WHAT DOES A CUSTOMER QUALITY ENGINEER DO?
Updated: Jan 15, 2025 - The Customer Quality Engineer ensures compliance with IATF 16949 and implements quality and environmental management systems to meet industry standards. This role involves identifying, analyzing, and addressing product and process nonconformities while guiding teams in effective investigation techniques. The engineer also represents customer requirements, provides technical solutions, and ensures adherence to safety standards across all operations.
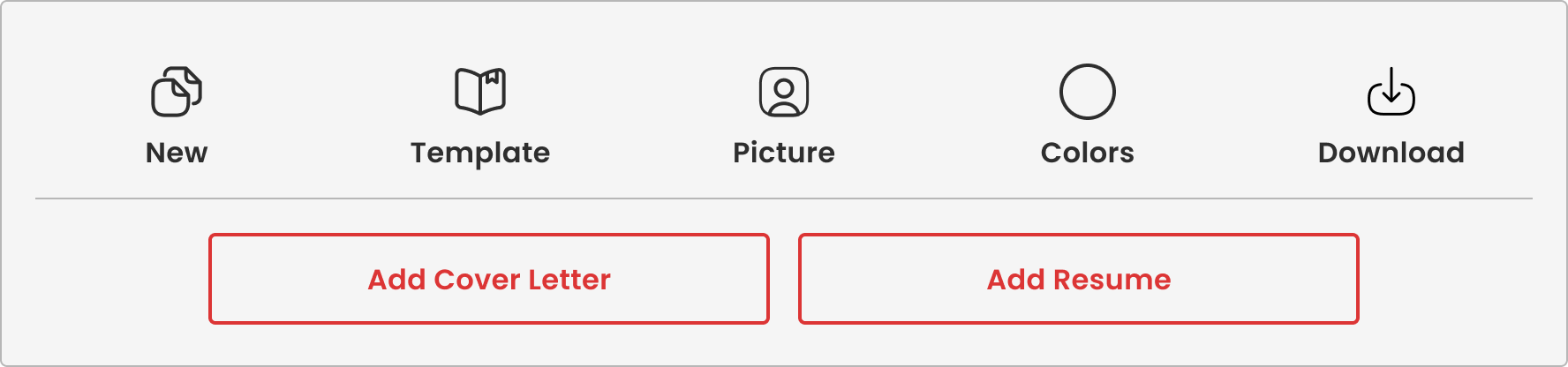
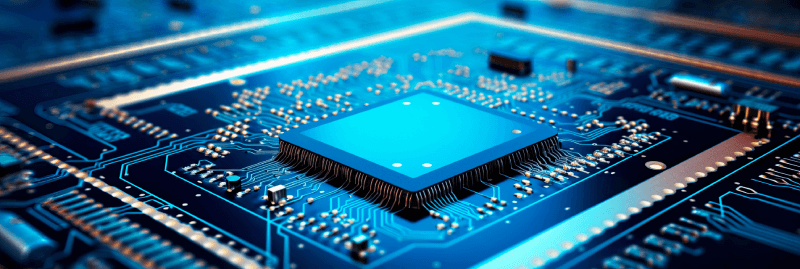
A Review of Professional Skills and Functions for Customer Quality Engineer
1. Customer Quality Engineer Functions
- Technical Expertise with In-House and Customer Records: Provide technical expertise necessary to interface in-house and customer records.
- Monitor Customer Portals: Oversee and monitor customer portals and communicate any updates/issues.
- Documentation Control Workflows: Workflows and tasks associated with Documentation Control.
- Expertise in Processing and Retention: Provide direction and expertise in the processing, release, reproduction, and retention.
- Communicate Customer Updates: Ensure customer requirements and new updates are communicated through customer portals in coordination with the Corporate Quality team.
- Policy Knowledge: Maintain knowledge of current department and corporate policies and procedures essential.
- Query and Issue Resolution: Prompt resolution of queries, issues, and information requested by customers.
- Document Release and Control: Release and control documents using manual and automated methods.
- Daily Assistance to Quality Team: Provide daily assistance to the rest of the NMI and Corporate Quality team.
- Weekly Reporting and Project Updates: Provide necessary weekly reports and project-related updates as requested by the Management, or project team.
- Risk Identification Mindset: Proactive and robust risk identification mindset to ensure that the potential risks are identified during the development phase.
2. Customer Quality Engineer Accountabilities
- High-Level Customer Quality Concerns Management: Manage high-level customer quality concerns with large corporations and companies globally.
- Technical Information and Corrective Actions Communication: Review and communicate technical information and corrective actions.
- Improvement Plan Implementation: Proactively implement improvement plans with the customer, engineering, and manufacturing sites within TE.
- Customer Meeting Participation: Participate in Customer Scorecard Reviews and customer focus team meetings.
- Customer Audits and Visits Facilitation: Prepare, organize, and facilitate customer audits/visits for A and strategic accounts, and follow up on potential corrective actions.
- Warranty and Liability Claims Management: Manage high impact warranty and liability claims for a manufactured product.
- Quality KPIs Review: Review relevant quality and TEOA KPIs to track performance and take appropriate action.
- VOC/VOB Follow-up: Obtain regular VOC/VOB and functional follow-up.
- Production Process Blocking/Unblocking: Block/unblock production processes (stock and deliveries).
- Customer Claims Reporting and Advising: Report and advise on customer claims to key stakeholders, including Legal Counsel and Finance.
- Project Management: Work on planned and ad-hoc projects.
- Company Values Upholding: Maintain a high level of integrity and uphold TE values of integrity, teamwork, accountability, and innovation.
3. Customer Quality Engineer Job Summary
- Quality Improvement Methodology Application: Applies quality improvement methodologies and principles to problems and projects across field service products.
- Cross-Functional Team Collaboration: Works closely with Customer Engineers (CEs) and cross-functional teams.
- Root Cause and Corrective Action Identification: Identify the root cause and establish corrective actions for installation, maintenance, and workmanship-related issues.
- Non-Conformance Analysis: Assess field issues through detailed NC (non-conformance) analysis, identify data trends, and drive quantified root cause identification.
- Issue Resolution Coordination: Coordinates issue resolution using quality (TrackWise, Tableau, Advanced Problem Solving (APS)) and statistical analysis tools.
- Zero-Defect Quality Culture Support: Support a Zero-Defect Quality culture in Service through improvements in operational processes, first-time-right performance, the proliferation of learnings, and reporting/data accuracy.
- Service and Operations Team Collaboration: Works with cross-functional teams (FSO, iTeam, AGS Central Operations, Product BU’s, Manufacturing, Quality).
- Current-State Assessment Conducting: Conduct current-state assessments of service business processes and identify improvement opportunities.
- Process Improvement Documentation Generation: Throughout the process improvement, generate supporting documentation such as current and future-state conditions, value stream maps, business process maps, and cost-benefit analysis.
- Process Improvement Proliferation Coordination: Coordinates the proliferation of problem solutions and operational process improvements across other organizations and products.
- Project/Program Management Skill Employment: Employs project/program management skills related to overall project tracking, deliverables management, action item tracking, meeting minutes, team communications, and presentations.
- Independent Work Execution: Works independently and receives minimal guidance and direction.
- Colleague Resource Support: Acts as a resource for colleagues with less experience.
4. Customer Quality Engineer Details
- Rejected Material Problem Evaluation: Record and evaluate any problems related to rejected material.
- Material Usage Verification: Ensure that the material received is not used until reviewed and/or quality reports are verified.
- Component Inspection and Documentation: Inspect and evaluate the components and document procedures.
- Inspection Record Maintenance: Establish and maintain records of inspection and evaluation of each received material.
- Supplier Communication Management: Maintain constant communication with suppliers to ensure that client requirements are met.
- Corrective Action Process Coordination: Manage and coordinate the process of formal corrective action provider.
- Corrective Action Review and Approval: Review and approve corrective action responses from the supplier.
- Supplier Quality Information Analysis: Collect, analyze, and summarize information on supplier quality and prepare periodic reports concerning quality problems.
- Supplier Corrective Action Response: Answer supplier corrective actions and disposition of rejected items.
- Supplier Certification Program Implementation: Implement and coordinate a supplier certification program.
- Test Equipment Verification: Ensure the veracity and accuracy of test measurement equipment used to verify product quality.
- Pressure Gauge Repair and Calibration: Undertake repair of pressure gauges used in the inspection that require calibration.
5. Customer Quality Engineer Details and Accountabilities
- Quality System Maintenance (IATF 16949): Ensure and maintain a quality system according to IATF 16949.
- Statistical Study Application: Ensure that appropriate statistical studies are being applied to analyze the variation in each measurement and testing equipment.
- Product Quality Guidance: Provide direction and technical guidance to personnel related to product quality.
- Quality and Environmental System Implementation: Implement quality systems and environmental management within the company.
- Nonconformity Prevention: Initiate actions to prevent the occurrence of any nonconformity relating to the product, process, quality system, and environmental management system.
- Issue Identification and Recording: Identify and record any issues with the product, process, quality system, and environmental management system.
- Solution Recommendation: Initiate, recommend, or provide solutions through established communication channels.
- Customer Representation in Quality Duties: Represent customer needs in domestic duties according to the requirements of the Quality System.
- Quality Representative Mentorship: Mentor quality representatives on effective investigation techniques and technical writing.
- Industry Group Participation: Actively participate in appropriate technical industry groups in industries that use products.
- Safety Standards and Decontamination Policy Adherence: Adhere to and maintain knowledge of all safety standards and return-product decontamination policies.