Published: September 13, 2024 – The Customer Quality Engineer manages customer expectations regarding product quality, handles inquiries, and provides technical documentation to ensure alignment with specifications. This role involves overseeing global service systems, addressing product failures, and managing customer returns while driving quality improvement initiatives. Additionally, the engineer analyzes customer satisfaction data, develops strategies for quality enhancement, and coordinates with legal and business teams on quality agreements.
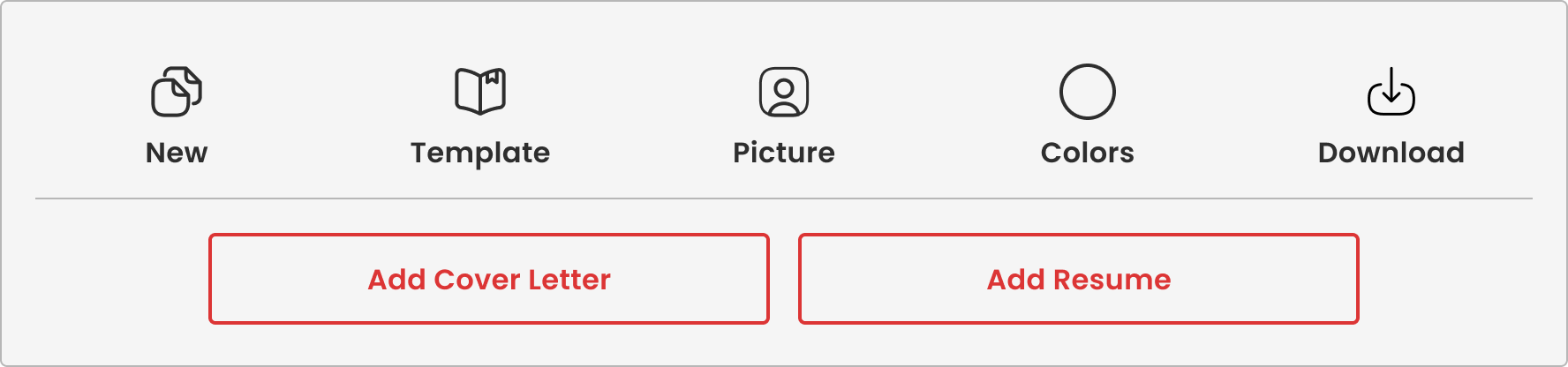
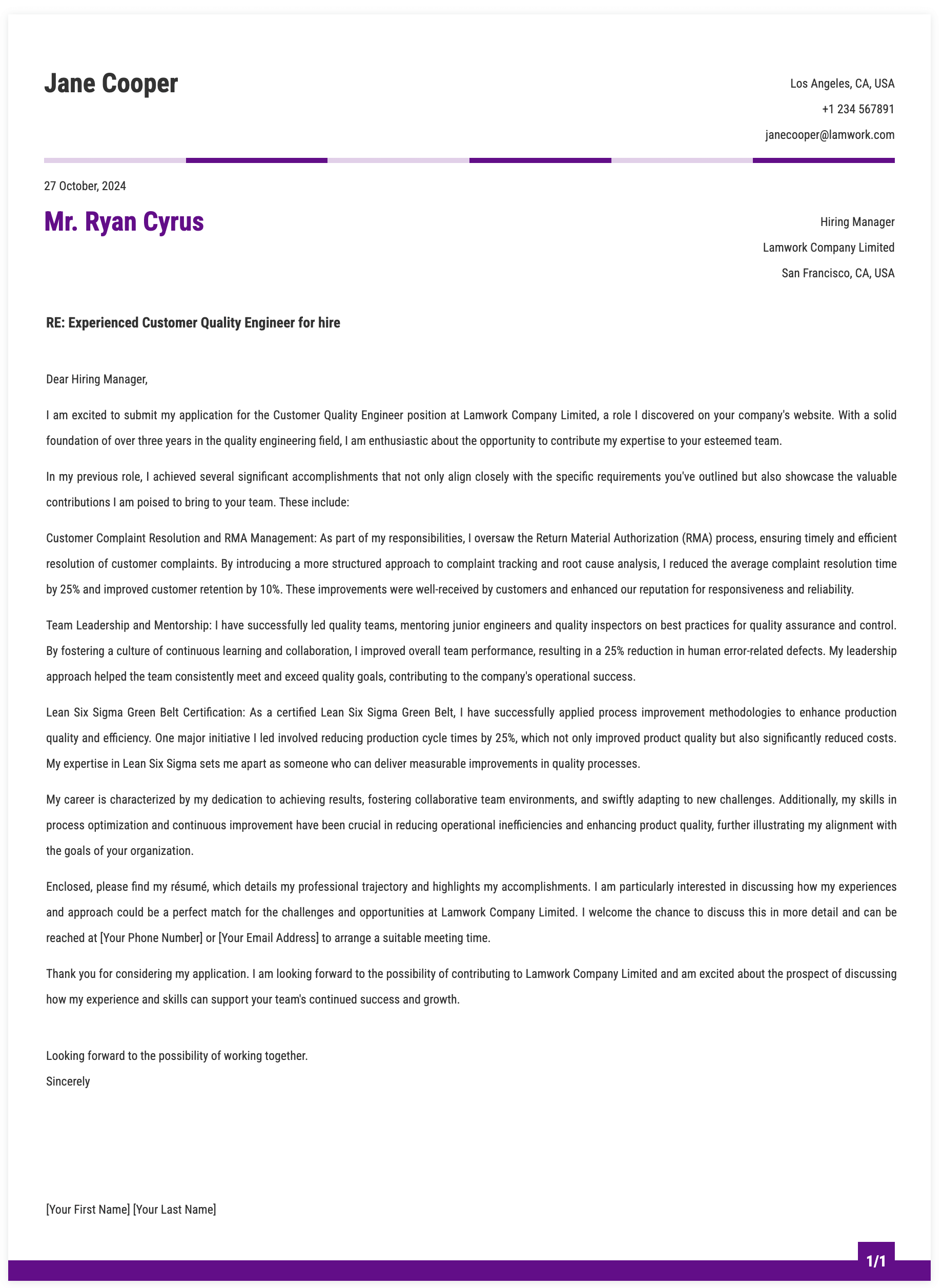
An Introduction to Professional Skills and Functions for Customer Quality Engineer with a Cover Letter
1. Essential Functions for Customer Quality Engineer Cover Letter
- Support the Product Group on customer communication by providing failure analysis and 8D reports
- Define troubleshooting procedures for field failures and field returns based on product requirements
- Perform failure analysis on returned parts, sub-assembly and full systems
- Apply problem-solving methodology and work closely with other business functions to accomplish root cause investigation (8D)
- Define and implement test procedure and test setup to validate the failure mode and validate root cause identification
- Define and map the failure modes across the installed base, make a Pareto analysis and follow up on corrective action execution
- Report in an accurate way the required metrics and KPI related to field failure
- Propose and validate corrective and preventive actions in collaboration with other business functions
- Perform failure analysis on part returned from the field and escalate to engineering when necessary
- Provide input for new product development and new product requirements to improve customer satisfaction
- Be an active part of the quality improvement process reporting lessons learned
- Support internal and external repair centers to define the troubleshooting and failure analysis procedure
Skills: Failure Analysis, Root Cause Investigation, 8D Problem-Solving, Troubleshooting Setup, Test Development, Pareto Analysis, KPI Reporting, Quality Improvement
2. Core Competence for Customer Quality Engineer Cover Letter
- Communicate customer requirements and expectations within Qorvo
- Communicates product reliability testing status to the customer
- Works with the involved parties to enable the success of new product development and sub-projects within the product development schedule
- Work with Product Engineering, Design, and Manufacturing teams
- Determine root cause and assess potential reliability risks related to quality and yield excursions
- Review, refine and publish FA and 8D reports to customers for quality incidents
- Coordinate cross-functional teams and publish high-quality customer reports
- Be responsive to customer needs
- Interact with customers and sales on quality issues and close all issues on time
- Travel to customers and supplier sites to assist in product quality problem-solving and communications, both domestic and international
- Establish systems and processes to enhance responsiveness to customer requirements and assist in driving overall quality improvement for Qorvo
Skills: Customer Requirements Communication, Product Reliability Updates, New Product Development Support, Cross-Functional Collaboration, Root Cause Analysis, FA and 8D Reporting, Quality Issue Resolution, Customer Quality Problem-Solving
3. Success Indicators for Customer Quality Engineer Cover Letter
- Develop a strategy to manage specific customer accounts
- Lead customer quality issue resolution
- Interacts with the customer to satisfy their requirements
- Understand customer-specific requirements
- Maintain daily quality (PPM/other KPI targets) and cost (internal/external costs) data for all requirements.
- Actively engage the site production team to drive manufacturing improvements
- Support new business opportunities and new product development programs
- Gather warranty data, generate warranty charts, analyze trends and prepare warranty reports for each assigned OEM to reduce warranty cost
- Support change management programs customers, and at plant level.
- Fulfill/Submit all new parts submission (PPAP) requirements
- Interact closely with cross-functional Teams to perform Advanced Product Quality Planning for new product launches and Advanced Quality Planning for product and/or process changes.
Skills: Customer Account Strategy, Quality Issue Resolution, Customer Interaction, KPI and Cost Tracking, Manufacturing Improvement Support, Warranty Data Analysis, Change Management Support, New Product Quality Planning
4. Primary Focus for Customer Quality Engineer Cover Letter
- Assess Operations needs and deliverables required for successful market entry in the UK and roll out together with HQ Operations team
- Roll up your sleeves and help set up local Operations processes from the ground up
- Hire and manage a team of operations specialists to scale business operations in the UK
- Be the first point of contact for customers and accompany them throughout the entire onboarding process [during the launch phase only]
- Excite customers during every interaction and support them with expertise
- Perform Know Your Customer (KYC) analysis and prepare customer due diligence documents for customer acceptance [during the launch phase only]
- Advise and support customers via telephone, e-mail, or chat and process their inquiries [during the launch phase only]
- Drive the continuous optimization of processes in the operations department
- Interface with key customers to ensure customer satisfaction and review requirements to meet customer specifications
- Work with the internal technical organizations and teams (such as design, assembly, and product testing) to ensure high-quality products are achieving
Skills: Operations Setup, Team Management, Customer Onboarding, KYC Analysis, Customer Support, Process Optimization, Customer Satisfaction, Cross-Functional Collaboration
5. Key Strengths for Customer Quality Engineer Cover Letter
- Improving customer service processes and operating models to support current and future customer service operations, sales and business needs.
- Improving operations by monitoring efficiency and productivity, identifying and resolving problems, preparing and completing action plans
- Preparing performance reports and insights by collecting, analyzing, and summarizing data and trends
- Accomplishing human resource objectives by developing and harmonizing recruiting, onboarding, training and coaching practicalities
- Ensuring the maximum use of contact center technology, ie. WFM, contact handling system, chatbot
- Supervisor duties and leading the well-being at work process for one's team
- Participating in Product teams to represent the Voice of the Customer and driving key decisions and priorities to meet Customers’ quality expectations.
- Leading multi-functional quality teams and continuous improvement programs to enhance product quality
- Managing customer communications including PCN, FA reports, Quality Alerts, etc
- Developing quality metrics to measure and improve business outcomes and customer experience
- Creating and maintaining a system to track customer quality-related inquiries and responses.
Skills: Customer Service Process Improvement, Operational Efficiency Monitoring, Performance Data Analysis, HR and Training Management, Contact Center Technology Utilization, Team Leadership, Voice of Customer Representation, Quality Metrics Development
6. Expertise Areas for Customer Quality Engineer Cover Letter
- Review performance metrics and prioritize data-driven improvement activity
- Conduct Root Cause and Corrective Actions based on internal metrics and customer Quality Notifications
- Guide production leads in continuous quality improvement activities based on lean principles
- Review customer scorecards and target areas of concern
- Conduct internal QMS audits to monitor conformance and determine areas for improvement
- Set quality goals and improvement plans
- Take responsibility for reviewing/Improving Control plans
- Interface with customers for completing the delivery of the order including presentation of the lot data packages, FAIs if needed and any PO changes.
- Verify all quality contractual requirements have been met and lessons learned from the customer orders have been documented.
- Participate in any PDR or CDRs.
- Attend all sales order closeout meetings
Skills: Data-Driven Improvement, Root Cause and Corrective Actions, Continuous Quality Improvement, Customer Scorecard Review, QMS Auditing, Quality Goal Setting, Control Plan Review, Customer Order Management
7. Performance Expectations for Customer Quality Engineer Cover Letter
- Supports customer accounts through direct customer interaction
- Responding to customer issues quickly and effectively
- Maintaining customer contracts from product development through production
- Oversee analysis of products in response to customer complaints
- Determine solutions to production quality problems to meet customer requirements
- Handles Production Part Approval Process and provides documents to customer
- Conducts measurement system analysis and statistical process control for key processes
- Ensures a smooth and timely launch of new and changed products
- Handles customer returns and uses company tools to provide frequent status updates to affected customers
- Works effectively with test, design, product, and planning engineers, regional quality engineers, regional planners, regional technical sales representatives and marketing representatives to solve customer challenges and provide answers
Skills: Customer Account Support, Issue Resolution, Contract Management, Complaint Analysis, Production Quality Solutions, PPAP Documentation, Statistical Process Control, Product Launch Management
8. Scope of Work for Customer Quality Engineer Cover Letter
- Lead quality activities to improve customer quality and satisfaction, while reducing warranty costs, claims, early failures, customer complaints and technical service requests.
- Provide a positive customer experience through building strong relationships through timely problem resolution.
- Demonstrate leadership by providing prompt technical and cross-functional problem-solving support to UCA and the dealer network
- Initiating and leading customer quality and service investigations, effective root cause analysis and complete problem resolution.
- Collaborate with Warranty, Engineering, Manufacturing Quality, Supplier Quality and other teams to ensure field issues are resolved promptly through approved methodologies such as the 8D process.
- Maintain pipeline of customer quality and product support improvement opportunities, prioritize and manage multiple projects, and complete QAR activities in an expedited timeframe with a persistent focus on customer satisfaction.
- Obtain feedback from the field, and participate in field visits as appropriate, to investigate product and service issues, and follow up with specific actions to resolve the issues.
- Review conformance to customer requirements, and improvement opportunities and ensure products and processes meet requirements.
- Develop relationships with dealers and internal and external customers that foster a high level of commitment to constant improvement in product quality and support.
- Lead/Direct customer issues to closure by gathering appropriate teams and leading problem-solving using tools
Skills: Customer Quality Improvement, Warranty Cost Reduction, Technical Problem Resolution, Root Cause Analysis, Cross-Functional Collaboration, Project Prioritization, Field Issue Investigation, Customer Relationship Building
9. Standards for Customer Quality Engineer Cover Letter
- Organizes designs, implements and maintains quality assurance protocols and methods for processing materials into partially finished or finished products
- Key participant in planning, implementing and managing compliance of manufacturing and production processes with internal and external safety, quality and regulatory standards requirements for worldwide distribution
- Organizes design methods and procedures for inspecting, testing and evaluating the precision and accuracy of production processes, production equipment and finished products
- Collaborates on analysis of reports and production data to identify trends and recommend updates or changes to quality standards and procedures when necessary
- Develops methods for testing, sampling and training
- Act as an internal consultant by providing technical guidance on most complex projects
- Works with quality inspection supervisors to train and oversee inspectors in their use of control forms, and procedures, and correcting quality problems
- Coordinates project teams to ensure a successful launch of new products
- Key participant in planning, implementing and managing compliance of manufacturing and production processes with internal and external safety, quality and regulatory standards requirements for worldwide distribution
- Works with quality inspection supervisors to train and oversee inspectors in their use of control forms, and procedures, and correcting quality problems
- Key member of FMEA Development serving as key member liaison between Manufacturing Engineering and Design Engineering.
Skills: Quality Assurance Protocols, Compliance Management, Production Process Evaluation, Data Trend Analysis, Testing and Sampling Methods, Technical Guidance, Inspector Training, New Product Launch Coordination
10. Outcomes for Customer Quality Engineer Cover Letter
- Work actively with customer-facing teams to set expectations with customers regarding released product quality including manufacturing controls and capabilities, complaint processes and expectations, specifications and revisions.
- Interface directly with customers as the lead contact for all customer issues and inquiries
- Share appropriate technical documentation with customers including customer drawings/revisions and formal company documents and specifications.
- Manage an active internal and 3rd party onsite service system to respond to customer needs for CPC customers around the globe and in multiple industries.
- Manage communications with customers on improvement initiatives to address customer issues from product failures or audits.
- Manage technical disposition of all customer product returns.
- Collect, review and manage customer satisfaction data and establish data sources for customer satisfaction data.
- Partner with senior leaders to establish company strategies based on this data.
- Drive internal strategies for product quality that meet the needs and requirements of all industries and standards in which product is utilized.
- Coordinate with legal and business leaders for all customer quality agreements.
- Mentor cross-functional personnel on the customer-issue process.
Skills: Customer Issue Resolution, Technical Documentation Sharing, Onsite Service Management, Improvement Initiative Coordination, Product Return Management, Customer Satisfaction Data Analysis, Product Quality Strategy, Cross-Functional Mentoring
What Are the Qualifications and Requirements for Customer Quality Engineer in a Cover Letter?
1. Account Management Best Practices for Customer Quality Engineer Cover Letter
- Strong verbal and written communication skills
- Demonstrated strong analytical and problem-solving skills
- Ability to work in teams and collaborate effectively with people in different functions
- Ability to take the initiative and drive for results
- Strong time management skills that enable on-time project delivery
- Ability to work effectively in an interrupt-driven, fast-paced and rapidly changing environment
- Demonstrated ability to build strong, influential relationships
- Ability to interface and build relationships with customers and internal TI functions – both in the business and in the fab
- A strong background in Electrical Engineering, Physics, or related engineering fields of study
- Ability to manage customer expectations, and drive for results within TI to ensure that customer expectations are met
- Have a passion for meeting customer needs and be able to influence without direct authority
Qualifications: BS in Mechanical Engineering with 2 years of Experience
2. Collaborative Teamwork for Customer Quality Engineer Cover Letter
- Experience in a high technology/high volume manufacturing environment
- Experience with Power BI, Oracle, and other commercial databases
- Must have proficiency in data synthesis
- The ability to interpret design prints
- Experience working with a wide range of Quality Tools
- Exceptional customer interface and problem-solving skills
- A good working knowledge of risk assessment (fault tree analysis, FMEA) and mitigation
- Excellent technical communication and project management skills
- Ability to interface with multiple internal functions and external parties in all global regions
- Must have strong communication skills
Qualifications: BA in Industrial Engineering with 3 years of Experience
3. Key Achievements for Customer Quality Engineer Cover Letter
- Related experience in the areas of server design and deployment
- Experience in product quality, reliability, or product engineering, preferably in semiconductor logic SOC.
- Possess strong technical knowledge of server products, and architecture, and understanding of AMD components.
- Experience with semiconductor manufacturing and test flow, including fab, bump, assembly, and test.
- Strong understanding of end-to-end system/component/process interactions
- Customer-facing experience with the ability to network, build relationships, and drive effective decision-making across multiple functions and levels within the organization.
- Highly organized, able to prioritize, and juggle multiple work streams to tight deadlines
- Experience dealing with customers as the focal point for quality discussion and continuous improvement.
- Effective presentation and communication skills, good negotiation skill
- Ability to work both independently as well as in teams and across business units to accomplish tasks on time
- Fluent in both spoken and written English and Chinese.
Qualifications: BS in Quality Engineering with 12 years of Experience
4. Industry Knowledge for Customer Quality Engineer Cover Letter
- Customer quality experience in electronics products.
- Experience in quality operation or System Data Center and Automotive Industry Support
- Working experience in PCBA Testing/Troubleshooting processes.
- Knowledge of SMD (Surface Mount Device), SMT (Surface Mount Technology), and Assembly manufacturing practices and controls.
- Knowledge of Data Center operation and management, familiar with server architecture and technology.
- Strong ability in data analysis and familiarity with QA analysis tools.
- Strong experience in structured problem-solving
- Knowledge of ISTS 16949 requirements and Statistical Quality Control.
- Knowledge of standard quality tools such as FMEA (Failure Modes Effect Analysis), SPC (Statistical Process Control), 8D, etc.
- Good verbal and written communication skills in English and Chinese.
Qualifications: BS in Manufacturing Engineering with 4 years of Experience
5. Experience and Qualifications for Customer Quality Engineer Cover Letter
- Experience in the field of quality management in a production plant
- Experience in the automotive or electronics industry
- Good command of English
- Knowledge of the quality requirements of the automotive industry and OEM customers
- Practical knowledge of tools Control Plan, Flow Diagram, FMEA, MSA, PPAP, 8D, 5Why
- Good knowledge of MS Office (Word, Excel, PowerPoint, Outlook)
- Excellent work organization and problem-solving skills
- The ability to conduct audits
- Excellent communication skills, able to speak clearly and persuasively in positive or negative situations
- Have Continuous Improvement Mindset – Constantly challenge the status quo, leverage technology advancement to create positive changes
Qualifications: BA in Operations Management with 2 years of Experience
6. Technical Expertise for Customer Quality Engineer Cover Letter
- Experience in a quality role, in the semiconductor industry and customer communications experience
- Experience with applicable quality tools such as Pareto, FMEA’s, SPC/SQC, histograms, trend analysis, process mapping, design of experiments, cause and effect diagrams, 8D problem-solving methodology
- Thorough understanding of requirements associated with the ISO 9001 quality standard.
- Proficient and practiced level of Business English both Written and Spoken.
- Strong communication skills with leadership ability to drive all action
- High accountability to achieve the goal
- Excellent customer management skills, with problem-solving skills
- Must have solid analysis skills, and result-driving
- Accountability – Hold high-performance standards for self and others, do not avoid making difficult decisions when needed
- Strong teamwork, and able to exhibit objectivity and openness to others' views
Qualifications: BS in Electrical Engineering with 5 years of Experience
7. Problem-solving Abilities for Customer Quality Engineer Cover Letter
- Demonstrate skills in preventive quality methods and compliance, and statistical data analysis, critical thinking, structured problem solving (8D)
- Demonstrate skills in the use of metrics to identify opportunities and business process improvement.
- Demonstrate skills in managing customer quality issues
- Experience setting up the product, and process quality control for the equipment assembly line.
- Knowledge of regulatory and compliance, experience in product, process, and system audit.
- Strong communication, leadership, and management skills.
- Experience in Functional management, compliance Engineering, Operations, Quality, or Reliability.
- Experience in quality and manufacturing systems, business process improvement tools, and problem-solving.
- Experience with the ISO 9001 standard is required.
- Experience managing critical customer communications.
- Experience with Lean, 6S, zero-defect manufacturing processes, inspection methods, and tools.
Qualifications: BS in Materials Science Engineering with 9 years of Experience
8. Training and Certifications for Customer Quality Engineer Cover Letter
- Experience in the Semiconductor field or Quality experience
- Broad technical knowledge of semiconductor wafer fab, assembly and test processes
- Familiarity with Automotive quality, industry standards including ISO 9001 and IATF16949, 8D problem solving, FMEAs, Lean principles and Six Sigma methodology
- Excellent written and verbal communication skills
- The ability to explain complex technical issues to customers
- Excellent problem-solving skills
- Must be team-oriented, collaborative, and a willingness to learn
- Excellent project management skills
- The ability to prioritize the workload, proactively address problems and meet deadlines
- Ability to travel to suppliers, subcontractors, and customers (domestic and international)
Qualifications: BS in Supply Chain Management with 4 years of Experience
9. Key Qualifications for Customer Quality Engineer Cover Letter
- Experience with diverse skills (Process Engineering, Technology Development, Reliability, Process Integration, Project management)
- Experience in semiconductor manufacturing process and quality systems
- Strong communication skills, both verbal and written
- Strong organizational skills
- Demonstrated ability to manage multiple tasks simultaneously and able to react to shifting priorities to meet business needs.
- Previous customer support experience
- Results-oriented and focused on quality of work
- Excellent structured problem-solving skills
- Ability to work effectively and efficiently with diverse teams and clients
- Strong presentation and technical writing skills
Qualifications: BS in Systems Engineering with 6 years of Experience
10. Knowledge, Skills and Abilities for Customer Quality Engineer Cover Letter
- Experience preferred in a technical environment within the medical device, healthcare, or pharmaceutical industries.
- Excellent problem-solving and analytical skills.
- Strong organizational skills, with the ability to manage priorities.
- Professional verbal and written communication skills.
- Exceptional documentation skills.
- Must have strong interpersonal skills, with superb time management skills.
- Ability to interface with technical resources and cross-functional teams.
- Set a professional tone and establish a cooperative partnership.
- Successful in a challenging, fast-paced, results-oriented environment.
- Strong knowledge and ability in Microsoft Office Suite (Word, Excel, PowerPoint, Outlook).
Qualifications: BA in Business Administration with 3 years of Experience