WHAT DOES AN ENVIRONMENTAL HEALTH AND SAFETY ENGINEER DO?
Updated: Mai 31, 2025 - The Environmental Health and Safety Engineer is responsible for leading EHS-related approvals and assessments for new facilities and projects, ensuring compliance with local government requirements. This position sets up and standardizes EHS management systems, implements SOPs, and organizes routine inspections, incident investigations, and corrective actions. This role develops and conducts EHS training programs, supervises external contractors, and leads EHS culture activities to enhance safety awareness across the site.
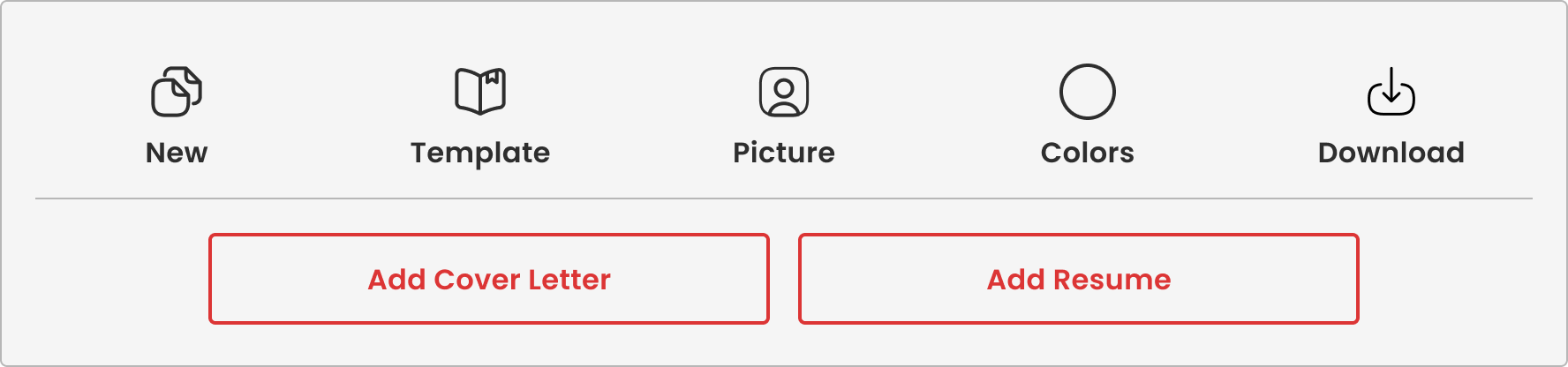
A Review of Professional Skills and Functions for Environmental Health and Safety (EHS) Engineer
1. Environmental Health and Safety Engineer Duties
- Injury/Accident Management: Review, investigate, and implement action plans for work-related injuries, illnesses, accidents, and safety concerns.
- Standard Development: Participate in new standard developments with Engineering, Manufacturing, and other key stakeholders.
- Customer Communication: Communicate with HQ about customer requirements.
- Guideline Provision: Provide proper guidelines about common specifications and safety to Korea engineers and HQ.
- Audit Support: Conduct & support Samsung common specifications audits in Samsung sites.
- Communication: Excellent communication skills to report and explain safety incidents to HQ.
- Tracking: Track customer requests about safety and common specifications with the Korea team.
- Customer Request Management: Drive customer requests with HQ engineering BU.
- Customer Interface: Interface with customers to deal with special requests regarding all product models.
- Meeting Participation: Attend regular meetings with customers to learn revised common specifications and safety regulations.
- Vendor Management: Manage local vendors about customer satisfaction work.
2. EHS Engineer Details
- Internal Audits: Conduct internal audits in line with ISO 14001 / 45001 / OHSAS 18001.
- Incident Tracking: Ensure incident investigations are tracked to closure.
- Compliance Assessment: Conduct procedural compliance assessments in the factory.
- Permit Development: Develop the permit-to-work system in association with technical personnel in the plant.
- Risk Assessment Coordination: Coordinate and lead task, area, and equipment-related health and safety risk assessments as part of the ongoing risk assessment program for the site.
- Ergonomics: Conduct manual handling and ergonomic assessments.
- Compliance Audits: Conduct assessments of compliance on batch records and other manufacturing-related documents.
- Emergency Response: Assist in the maintenance of the site's Emergency Response Team and Emergency Response Plan as an Upper Tier Seveso Site.
- Contractor Management: Assist in ensuring a strong adherence to contractor management activities.
- Action Tracking: Assist in ensuring action tracking and management across all functions of the organization.
- EHS Training: Ensure a process of continuous improvement in the EHS Training requirements of the site, including the development and delivery of training modules, safety briefings, tool box talks, etc.
- Documentation and Compliance: Assist with other EHS-related tasks such as updating documentation in a GMP environment, assist with Regulatory Agency Inspections, and communications, etc.
3. Environmental Health and Safety (EHS) Engineer Responsibilities
- EHS Approval: Be responsible for leading EHS-related approval/assessment for new facilities and projects, such as EIA, occupational health and safety assessments.
- Permit Management: Prepare for the application and collect the EHS permitting/license from the local government for operations.
- EHS System Setup: Set up and standardize EHS management systems, develop and implement EHS SOPs, and follow up on the implementation of EHS policies, rules, and standards.
- EHS Committee: Establish the EHS committee and hold regular meetings to review EHS KPIs with the management team.
- Safety Collaboration: Co-work with the operation team to set up safety protection and discipline to avoid working injuries.
- EHS Inspections: Organize routine EHS inspections, lead incident investigations, identify root causes, and follow up on corrective and preventive actions.
- Waste Management: Implement hazardous waste disposal and audit compliance of wastewater and gas treatment.
- Occupational Health: Be responsible for overall occupational health management to ensure compliance.
- Training: Develop/Conduct EHS training for staff, including new hire orientation and regular training on different topics for employees.
- Contractor Supervision: Supervise external contractors' work, ensuring it meets the proper engineering standards and EHS requirements.
- Regulatory Communication: Keep good communication with local authorities to comply with government requirements.
- EHS Culture: Lead EHS culture activities, enhancing EHS awareness for the whole site.
4. Environmental Health and Safety Engineer Job Summary
- EHS Training: Responsible for providing EHS training (level 2) to employees, contractors, and customers.
- Training Needs Assessment: Determine training needs and assist in the delivery of training programs to improve skills and techniques for lab & pilot plant personnel, including contractors.
- Safety Meeting Coordination: Organize and ensure monthly & quarterly safety meetings with segment & site EHS are conducted.
- Permit Management: Responsible for ensuring all work permits are issued and followed properly.
- Safety Job Analysis: Support segments to initiate safety job analysis (JSA) for non-routine work.
- Safety Reviews: Support the manager in leading and driving safety reviews of start-ups and new processes.
- Incident Reporting: Support segments to ensure PD labs & pilot plant safety/environmental incidents are properly recorded, reported, and closed accordingly.
- Waste Management: Serve as the responsible person for waste management in PD and liaise with site EHS regarding scheduled waste management.
- Safety Review: Support segments and ensure that all segments conduct safety reviews (SHE/MOC/PSSR) and HIRARC if any new activity, equipment, or process is introduced in PD labs & pilot plant.
- EHS Representation: Represent the PD operation team, and liaise with the site safety department & campus management team for all EHS issues, including safety committee meetings and monthly safety walkabout inspection programs.
- EHS Platform Management: Serve as EHS facilitator and editor on the PD EHS information platform.
- Safety Compliance: Ensure all environmental, health, and safety rules and guidelines are being adhered to and maintain high safety standards and a safe working environment.
5. Environmental Health and Safety Engineer Accountabilities
- Environmental Management: Maintain the Company's environmental plan, environmental programs, and all environmental permits in a manner consistent with Federal, State, and Company guidelines.
- Permit Management: Responsible for submitting all permits and maintaining all environmental files in a manner consistent with Federal, State, and Company guidelines.
- Environmental Compliance: Implement and administer all government-required environmental processes.
- EHS Partnership: Partner with department managers, team leaders, and hourly team members to achieve Environmental, Health, and Safety goals.
- Technology Knowledge: Maintain working knowledge of new technologies developed by the industry and government regulators.
- Process Improvement: Ability to develop engineered solutions to improve conditions or processes that result in a safer workplace.
- Safety Leadership: Possess the managerial courage to address safety issues within the team.
- Waste Monitoring: Monitor and record hazardous waste generation at the facility.
- Waste Management: Maintain hazardous waste manifests.
- Cost Tracking: Track waste disposal costs at the facility on a monthly basis.
- Regulatory Reporting: Submit annual reports to State regulatory agencies.
- Safety Processes: Safety processes such as Lock Out/Tag Out, Personal Protective Equipment, Fire Safety, Confined Space, Fall Protection, and Ergonomics, etc.
- Industrial Hygiene: Serve as the site’s Industrial Hygiene Coordinator, implementing and maintaining Industrial Hygiene Programs (e.g., Hazardous Communication, Hearing Conservation, etc.).
- EHS Training: Deliver EH&S training to new team members.
6. Environmental Health and Safety Engineer Functions
- Leadership: Lead the startup of a newly acquired manufacturing center of excellence.
- EHS Compliance: Implement EHS programs for three business groups occupying the Plymouth, MN facility to ensure compliance with regulatory bodies and a safe work environment for employees in both medical device manufacturing and office-based settings.
- Policy Alignment: Direct EHS programs for the Plymouth, MN site to ensure compliance and alignment with Philips corporate Health, Safety, and Sustainability policies and requirements.
- Regulatory Compliance: Maintain compliance with EPA, MN Pollution Control Agency, and MNOSHA.
- Safety Programs: Develop and manage site safety and health programs to ensure a safe and healthful working environment for employees.
- Safety Certifications: Drive site programs to achieve ISO 14001 and ISO 45001 management system certifications for the site.
- Environmental Programs: Develop and manage environmental programs, including Solid and Hazardous Waste Management, Recycling, Energy and Water Reduction Programs, New Chemical Approval, Tier 2 Reporting, DOT Hazardous Materials/Dangerous Goods, and other general environmental management system and control programs.
- Emergency Response: Develop and maintain an effective emergency response program commensurate with the risk-related emergencies relevant to the site and operations.
- Auditing and Inspections: Conduct internal audits, inspections, risk assessments, and accident investigations.
- Risk Management: Responsible for Risk Analysis of existing and new processes, implementation of mitigation actions (incl. Ergonomics, work clothing & PPE), and incident/accident investigations.
- HSE Audits: Participate in internal cross-audits and 3rd Party HSE Audits, ensuring non-conformities are corrected.
- Occupational Health: Manage all aspects of Occupational Health in cooperation with the HR Function.
- Facilities Safety: Work with the Facilities Team to ensure buildings and equipment are maintained in safe condition.
- Hazardous Material Management: Ensure appropriate usage, storage, and disposal of all hazardous material, waste, and HSE-relevant documents and records.
7. Environmental Health and Safety Engineer Job Description
- Safety Enforcement: Maintain and enforce all safety and health policies, including creating new procedures and enforcing existing policies required by state and federal governments.
- Operations Oversight: Oversee daily operations to ensure all manufacturing employees follow safety procedures precisely.
- Policy Documentation: Create documents that outline all safety policies in a manner easily understood by manufacturing workers and the management team.
- Administrative Reporting: Complete administrative duties, including filling out safety reports, collaborating with management, and compiling information about accidents to prevent similar incidents in the future.
- Employee Training: Train and oversee employees on health and safety regulations.
- Hazard Monitoring: Monitor personnel and workspace to identify and address potential safety risks.
- Risk Mitigation: Evaluate probable physical and chemical hazards and take essential steps to minimize them.
- Program Evaluation: Measure and audit the effectiveness of hazard control programs.
- Equipment Management: Maintain and manage equipment and processes related to each health and safety project.
- Issue Resolution: Recommend solutions to issues that need improvement.
- OSHA Compliance: Report injury and illness data online to comply with OSHA requirements.
- Workers' Compensation Coordination: Coordinate with HR to submit workers' compensation claims.
8. Environmental Health and Safety Engineer Overview
- Compliance Auditing: Work with outside consultants performing periodic compliance audits and participate in reporting and compliance review processes with regulatory agencies.
- EH&S Project Support: Provide support to EH&S projects considered critical or sensitive in nature, including projects impacting facilities, liabilities, and capital expenditures.
- Process Review: Review the implementation of EH&S methods, practices, and procedures.
- Team Leadership: Act as a lead or technical expert to direct, coordinate, and review the work of a small group of staff involved in EH&S activities.
- Technical Guidance: Provide technical guidance to technical staff and other departments for all EH&S matters.
- Certification Maintenance: Attend regular training in environmental, health, and safety areas and maintain/obtain certifications applicable to EH&S programs.
- EH&S Trends Monitoring: Stay updated on new EH&S methods and developments, including environmental safety engineering and industrial hygiene, to recommend changes.
- Safety Coordination: Coordinate safety program activities to achieve safety goals.
- Performance Tracking: Establish and maintain comprehensive industrial safety/health records to demonstrate safety performance improvements.
- Training Development: Develop, conduct, coordinate, and implement training programs for all associates.
- Regulatory Compliance: Ensure continual compliance with all applicable federal, state, and local regulations, and periodically review new or amended rules for applicability to the organization.
- Hazard Evaluation: Evaluate all site materials, technologies, equipment, processes, and procedures to identify potential EH&S hazards, communicate them, and implement hazard control measures.
9. Environmental Health and Safety (EHS) Engineer Details and Accountabilities
- EHS Leadership: Interfacing with a team of engineers, management, and operations employees, the Environmental, Health and Safety Engineer provides guidance, leadership, and technical support for environmental, health, and safety programs and initiatives.
- Environmental Review: Review projects, plans, specifications, and purchases to verify that environmental issues are considered and addressed in a proactive manner.
- Project Support: Support projects and collaborate with company and consultant resources to leverage best work practices and to provide additional skill-level support.
- Regulatory Reporting: Responsible for submitting state and federal compliance reports for air, waste, water, and other programs.
- Root Cause Analysis: Lead or facilitate root cause analysis when non-compliance events, environmental near misses, or safety incidents occur.
- Compliance Monitoring: Stay abreast of new environmental obligations (i.e. government regulations, industry standards, or corporate guidance) or a change in the workplace and ensure continued facility compliance.
- Data Analysis: Compile, analyze, and interpret environmental statistical data.
- Risk Assessment: Understand the impact of manufacturing processes and equipment in regard to environmental impacts, health and safety risks, and compliance.
- Regulatory Liaison: Interact with federal, state, and local regulators to facilitate plant operations, resolve compliance issues, and participate, as a team member, in regulatory and corporate inspections and investigations.
- Audit Management: Lead the facility effort to respond to corporate and external audits, including developing appropriate corrective actions and tracking the closure of those actions.
10. Environmental Health and Safety Engineer Tasks
- Task Prioritization: Prioritization of job duties and assignments depending upon evolving location and enterprise needs.
- Independent Decision-Making: Work is often performed without appreciable direction and with considerable latitude in determining the technical objectives of assignments.
- Technical Problem Solving: Exercises judgment in selecting methods, techniques, and evaluation criteria for obtaining results, and develops consensus-built ideas and technical solutions to address EH&S needs and regulatory or compliance challenges.
- Risk Mitigation: Postulates, derives, or develops solutions that enable effective risk mitigation, promotion of a safe and healthful work environment, and avoidance of potential negative risks or impacts to the company, its employees, or operating environments.
- Regulatory Analysis: Analyzes current, pending, or developing laws and regulations to identify potential impacts or concerns and effectively summarizes and communicates findings.
- Strategic Initiatives: Develop and implement strategic initiatives that drive continuous programmatic improvement.
- Stakeholder Interaction: Interacts with all organizational levels, including program and senior management, technical personnel, internal and external customers, and regulatory agency personnel, to define and socialize consensus-supported solutions for strategic objectives or compliance challenges.