WHAT DOES AN ENVIRONMENTAL HEALTH AND SAFETY COORDINATOR DO?
Updated: Mai 30, 2025 - The Environmental Health and Safety (EHS) Coordinator executes environmental compliance audits for manufacturing environments and fieldwork, ensuring adherence to safety and environmental standards. This position develops and delivers training programs on environmental concerns, maintains training records and relevant documentation, and coordinates emergency response plans. Additionally, this role monitors hazards, manages waste streams, maintains environmental permits, and collaborates with Logistics and Supply Chains to select suppliers for waste collection.
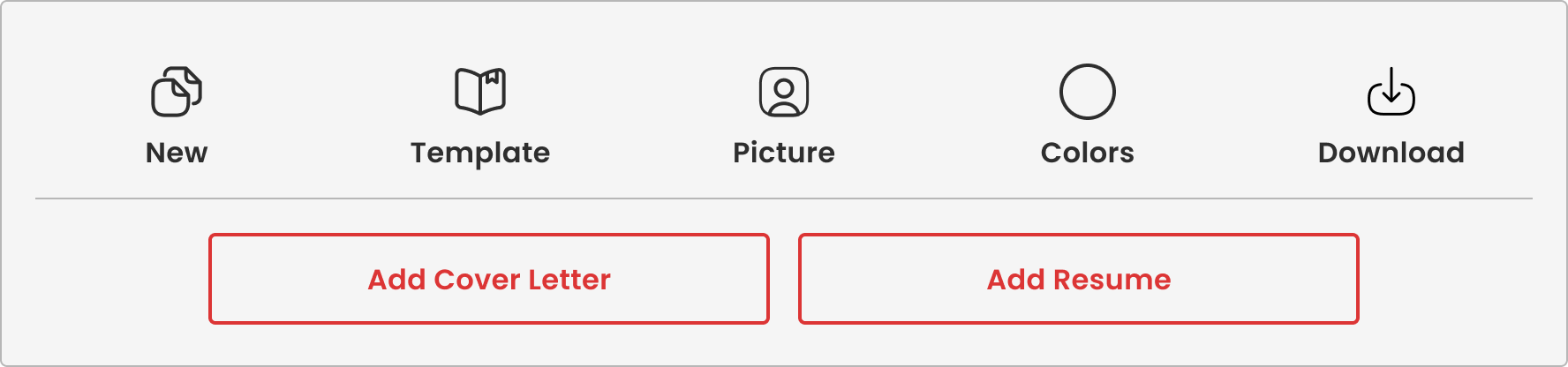

A Review of Professional Skills and Functions for Environmental Health and Safety Coordinator
1. Environmental Health and Safety Coordinator Duties
- Regulatory Compliance: Ensure the company is in compliance with OSHA 29CFR.1910 regulations and EPA 40 CFR.
- Record Management: Maintain all records for EPA, OSHA, and DOT both Federal and State.
- Procedure Maintenance: Maintain all ISO 14001, ISO 45001, OSHA, and EPA required procedures ensuring they are up to date.
- EHS Training Management: Create, conduct, coordinate, and manage all EHS training (including EHS training record database).
- Data Collection and Reporting: Collect and report all safety and environmental required information and readings.
- Incident Reporting: Maintain the OSHA log 300 and worker's compensation records for injury reporting.
- Risk Assessment: Manage Risk Assessment and Job Safety Analysis database per work center.
- Safety Documentation: Update and maintain all Safety Data Sheets for state and OSHA requirements.
- Near Miss Tracking: Maintain near miss log and corrective actions.
- Collaboration and Networking: Create links and contacts with other sites in the Europe region to research the best available practices and share ideas.
- Project Participation: Participate in regional networks and contribute to regional or subregional projects.
2. EHS Coordinator Details
- HSE Advisory: Advise and support the site management on all HSE issues.
- Team Collaboration: Partnership with temporary HSE team members working on-site projects.
- Regulatory Compliance: Follow Bayer's fundamental HSE requirements and local legal requirements.
- Procedure Implementation: Implement procedures, guidelines, training, and support to ensure compliance.
- Stakeholder Engagement: Daily interaction with site supervisors, shop floor supervisors, and operators to gain support and understanding of programs.
- Program Coordination: Organize and coordinate onsite activities, meetings, and training for occupational health and safety.
- Action Deployment: Deploy the actions defined by the annual master plan throughout the site.
- Hazard Recognition: Coordinate and improve hazard recognition, observations, and incident support processes.
- Audit Execution: Perform internal audits, document results, and follow up on action plans.
- Safety Reporting: Stimulate safety observations, near-miss, and first-aid notifications.
- Performance Reporting: Report periodically on progress to site management using performance and management review processes.
3. Environmental Health and Safety Coordinator Responsibilities
- Environmental Auditing: Executes environmental compliance audits for manufacturing/shop environments and fieldwork.
- Training Development: Develops and delivers training programs on environmental concerns or health and safety risks.
- Record Maintenance: Ensures appropriate maintenance of training records, environmental manuals, incident/accident reports, and documentation.
- PPE Management: Purchases and distributes personal protective equipment and related supplies.
- Hazard Monitoring: Monitors health, safety, and environmental hazards, such as noise, air, or wastewater pollution levels.
- Inspection Coordination: Coordinates inspection of facilities, vehicles, and equipment.
- Emergency Planning: Develops and communicates facility-specific emergency response or evacuation plans.
- Permitting Compliance: Maintains applicable permitting and licensing for environmental requirements in various states.
- Regulatory Research: Researches federal, state, and local environmental requirements for compliance updates.
- Waste Management: Develops and implements Waste Management Plans, including risk assessments, SOPs, emergency response plans, and training.
- Supplier Coordination: Works with Logistics and Supply Chain to assess waste-streams and select appropriate suppliers for collections.
4. Environmental Health and Safety (EHS) Coordinator Job Summary
- KPI Management: Management of SGA and reporting of KPIs.
- ISO Compliance: Accomplish all requirements established in ISO 14001.
- Personnel Training: Training of new and current personnel.
- Action Monitoring: Follow up on corrective and preventive actions.
- EHS Advisory: Provide advice and suggestions on EHS matters ensuring compliance.
- Incident Management: Ensure all incidents and accidents are recorded, investigated, and filed.
- Documentation Management: Create, develop, and maintain EHS documentation.
- Risk Assessment: Participate in risk assessment generation and review.
- Inspection and Auditing: Undertake EHS inspections and participate in audits and regulatory visits.
- Waste Management: Ensure all waste is disposed of correctly and paperwork is completed in accordance with legislation.
- Environmental Reporting: Submit Environment Agency returns and update corporate environment reporting tools.
- Sustainability Initiatives: Participate in sustainable development initiatives.
- EHS Training Delivery: Deliver training on EHS topics
5. Environmental Health and Safety Coordinator Accountabilities
- EHS Culture Promotion: Promoting a collaborative EHS culture and facilitating team cooperation and engagement.
- Mentoring and Coaching: Mentoring, coaching, and teaching Novelis Kingston team members within the scope of expertise.
- ISO Compliance Support: Supporting the development and maintenance of ISO compliance systems and EHS SOPs/work instructions.
- Accident Investigation: Supporting accident investigation and driving towards root-cause solutions.
- Risk Management: Recognizing, evaluating, and controlling industrial risks through active facilitation of Safety Programs and Policies.
- Compliance Decision-Making: Making decisions impacting compliance and the prevention of injuries and illnesses.
- Security Liaison: Guiding facility security services and acting as a liaison with the facility.
- Continuous Improvement: Participating in continuous improvement exercises to build sustainable solutions.
- Regulatory Compliance: Ensuring EHS regulatory compliance and managing annual reporting requirements.
- Waste Treatment Management: Facilitating waste treatment processes, including auditing, record keeping, and waste reduction.
- WHMIS Resource: Acting as a resource for WHMIS, managing SDS databases, and conducting periodic audits and training.
6. Environmental Health and Safety Coordinator Functions
- Compliance Management: Ensure that the organization complies with applicable federal, state, and local laws, codes, and regulations pertaining to the environment, health, and safety, including the development and implementation of written programs required by established and future standards.
- Program Administration: Establish a formal program to administer the facility hazard evaluation activities and process safety program.
- Hazard Control Coordination: Work with consultants to coordinate combustible dust hazard testing and implement cost-effective control of hazards.
- Employee Training Development: Develop appropriate employee training in fire and explosion hazards, equipment, and administrative controls.
- Policy Consultation: Provide guidance, consultation, and assistance to management and others on developing, distributing, and enforcing policies and procedures regarding the environment, health, and safety.
- Training Program Management: Determine occupational safety and health training requirements for the organization and develop, organize, and present appropriate training to employees.
- SPCC Plan Maintenance: Maintain a Spill Prevention Control and Countermeasure (SPCC) plan.
- SOP Compliance Coordination: Work with Operations and Maintenance to install and maintain necessary control measures and ensure SOPs are SPCC compliant.
- Equipment Testing Coordination: Conduct or coordinate biannual calibration and testing of all oxygen deficiency monitors.
- Incident Investigation: Respond to complaints, conduct investigations, and recommend solutions to minimize safety and health problems to management.
- Safety Documentation Management: Maintain the safety training manual, including the emergency response plan.
- Chemical Safety Planning: Coordinate with the Quality Control Laboratory Manager to develop and maintain a chemical hygiene plan and ensure compliance with best practices for laboratory safety.
- Insurance Compliance: Work with insurance representatives to complete best practices or recommendations.
7. EHS Coordinator Job Description
- Safety Committee Management: Facilitate, organize, and participate in the company safety committee.
- Incident Investigation and OSHA Compliance: Coordinate with HR to maintain OSHA records, perform incident investigations, and provide follow-up with employees after an accident.
- EHS Audit Program Development: Develop an internal EHS audit program and work with consultants to complete annual external audits.
- Hazardous Waste Management: Administer the hazardous waste management program with the help of outside vendors, ensuring compliance with RCRA (Resource Conservation and Recovery Act) and the State of Arizona regulations.
- Regulatory Compliance: Interpret and apply regulations to ensure compliance with RCRA and other environmental standards.
- Waste Minimization Program: Establish and maintain an effective waste minimization program according to RCRA requirements.
- Universal Waste Management: Administer the universal waste management program for the disposal of contaminated products, pesticides, and other materials in compliance with state and federal regulations.
- Respiratory Protection Coordination: Coordinate the respiratory protection program for the organization.
- Hazard Communication Program: Coordinate the Hazard Communication program, including maintaining the inventory of hazardous chemicals within the organization and ensuring departments maintain SDSs (Safety Data Sheets) for areas such as laboratories, production, and maintenance.
- Emergency Response Coordination: Serve as the emergency contact for Precision Science and coordinate emergency response efforts, including the emergency notification system and implementation of emergency management policies and procedures.
- Emergency Drill Organization: Organize and conduct annual evacuation drills and other emergency exercises.
- Industrial Hygiene Testing: Coordinate biennial industrial hygiene testing.
8. Environmental Health and Safety Coordinator Overview
- Workplace Safety Promotion: Promote and provide a safe workplace, seek improvements, and support the Health & Safety Program.
- Union Relations Support: Support compliance with collective agreements and foster sound union/management/employee relations.
- Stakeholder Rapport Development: Develop and maintain a good rapport between labor, customers, outside agencies, other users, and management.
- Innovation and Awareness: Identify innovative ideas and implement activities to seek improvements, promote awareness, and ensure a safe workplace.
- Health and Safety Program Development: Develop and support Health and Safety programs, ensuring effective implementation, training, and maintenance for all employees through accountable Supervisors and Superintendents.
- Safety Inspections and Investigations: Conduct and participate in safety/environmental inspections and incident investigations within the FRM operations.
- WSIB and RTW Program Management: Manage the administration and maintenance of WSIB (Workers' Safety and Insurance Board) and RTW (Return to Work) programs.
- Committee Participation: Participate in various committees, including the JHSC (Joint Health and Safety Committee), to ensure consistent application of health, safety, and environmental practices.
- Employee Training and Communication: Communicate and train all Sawmill employees on Health, Safety, and Environmental regulations, as well as internal policies and procedures.
- Policy Compliance Enforcement: Ensure employees, contractors, consultants, and visitors comply with Company policies, procedures, guidelines, and all health, safety, and environmental Acts, Rules, and Regulations.
- Environmental Management Standards: Develop and maintain the Environmental Management System (ISO 14001) and OHSAS (ISO 18001) standards for NOW operations.
- Regulation Updates and Innovation: Identify and stay updated with new regulations and innovations to enhance the effectiveness and efficiency of Health, Safety, and Environmental Services.
- Safety Statistics and Reporting: Develop, manage, and maintain a system to provide safety statistics and reports to identify trends and implement preventative actions while minimizing costs.
- Safety Activity Audits: Audit all safety activities for Sawmill operations.
- Program Implementation and Improvement: Implement, maintain, monitor, and improve health and safety programs to support, counsel, and empower management personnel and employees.
9. Environmental Health and Safety Coordinator Details and Accountabilities
- Compliance Management: Ensure the management system complies with current versions of ISO 14001, OHSAS 18001, and ISO 50001.
- Regulatory Compliance: Ensure compliance with applicable federal and/or state laws, regulations, agency rules, corporate standards, and guidelines.
- Permit Management: Secure, revise, and maintain applicable environmental and hazardous materials permits.
- Team Supervision: Establish priorities, make assignments, and provide necessary supervision to monitor job execution and ensure compliance with established standards.
- Safety Training: Provide training on OSHA standards and safety regulations.
- Training Records: Maintain records documenting the date and nature of OSHA training.
- Report Review: Review and respond to OSHA reports.
- Emergency Planning: Develop appropriate emergency plans.
- Emergency Response: Respond to emergencies during off-hours.
- Accident Management: Perform accident management activities, including injury and incident management, investigations, and associated record keeping.
- Investigation Oversight: Ensure accident/incident investigations are conducted.
- Corrective Actions: Identify, implement, and track corrective actions to prevent recurrence.
- Injury Records: Maintain injury records in accordance with government regulations and corporate practices.
- Claims Oversight: Oversee worker’s compensation claim management.
- Hazard Assessment: Perform hazard assessments and other evaluations.
- Risk Analysis: Survey, compile, and analyze data relating to risks.
10. Environmental Health and Safety Coordinator Tasks
- Risk Assessment and Hazard Control: Assess risk and make recommendations to control hazards.
- Safety Evaluations: Perform job safety assessments and other EHS evaluations.
- EHS Awareness Promotion: Promote awareness of the EHS policy and objectives at all levels of the organization.
- Plan Development and Review: Oversee the development, evaluation, or review of plans and criteria for a variety of activities.
- Feasibility Assessment: Assess the feasibility of proposed plans, projects, and equipment.
- EHS Effectiveness Monitoring: Monitor and evaluate operations, programs, processes, and practices for EHS effectiveness.
- Committee Participation: Participate in EHS Committee and Ergonomic Committee activities.
- Legislation and System Updates: Maintain documented knowledge of existing legislation and management systems, keep updated on developments in laws and regulations, and inform the Quality & EHS Country Coordinator of relevant matters.
- EHS Contract Management: Select, develop, and evaluate applicable EHS contracts to ensure efficient operations.
- Regulatory Compliance Oversight: Ensure compliance with federal and/or state laws, regulations, agency rules, corporate standards, and guidelines.
- Quality and Effectiveness Monitoring: Monitor and evaluate operations, programs, processes, and practices for quality and effectiveness, making recommendations for improvement.
- Incident Investigation and Corrective Action: Ensure accident and incident investigations are conducted to determine causes and implement appropriate corrective actions.
- Injured Worker Rehabilitation: Ensure injured workers are rehabilitated and achieve an early return to the workplace.
- Health and Safety Compliance: Ensure compliance with all relevant health and safety legislative requirements.
- Regulatory Agency Relationship Management: Maintain positive working relationships with Regulatory Agency Personnel (EPA, OSHA, DOT, federal, state, and local agencies) and various outside auditors.
11. Environmental Health and Safety Coordinator Roles
- Safety Meeting Leadership: In partnership with plant management, plan, lead, and participate in plant safety meetings.
- Safety Training Facilitation: Assist in training, educating, and ensuring supervisors are capable of running safety meetings.
- Safety Metrics Review: Review and update monthly plant-specific safety metrics.
- Equipment Safety Oversight: Develop and ensure safe equipment operating techniques.
- Partner with the Maintenance Team to ensure all machines and equipment are in good condition.
- Safety Onboarding Coordination: Lead safety onboarding meetings with all employees and sub-contractors.
- Documentation Review: Review all applicable documentation for completeness to ensure all employees and sub-contractors can adequately execute the scope of work safely.
- Disciplinary Procedure Enforcement: Follow up with supervisors and sub-contractor representatives to ensure proper disciplinary procedures are followed for safety issues.
- Safety Advisory Role: Serve as the principal source of information on safety issues to hold supervisors and sub-contractor representatives accountable to safety policies, procedures, and programs.
- SDS Management: Implement, inspect, and maintain job site and office SDS manuals.
- SDS Procedure Training: Train employees in SDS procedures.
- Hazard Communication: Provide and ensure compliance with information, signs, posters, barriers, and other materials to warn of potential and actual safety hazards and to prevent access to hazardous conditions.
- Injury Management and Return-to-Work Facilitation: Work with injured employees, supervisors, and HR to facilitate return to full-duty work responsibilities and provide meaningful light-duty transitional work opportunities.
12. Environmental Health and Safety Coordinator Additional Details
- EHS Program Administration: Ensure the implementation, administration, and maintenance of all facility-specific EHS programs.
- Corrective Action Management: Initiate, document, and monitor corrective actions for adherence to safety systems.
- Continuous Improvement Oversight: Manage all EHS continuous improvement initiatives relating to OSHA, EPA, and best management practices.
- EHS Metrics Reporting: Keep the facility management team informed of safety concerns and leading EHS metrics.
- ESG Initiative Leadership: Lead EHS-specific initiatives as they pertain to ESG.
- Safety Committee Facilitation: Participate in and facilitate the Safety Committee at the facility to ensure its effectiveness and alignment with the facility’s expectations.
- Hazard Inspection: Inspect the facility to detect existing or potential accident and health hazards.
- Corrective Measures Implementation: Determine corrective or preventative measures, assign responsibility, and follow up to ensure corrective actions are implemented.
- Plant Safety Inspection: Conduct periodic plant safety inspections to ensure safety procedures are in place.
- Accident Analysis and Resolution: Analyze accident causes and hazards, implementing solutions to resolve deficiencies.
- Disaster Plan Maintenance: Update and maintain the site-specific Disaster Plan.
- Emergency Preparedness Training: Periodically train employees in proper procedures and conduct emergency evacuation drills to ensure planning is effective in practice.
13. Environmental Health and Safety Coordinator Essential Functions
- PPE Requirement Assessment: Assist with the establishment of additional PPE requirements based on the job-specific requirements.
- Worker’s Compensation Management: Ensure compliance with Worker’s Compensation, including working with the Risk Management Team, third-party administrators, and legal counsel to effectively investigate and resolve claims in an expeditious and cost-effective manner.
- Fitness-for-Duty Coordination: Maintain a proactive fitness-for-duty process with local Occupational Medical clinics.
- Safety Training Implementation: Plan and implement programs to train supervisors and employees in plant safety practices, safe equipment operating techniques, and fire prevention for the plant and office area.
- First Aid and CPR Training: Facilitate employee training in first aid and CPR.
- Training Record Maintenance: Maintain training records in the employee files.
- New Employee Safety Orientation: Ensure new employees receive safety instructions prior to beginning work, emphasizing any specific plant hazards and thoroughly explaining all applicable precautions.
- Risk Management and Policy Implementation: Plan and implement risk management, safety policies, and procedures in compliance with all federal, state, county, and local rules and regulations, including SDS requirements, for both plant and office operations, to maximize a safe working environment.
- Safety Authority Escalation: Escalate any federal, state, or municipal safety or risk management authority and/or personnel, including, but not limited to, OSHA, to the Corporate Safety group.
- SDS Program Maintenance: Ensure the SDS program is maintained and all necessary personnel are trained on the procedures.
- Hazardous Materials Control: Manage hazardous materials control program, review samples, and test for hazardous materials prior to the start of operations.
- Incident Reporting Management: Ensure incident reports are prepared and sent in a timely manner.
14. Environmental Health and Safety Coordinator Role Purpose
- Regulatory Compliance: Ensure all employees and contractors comply with applicable provincial and other regulatory requirements.
- Safety Plan Implementation: Support the Project Management Team with the implementation of an effective Site-Specific Safety Plan.
- Plan Development: Support plan creation, including the development of job safety analysis (JSA), safe work practices, hazard/risk assessments, and incident investigation.
- EHS Role Compliance: Assist Senior Location Managers with compliance to role requirements as they relate to EHS.
- Joint Health and Safety Committee Support: Support Joint Health and Safety Committees in legislated roles and requirements.
- Incident Investigation: Conduct incident investigations for all injuries or near misses to identify root causes, trends, and prevention strategies, and report findings and lessons learned in Siemens’ tools to respective management.
- Injury Reporting: Report injuries to the applicable Workers' Compensation Board (WCB).
- Program Improvement: Continuously support improvement of Health, Safety, and Environment programs by updating hazard assessments, identifying aspects/impacts, and revising JSAs, safe work policies, and procedures in collaboration with the Field Operation team.
- EHS Software Maintenance: Support maintenance of EHS Insight Software, perform quality reviews of safety records, and communicate updates to the safety program.
- Safety Training Delivery: Support the safety training program and conduct internal Siemens-specific safety training virtually and/or in person.
- Supplier Pre-Qualification Support: Support the Supplier Pre-Qualification process.
- Certificate of Recognition Monitoring: Monitor and support the Certificate of Recognition (COR) process and mandatory customer/project requirements.
- EHS Initiative Monitoring: Monitor and support various aspects of new initiatives rolled out within the EHS program.
15. Environmental Health and Safety Coordinator General Responsibilities
- HR Process Management: Complete all necessary paperwork and processes for new hires, internal job changes, cost center changes, department changes, terminations, and pay changes.
- Data Accuracy and Entry: Ensure accuracy and timely completion of entries, including additional work to support joiners and terminations with BIS.
- Personnel File Management: Create, maintain, and manage all requests and work related to personnel files, ensuring timely and accurate filing.
- New Employee Orientation: Plan and conduct new employee orientation, including managing new hire paperwork.
- Job Description Updates: Manage updates to job descriptions and ensure signed copies are received by employees.
- Timekeeping Support: Understand and address timekeeping questions for hourly employees and managers.
- Benefits Support: Understand company benefits and escalate questions to the benefits center.
- HR Team Assistance: Support the HR team on required HR activities, projects, and develop centralized methods for communication, case management, and administrative processes.
- Policy Compliance: Ensure all working policies are in place, up-to-date, and reviewed regularly or as legislation dictates.
- Process Improvement: Manage projects to support the HR team and drive process improvements.
- Manager Coaching and Employee Support: Coach managers on HR processes and answer employee questions.
- Retention Support: Conduct exit and stay interviews, process exit paperwork, and reclaim company property.
- Security Management: Support security policies and procedures by facilitating the distribution and disabling of site badges.
- Vehicle and Parking Management: Manage site vehicle information and distribution of parking permits.
- Lobby Operations: Monitor and maintain the main plant lobby, including answering incoming calls, directing calls, and managing visitor records.