series, mass production) for different product families according to existing F-M standards and specific Customer requirements
- Periodically monitor customer portals to check plant performance (scorecard) and the presence of updated CSR (Customer Specific requirements)
- Manage Customer complaints, coordinate problem-solving activities (as part of the CCEM team) and provide regular feedback to the Customers
- Ensure communication and prompt/reliable reporting about Customer complaints using the appropriate tools
- Prepare and manage customer visits/audits at the plant
- Attend meetings at customer premises, when required and maintain regular contact and relationship
- Manage both internal and 3rd party sorting activities of finished products, aimed at ensuring their proper execution and relevant recording (including costs)
- Verify and understand quality issues, manage and coordinate customer complaints along with other team members, and provide status updates to the customer
- Determine adequate containment activities by customer requirements and guarantee the implementation of corrective actions and improvements
Skills on Resume:
- NPI Project Meeting Participation (Soft Skills)
- Customer Requirement Implementation (Hard Skills)
- Quality Control Plan Definition (Hard Skills)
- Customer Portal Monitoring (Hard Skills)
- Complaint Management and Problem-Solving (Soft Skills)
- Customer Complaint Reporting (Hard Skills)
- Customer Visit and Audit Management (Soft Skills)
- Containment and Corrective Action Implementation (Hard Skills)
11. Customer Quality Engineer, Keystone Fabrication, Wichita, KS
Job Summary:
- Establish individual goals, strategies, and procedures
- Assists with E2E SC Client Facing Quality customer relationships to drive continuous improvements using data analytics
- Review customer’s quality KPIs and help drive product performance to meet those targets using trend analysis
- Analyze end-to-end customer data and identify opportunities for improvements
- Drive consistency in product performance across customer platforms in the local manufacturing site and Data Center processes for Cloud Service Provider Products.
- Learn to make quick, effective decisions and prioritize projects to focus on the ones that have the highest impact on the business
- Facilitate internal and external meetings to understand quality data
- Develop and document quality metrics and create presentations/reports for the customers and team
- Support the existing CQEs in their customer-facing roles and grow the capabilities to take on customer-facing conversations
- Co-work with global teams in sharing customer data
- Serve as the team leader for a multi-disciplined team to solve customer issues
- Drive successful new product ramps that would achieve quality and reliability goals
Skills on Resume:
- Goal and Strategy Development (Soft Skills)
- E2E SC Client Relationship Support (Soft Skills)
- Quality KPI Review and Analysis (Hard Skills)
- Customer Data Improvement Analysis (Hard Skills)
- Product Performance Consistency (Hard Skills)
- Decision-Making and Prioritization (Soft Skills)
- Meeting Facilitation and Data Sharing (Soft Skills)
- Quality Metrics Development (Hard Skills)
12. Customer Quality Engineer, Luna Precision Corp, Rochester, MN
Job Summary:
- Undertake specified activities in managing the customer interface for all aspects of product quality.
- Take responsibility for direct customer contact
- Generate data for the process of reporting and communicating with internal and external customers up to the director level on quality topics, customer satisfaction and key performance indicators.
- Maintain customer satisfaction in all aspects of quality through achievement of customer-specified deliverables.
- Supports and complies with established Company’s Corporate Principles and goals.
- Understand and comply with Quality requirements such as automotive requirements
- Monitor manufacturing processes and assess product quality to determine adequacy, capability and ability to comply with customer specifications and the company’s specifications.
- Drive alignment within business units to meet quality requirements for products, processes and services
- Act as the primary quality representative, beginning with new process development and continuing from new product development through product end-of-life
- Act as the focal point for customer returns and customer communication for quality-related issues
- Develop and maintain documents and procedures related to quality standards, risk analysis, lessons learned from product recalls, product audits, field returns and repairs, complaints, scrap, and rework, and retain documented information as evidence.
Skills on Resume:
- Customer Interface Management (Soft Skills)
- Direct Customer Contact (Soft Skills)
- Data Generation and Reporting (Hard Skills)
- Customer Satisfaction Maintenance (Soft Skills)
- Quality Requirement Compliance (Hard Skills)
- Manufacturing Process Monitoring (Hard Skills)
- Quality Alignment Across Units (Soft Skills)
- Document and Procedure Development (Hard Skills)
13. Customer Quality Engineer, Matrix Components, Mobile, AL
Job Summary:
- Responsible for championing high quality for Qualcomm’s strategic Korean customers
- Drive cross-functional technical teams to identify containment and determine the root cause for Customer issues
- Be the San Diego Quality voice for both internal teams and Korean customers
- Work closely with the customer to fully understand their business from a quality perspective
- Escalate potential issues to management to avoid customer disruption and ensure smooth operation at the customer’s side
- Provide cross-functional team with customer priorities to properly address the issues according to their criticality
- Oversee the RMA process and drive to minimize RMA cycle time
- Write and deliver customer-facing presentations to communicate technical updates and resolutions as well as periodic RMA status
- Resolve complex issues through in-depth data mining, hands-on technical analysis and strong technical leadership
- Determine root cause and make the appropriate decisions based on well-thought-out data and facts
- Improve efficiency via metrics and KPI optimization and monitoring such as RMA cycle time, systemic failure mechanisms, issues affecting multiple customers, DPPM, etc
Skills on Resume:
- Customer Quality Champion (Soft Skills)
- Cross-Functional Issue Resolution (Soft Skills)
- Quality Voice for Internal and External Teams (Soft Skills)
- Customer Business Understanding (Soft Skills)
- Issue Escalation and Prevention (Soft Skills)
- RMA Process Oversight (Hard Skills)
- Customer Presentation Delivery (Soft Skills)
- Data-Driven Root Cause Analysis (Hard Skills)
14. Customer Quality Engineer, Nova Engineering, Syracuse, NY
Job Summary:
- Following customers’ quality experience based on statistical data, communication with the global engineering team, sales network, and customers directly
- Utilizing the failure analysis platform to do statistical analysis and find out the weak point of product or batch issue
- Collecting and investigating the background of customer failure, and based on background information, design and carry out the failure analysis plan
- Managing the electrical failure analysis on challenging field failure cases
- Finding out the root cause of the significant cases that have a great impact on product quality, where deep product knowledge of power electronics is needed
- Recording test results into the global failure analysis platform
- Compiling professional failure analysis reports
- Responsible for one or more customer accounts, being the visible face of the company before them and transferring their needs and requirements internally to the business.
- Participate in the definition of the quality strategy and lead some of the initiatives and work teams created to achieve the specific objectives defined, and aligned with that strategy.
- Lead the actions for the resolution of quality claims or incidents related to customers, ensuring that they are effective, with the least possible impact on the operations of the business.
Skills on Resume:
- Customer Quality Experience Tracking (Soft Skills)
- Failure Analysis and Statistical Review (Hard Skills)
- Failure Investigation Planning (Hard Skills)
- Electrical Failure Analysis (Hard Skills)
- Root Cause Identification (Hard Skills)
- Test Result Recording (Hard Skills)
- Failure Analysis Reporting (Hard Skills)
- Customer Account Management (Soft Skills)
15. Customer Quality Engineer, Orion Quality Systems, Fargo, ND
Job Summary:
- Implement and ensure compliance with all procedures described in the Business Management System (BMS).
- Worked within the aerospace or automotive sector
- Point of contact for the customers
- Ensure all customer project gate reviews are supported and the customer quality concerns shared throughout the review process
- Manage customer containment activities within the company and potentially at the customer locations
- Respond to customer concerns/ complaints by implementing full containment actions, full analysis, poka-yokes and executing short and long-term countermeasures.
- Lead problem-solving activities with each value stream, utilizing Ishikawa, 5 Why Shipped/Made techniques.
- Review and update quality documentation to communicate lessons learned from quality concerns.
- Ensure all necessary systems and procedures are in place to satisfy the customer requirements, visits and audits.
- Represent the company on customer plant visits and/ or conference calls/ meetings. Including carrying out the necessary actions.
- Identify systematic issues and drive continuous improvement across the business units
- Balance business unit customer satisfaction indices and customer quality indices
Skills on Resume:
- BMS Compliance Implementation (Hard Skills)
- Aerospace or Automotive Experience (Hard Skills)
- Customer Point of Contact (Soft Skills)
- Project Gate Review Support (Soft Skills)
- Customer Containment Management (Hard Skills)
- Complaint Response and Countermeasures (Hard Skills)
- Problem-Solving Leadership (Soft Skills)
- Continuous Improvement Initiatives (Soft Skills)
16. Customer Quality Engineer, PrimeTech Manufacturing, Richmond, VA
Job Summary:
- Keep up to date on all retailer quality/operations requirements and ensure they are included in the internal processes
- Ensure all retailer quality/operations requirements are met and resolve any deficiencies and corrective action requests
- Manage quality/operations communications with retailers, including the use of retailer portals and systems
- Perform first article inspections (FAIs) and lead cross-functional FAI reviews, document results, and drive corrective actions
- Develop processes and work instructions for internal and supplier processes
- Coordinate failure analysis of customer returns, analyze customer complaints, return rates and failure analysis data, and work with engineering to drive continuous improvement
- Participate in the supplier selection process, representing Product Quality, of logistics providers, warehouses, and packaging suppliers
- Perform process and technical supplier assessments for both quality and code of conduct (labor, ethics, health, safety and environmental) compliance
- Qualify supplier facilities, processes and products through supplier assessments and production part approval process (PPAP)
- Review and approve change orders (ECOs, MCOs, DEVs)
- Drive continuous improvement of suppliers based on supplier assessment results, quality performance, technical support, and delivery
- Review and approve supplier corrective actions for the adequacy of root cause identification and corrective actions using the 8D process
- Drive the use of statistical tools and methods within supplier facilities including statistical process control, capability analysis, gage repeatability & reproducibility, and design of experiments
Skills on Resume:
- Retailer Requirements Management (Hard Skills)
- Quality/Operations Deficiency Resolution (Soft Skills)
- Retailer Portal Communication (Hard Skills)
- First Article Inspection Leadership (Hard Skills)
- Process and Work Instruction Development (Hard Skills)
- Customer Return Analysis (Hard Skills)
- Supplier Selection and Assessment (Hard Skills)
- Supplier Corrective Action Review (Hard Skills)
17. Customer Quality Engineer, Quantum Industries, Lincoln, NE
Job Summary:
- Analyze return goods data, consumer reviews, and call center data to provide support for continuous improvement activities and new product development
- Champion continuous improvement activities of manufacturing processes and consumer products
- Conduct cross-functional meetings on continuous improvement activities and drive action items to closure
- Gathers data and authors' reports to indicate progress toward company goals and objectives
- Lead root cause analysis (8D/5 Why)
- Supports the quality function on new product development projects.
- Supports Supplier Quality in all phases of interaction with suppliers, including the development of new parts and assemblies, improvement of existing parts and assemblies and Corrective Action when necessary.
- Participates as an active member in the development, planning and formulation of policies, objectives, and goals
- Inspect and analyze components and products for conformance to specifications
- Develop inspection instructions and Equipment
- Perform system audits to ensure procedures are being followed
- Update procedures, statistical techniques, testing mechanisms, and equipment
Skills on Resume:
- Return Data and Review Analysis (Hard Skills)
- Continuous Improvement Leadership (Soft Skills)
- Cross-Functional Meeting Facilitation (Soft Skills)
- Progress Reporting (Hard Skills)
- Root Cause Analysis (Hard Skills)
- New Product Development Support (Soft Skills)
- Supplier Quality Support (Hard Skills)
- Inspection and Conformance Analysis (Hard Skills)