WHAT DOES AN ENVIRONMENTAL HEALTH AND SAFETY DO?
Published: Jun 16, 2025 - The Environmental Health and Safety (EHS) Professional ensures the protection of people, property, and the environment through strict adherence to regulatory standards and best practices. This role involves developing safety policies, conducting risk assessments, and delivering training programs to minimize workplace hazards. The individual supports sustainable operations by fostering a proactive safety culture and driving continuous improvement across the organization.
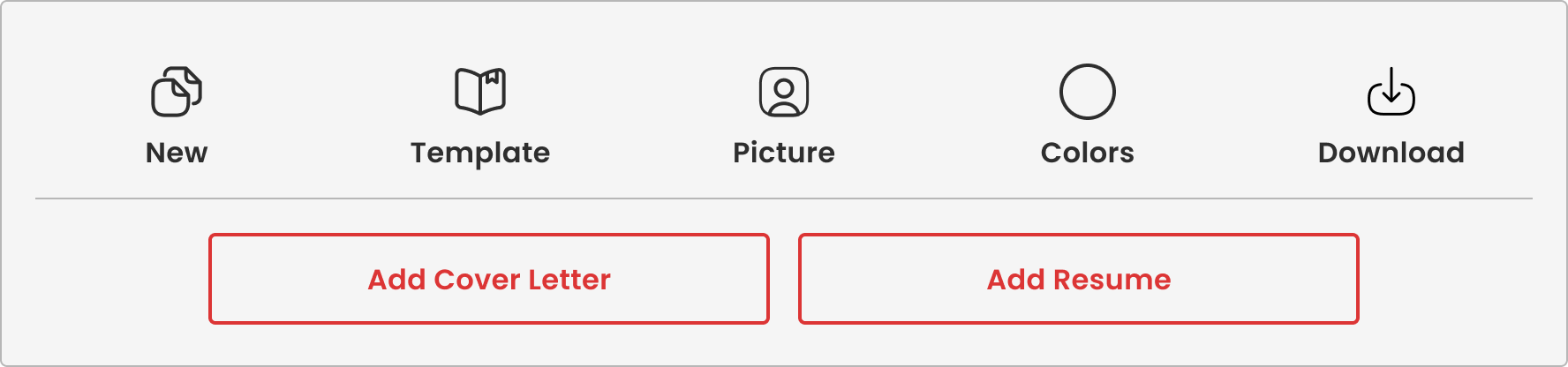

A Review of Professional Skills and Functions for Environmental Health and Safety
1. Environmental Health and Safety Coordinator Duties
- Regulation Review: Review local regulations regarding the type of operations of the company
- Task Prioritization: Prioritize tasks to implement safety policies in the venues
- Task Understanding: Understand tasks according to job positions, business, etc.
- Business Learning: Learn about the company and its business
- Progress Monitoring: Follow the progress, encourage and justify purchases
- Task Investigation: Investigate specific tasks and duties of all job positions
- Incident Prevention: Determine needs and the proper procedures to follow to prevent incidents
- Procedure Determination: Determine regulations and procedures to follow and implement in each project
- Information Communication: Communicate the related information about EHS requirements
- Requirement Review: Review continuously legal requirements
- Requirement Communication: Communicate the related requirements of EHS
- Report Preparation: Make a report with the information regarding
- Report Submission: Send the report to the managers
- Incident Recommendation: Make recommendations to prevent the same in the future
- Situation Monitoring: Monitor the situation continuously
2. Facility Environmental Health and Safety Engineer Details
- Committee Coordination: Conduct any Operating Safety Committee (OSC) meetings for new process/material implementation or changes
- Risk Assessment: Conducts hazards and risk assessments (HRAs), machine guarding, ergonomic and other assessments to make recommendations for corrective actions to control and/or mitigate risk
- Ergonomic Assessment: Conduct ergonomic assessments in high-risk areas
- Hazard Analysis: Conduct Process Hazard Analysis (PHAs) for all Process Safety Management-related processes
- Incident Investigation: Perform near-miss and accident Investigations and submit appropriate reports (s)
- Security Collaboration: Work closely with the Security team on all site security-related issues
- Technical Support: Provide technical expertise, assistance, training, and resources to customers, associates, legal, engineering, and management
- Standardization Alignment: Work in correlation with Auburn Hills Tech Center (ATC) Safety personnel to ensure standardized work and corrective actions
- Readiness Inspection: Conduct Operational Readiness Inspections (ORIs) for new equipment and/or process installations
- Communication Development: Develops customized HS&E communications for the facility (e.g., Newsletters, Safety Topic, Safety Alerts, etc.)
- System Coordination: Serves as Health and Safety Management System (HSMS) Coordinator
- Action Implementation: Implement corrective actions to facility risk management audit findings
3. Environmental Health and Safety Manager Responsibilities
- Safety Compliance: Ensure compliance with safety policies, regulations, and reporting in manufacturing
- Culture Promotion: Model and promote an organizational culture that fosters safe practices through effective leadership and training
- Control Verification: Work with the site leadership team to ensure all key safety operational controls are in place and safety action items and work orders are resolved on a timely basis
- Training Development: Develop and maintain safety and environmental training plans for the personal and professional development of managers and employees
- Procedure Maintenance: Maintain and update existing safety procedures, standard operating procedures and policies
- Audit Execution: Conduct internal safety audits promptly to ensure regulatory compliance
- Practice Improvement: Partner with manufacturing managers to review and improve safety practices and ensure adoption by employees
- Audit Support: Provide critical information and documentation to 3rd party auditors
- Hazard Improvement: Assist in the continuous improvement of hazard identification and risk assessment
- Regulation Management: Manage compliance for environmental regulations (e.g., air permits)
- Risk Assessment: Perform hazardous risk assessments for tasks or jobs to identify potential hazards and develop risk prevention plans to mitigate them
- Accident Analysis: Review and analyse accident/injury reports and data for accuracy and detail, ensuring corrective actions are taken
- Procedure Updating: Maintain and update existing safety procedures, standard operating procedures, and policies
- Objective Planning: Develop specific safety objectives and create action plans to meet those objectives
- System Management: Manage and maintain site-specific internal safety systems and reporting tools
- Root Cause Analysis: Ensure appropriate countermeasures are properly identified to prevent reoccurrence using a robust incident investigation process including 5-Why root cause analysis
- Testing Coordination: Ensure timely coordination of all regulatory environmental testing, training, and permit filings to maintain compliance with all environmental standards
4. Environmental Health and Safety Manager Job Summary
- Policy Support: Support the business management of HSE policy and guidelines
- System Implementation: Guarantee, by company guidelines, the implementation and updating of HSE systems
- Procedure Monitoring: Monitor the effective implementation of the procedures for the safety and environment system and update them in line with changes in company legislation and directives
- Incident Statistics: Carry out statistics on accidents/incidents, identifying trends and suggesting improvement plans
- Medical Coordination: Coordinate the competent doctor and the group RSPP
- Training Coordination: Coordinate compulsory HSE training and medicine activity
- Helpdesk Service: Provide helpdesk service to all employees on HSE activities
- Software Management: Manage HSE software, orders for personal protective equipment, etc.
- Budget Planning: Plan, prepare and discuss annual HSE budgets and quarterly reviews
- Legislative Support: Support activities under Legislative Decree 231
- Audit Coordination: Coordinate both internal and external HSE audits
- Legal Liaison: Deal with the Legal department and the O.D.V. (Organismo di Vigilanza)
5. Environmental Health and Safety (EHS) Officer Accountabilities
- HSE Administration: Conduct organized and professional administration of HSE at the Acworth Manufacturing Facility
- System Management: Act as an administrator in the HSE IndustrySafe system and perform activities of an administrator such as correction of entries and review of incident investigations
- Software Mastery: Master IndustrySafe safety software and become very familiar with obtaining records and reports from the system
- Trend Analysis: Use analytical skills to examine trends and develop processes that are proactive in nature to address negative trends and issues
- Safety Auditing: Perform periodic and regular site safety audits and inspections
- Inspection Monitoring: Monitor inspection reports and monitor corrective actions for follow-up and completion
- Training Management: Manage all aspects of site training, including the tracking of training and ensuring that all are sufficiently trained
- Incident Management: Manage all aspects of incident investigation, corrective actions, and work with Site supervision to ensure all incidents are fully investigated and documented
- Behavior Improvement: Analyze accident/incident trends and develop/implement recommendations to improve safety behaviors and safety record
- Environmental Oversight: Manage all aspects of environmental management for the site
- Return Support: Actively support the return-to-work process and the site management to optimize return-to-work timeliness and opportunities to return to work with light-duty restrictions
- Relationship Building: Establish and maintain good working relationships with peers, management, and site personnel
- Talk Execution: Ensures that toolbox talks are executed, signed by workers and filed
- Maintenance Coordination: Manage preventive and corrective maintenance tasks and the work order process for facility maintenance
6. Environmental Health and Safety (EHS) Supervisor Functions
- Program Leadership: Leads all facility safety programs and initiatives
- Team Leadership: Leads the safety team
- Training Delivery: Provides and/or supports all necessary safety training for FFS associates
- New Hire Training: Provides for new associate hire training
- Environmental Management: Manages environmental programs
- Waste Management: Manages hazardous waste collection and removal
- Recycling Documentation: Manages recycling trailer swaps and documentation of use/destruction documents
- Regulatory Liaison: Acts as liaison for consultant SHE services and regulatory agency inspectors
- Incident Follow-up: Investigates all safety incidents and follows up on corrective and preventative actions
- Sanitation Oversight: Manages the sanitation team
- Medical Coordination: Coordinates associate medical surveillance testing
- SOP Development: Develops SOPs for all job-related activities
- Permit Tracking: Tracks and updates facility permits
- OSHA Reporting: Assists the Human Resources department with reportable injury/OSHA reporting
- Regulation Education: Commits to continuing education on SHE items to stay informed of all current regulations