Updated: Aug 20, 2025 - The Continuous Improvement Manager coordinates cross-functional initiatives to ensure execution is on time, within budget, and aligned with quality standards. This role leads and supports operational excellence efforts that improve compliance, efficiency, yields, and throughput while fostering a continuous improvement mindset. The manager also drives the implementation of global methodologies, supports KPI development, and resolves processing challenges.
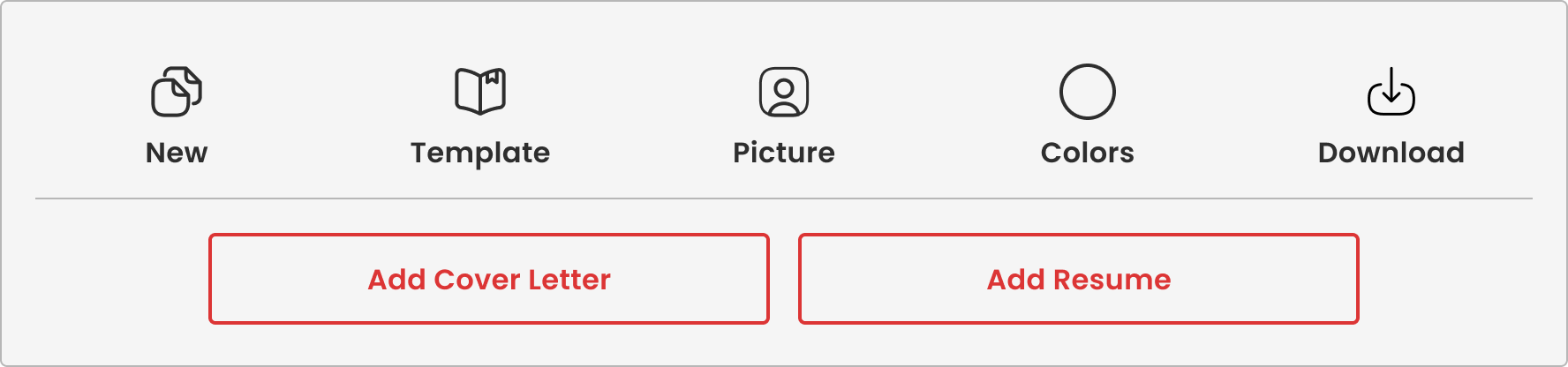

Tips for Continuous Improvement Manager Skills and Responsibilities on a Resume
1. Continuous Improvement Manager, XYZ Manufacturing, Denver, CO
Job Summary:
- Find and analyze the issues related to equipment and processes during the daily operation, lead the root cause analysis and problem solving
- Familiar with the operation process flow, proactive point out the improvement areas, and drive the suggestions, analyses, and improvement actions to happen
- Involved in the equipment automation and people saving project, including the study and improvement of the people allocation
- Responsible for the ISO and GMP and ensuring the effective monitoring and control of the GMP
- Involved in the related new product trial and initiation of normal production
- Follow up on the related issues, collect the relevant production data, finalize the headcount and formalize the SOP
- Involved in debugging the new equipment and coordinating and following up on the issues associated with production and engineering
- Implementation of the employee suggestion activity
- Implementation of improvement tools like TPM, Lean, Project Management (Scrum/Sprint), and Six Sigma.
- Promote the continuous improvement of culture, incentive, and award the team and individual for continuous improvement behaviors.
Skills on Resume:
- Root Cause Analysis (Hard Skills)
- Process Optimization (Hard Skills)
- Automation Projects (Hard Skills)
- GMP Compliance (Hard Skills)
- New Product Introduction (Hard Skills)
- Equipment Debugging (Hard Skills)
- Lean Implementation (Hard Skills)
- Team Motivation (Soft Skills)
2. Continuous Improvement Manager, ABC Logistics, Atlanta, GA
Job Summary:
- Develop and own the annual CI plan for the facility
- Develop and lead the implementation of employee engagement teams to support lean initiatives
- Responsible for the overall effectiveness of the kaizen activity
- Developing and implementing improvements to eliminate operational wastes in the process while managing and evaluating multiple projects.
- Effectively utilize the 8-Step Problem Solving process to lead through problem-solving exercises as it pertains to the elimination of waste.
- Drive and implement improvements with a major focus on Changeover Reduction
- Develop Lean Manufacturing training materials, coordinating and providing Lean Manufacturing direction with the support functions such as Maintenance, Materials, Quality, HR and Engineering.
- Train associates on Improvement Tools and Methodologies
- Implement and maintain visual workplace standards
- Implement tools to improve manufacturing performance
Skills on Resume:
- Annual CI Planning (Hard Skills)
- Employee Engagement (Soft Skills)
- Kaizen Leadership (Hard Skills)
- Waste Elimination (Hard Skills)
- Problem Solving (Hard Skills)
- Changeover Reduction (Hard Skills)
- Lean Training (Hard Skills)
- Visual Management (Hard Skills)
3. Continuous Improvement (CI) Manager, Standard Tech Solutions, Phoenix, AZ
Job Summary:
- Efficiently manage and challenge external suppliers to ensure maximum return for the funds invested
- Lead market research projects for assigned Categories and Clients that are relevant to the business, focusing on the needs of internal and external clients, respecting CI global standards
- Responsible for all improvement tools and techniques, ensuring all key operational processes are accurately mapped
- Ensure consistent methods are adopted in all areas of the business
- Project managing key processes and system-based changes and problems to improve operational efficiency across the site
- Review of KPIs and productivity across the site to continuously improve delivery for the customer
- Lead and develop a team to become self-sufficient, proactive leaders of the future
- Training and development of staff in improved processes.
- Continually review and adjust the strategy in line with internal and external changes.
- Plan all site activities on a master schedule and hold others accountable to the timelines to ensure the on-time delivery of the strategy.
Skills on Resume:
- Supplier Management (Hard Skills)
- Market Research (Hard Skills)
- Process Mapping (Hard Skills)
- Standardization Methods (Hard Skills)
- Project Leadership (Hard Skills)
- KPI Review (Hard Skills)
- Team Development (Soft Skills)
- Strategic Planning (Hard Skills)
4. Continuous Improvement Manager, Green Energy Corp, Sacramento, CA
Job Summary:
- Create and manage resource plan, testing strategy, testing plan, change management plan, cutover or deployment strategy and plan
- Monitor and control project activities and deliverables
- Evaluate complex situations accurately and identify viable solutions
- Manage relationship with project stakeholders, keeping stakeholders informed of progress and issues to manage expectations on all project requirements and deliverables
- Ensure proper use of methodology, tools, and procedures
- Be a key actor and contributor to the Category Plans strategy, GBU Plans and local clients' plans.
- Execute quantitative and qualitative CI studies in Mexico, Colombia and CAM
- Manage, track and inform key stakeholders of the Category Plans strategy
- Be the CI expert for category-specific discussions with senior clients
- Be the first point of contact for category-specific consumer insights questions from regional key stakeholders as well as global ones, in what matters to Mexico, Colombia, and CAM.
Skills on Resume:
- Resource Planning (Hard Skills)
- Project Monitoring (Hard Skills)
- Solution Evaluation (Hard Skills)
- Stakeholder Management (Soft Skills)
- Methodology Compliance (Hard Skills)
- Strategy Contribution (Hard Skills)
- Insight Execution (Hard Skills)
- Client Communication (Soft Skills)
5. Continuous Improvement Manager, Riverdale Plastics, Louisville, KY
Job Summary:
- Develop and oversee the day-to-day activities of the supervisors and staff of the alarm masking and quality assurance teams
- Ensure that all work is done properly, according to company standards and promptly
- Standardize and streamline processes and procedures to improve productivity and efficiency
- Monitor staff work for quality assurance to foster continuous process improvement and provide excellent service to all customers
- Define and manage metrics, ensure customer satisfaction, and report on performance related to customer accounts
- Analyze reports with the intent to identify potential operational improvement initiatives
- Initiate projects that focus on operational excellence through process improvement and/or enhancement in the use of technology
- Maintain a safe and secure work environment by following safe practices
- Conduct the project planning activities and manage the execution of large-scale, high-risk, or strategic projects according to plan
- Establish/ define benchmark, identify opportunities, set targets and timelines using essential management tools
Skills on Resume:
- Team Supervision (Soft Skills)
- Process Standardization (Hard Skills)
- Quality Monitoring (Hard Skills)
- Customer Satisfaction (Soft Skills)
- Performance Metrics (Hard Skills)
- Operational Analysis (Hard Skills)
- Project Execution (Hard Skills)
- Benchmark Setting (Hard Skills)
6. Continuous Improvement Manager, HealthSafe Inspections, Portland, OR
Job Summary:
- Introducing and supporting a culture of continuous improvement throughout the business
- Improving processes through people and change management
- Making sure every product is the best can make
- Improving green credentials and reducing environmental impact
- Implementing change and improvement through a structured and process-based system.
- Delivering measurable and desired improvements within the cultural boundaries of the business.
- Improvements to processes and procedures aimed at driving optimal performance.
- Collaborating with internal and external partners to create improvements through the whole supply chain.
- Recommending and developing improvement projects across quality, staff wellbeing, productivity, equipment, facilities and operational costs.
- Planning, monitoring and reporting on the progress of improvement projects.
Skills on Resume:
- Continuous Improvement (Soft Skills)
- Change Management (Soft Skills)
- Product Quality (Hard Skills)
- Environmental Impact (Hard Skills)
- Structured Implementation (Hard Skills)
- Cultural Alignment (Soft Skills)
- Process Enhancement (Hard Skills)
- Supply Chain Collaboration (Soft Skills)
7. CI Manager, Efficiency Experts, Miami, FL
Job Summary:
- Drives and supports the implementation of continuous improvement activities throughout the plant.
- Leads site pre-analysis that includes baseline operational and financial measurements.
- Continuously challenges conventional thinking, drives accountability for site or functional results and deployment, and sustains the internal CI system.
- Teaches continuous improvement thinking by both leading and coaching others to lead Kaizen events daily.
- Serves as a change agent and key mentor/ improvement coach for Team Leaders.
- Identifies and shares best practices from inside and outside of the plant with other plants within the group and with other Business Units.
- Coordinates and assists Kaizen and problem-solving teams in the definition of continuous improvement or problem-solving project planning concerning scope, time, quality, budget, milestones, allocation of resources, etc.
- Participates in the development of specifications for new equipment to comply with Lean FMOS principles.
- Develop and implement an effective CI strategy that encompasses all site functions.
- Ensure this strategy meets the goals of the site and overall business strategy, ensuring all stakeholders are engaged.
Skills on Resume:
- CI Implementation (Hard Skills)
- Operational Analysis (Hard Skills)
- Accountability Driving (Soft Skills)
- Kaizen Coaching (Soft Skills)
- Change Mentoring (Soft Skills)
- Best Practice Sharing (Soft Skills)
- Project Planning (Hard Skills)
- Strategy Development (Hard Skills)
8. Supply Planning Project and Continuous Improvement Manager, Dynamic Fabricators, Minneapolis, MN
Job Summary:
- Supports the Supply Planning Hub Manager and the regional CI manager in developing, deploying and managing the yearly plans and strategy in four main areas
- Lead specific planning projects or task forces in one or across multiple planning teams/sites within the ICO Metal Hub
- Ensure the required service to the customer and the appropriate balance with costs and inventory for both finished goods and materials.
- Coordination and implementation of cross-planning hub initiatives, pursuing the targets on Service, Inventory and SLOBS, both through MDI and Tiers and improvement projects
- Deploy improvements on the core planning processes or in the standardization across sites.
- Continuously optimize the current planning tools by ensuring the settings/parameters support and fit business processes.
- Participate in central tool/process development/deployment projects, ensuring sustainability.
- Represents the regional ICO Metal planning team in bigger cross-functional projects
- Alignment with Procurement, Manufacturing, and Logistics on tactical and operational level process improvements and initiatives
- Lead or participate in RCA and corrective actions to resolve issues
Skills on Resume:
- Strategy Deployment (Hard Skills)
- Project Leadership (Hard Skills)
- Service Optimization (Hard Skills)
- Cross-Planning Coordination (Hard Skills)
- Process Standardization (Hard Skills)
- Tool Optimization (Hard Skills)
- Cross-Functional Collaboration (Soft Skills)
- Root Cause Resolution (Hard Skills)
9. Supply Planning Project and Continuous Improvement Manager, Quantum Industrial, Birmingham, AL
Job Summary:
- Supporting the continuous development and execution of improvement projects related
- Supply planning within the ICO Metal Hub, in charge of the supply planning activities for six production sites
- Support the Supply Planning Hub Manager and the regional CI manager
- Continuous development of the supply planning and performance management processes.
- Optimal setup of the planning tool to perform the day-to-day planning activities.
- Lead on specific planning projects in one or across multiple planning teams/ sites
- Support on side projects and the deployment of the strategy and operational plans into the region.
- High-quality stakeholder management and the capacity to influence the planning teams regarding the importance of improvements.
- Work in an agile manner to cope with changes in priorities/projects based on business needs and findings.
Skills on Resume:
- Project Execution (Hard Skills)
- Supply Planning (Hard Skills)
- Process Development (Hard Skills)
- Tool Configuration (Hard Skills)
- Strategic Support (Hard Skills)
- Stakeholder Influence (Soft Skills)
- Agile Adaptability (Soft Skills)
- Regional Coordination (Hard Skills)
10. Continuous Improvement Manager, Pure Water Systems, Las Vegas, NV
Job Summary:
- Facilitate the education of the team in the principles, philosophies and tools of CI.
- Administer training programs that foster cross-functional deployment of continuous improvement.
- Develop, train and mentor employees to foster a strong culture of continuous improvement.
- Collaborate with counterparts within and outside the regions to ensure consistency among processes and procedures.
- Create plans and engage with the leadership team to close any gaps identified.
- Challenge management thinking and insist on appropriate practices such as: Visiting the factory floor daily, Confirming standardized processes, Demanding factual data, Insisting that problems are made visible, Questioning to ensure the root cause has been found, Supporting the standard meeting governance
- Drive the standardization of all structures, work, training, procedures and records across the plant.
- Ensure the new standard is documented, trained and confirmed when improvements are made to processes.
- Conduct ongoing reviews of the plant’s continuous improvement performance to understand the level of maturity.
- Coaching and training others in the use of TPM – total productive maintenance.
Skills on Resume:
- CI Training (Hard Skills)
- Employee Mentoring (Soft Skills)
- Cross-Functional Coaching (Hard Skills)
- Process Consistency (Hard Skills)
- Leadership Engagement (Soft Skills)
- Standards Enforcement (Hard Skills)
- Performance Review (Hard Skills)
- TPM Coaching (Hard Skills)
11. Continuous Improvement Manager, Sustainable Operations Inc., Hartford, CT
Job Summary:
- Identify and deliver margin-enhancing cost optimisation initiatives.
- Design and implement the ways of working and behaviours to sustain the initiatives captured.
- Create and embed a ‘cost ownership’ mentality within the team.
- Ensure the site's key performance indicators (KPI’s) (Safety, Quality, Service and Cost) are achieved through a rigorous performance management system.
- Implement the standard meeting governance that supports the delivery of the metrics.
- Identify performance gaps, trends, and actions required to improve.
- Align the site KPI structure with functional and global metrics.
- Support the establishment of floor-level metrics within the KPI tree.
- Act as a change agent, coaching, mentoring and influencing at all levels to affect the required CI culture.
- Act as a key member and influencer within the site leadership team.
Skills on Resume:
- Cost Optimization (Hard Skills)
- Behavioral Implementation (Soft Skills)
- Cost Ownership (Soft Skills)
- KPI Management (Hard Skills)
- Governance Structure (Hard Skills)
- Performance Analysis (Hard Skills)
- CI Culture Coaching (Soft Skills)
- Leadership Influence (Soft Skills)
12. Continuous Improvement Manager, Alloy Manufacturing Co., Peoria, IL
Job Summary:
- Direct company lean activities and continuous improvement program to meet budget and operations goals
- Develop, establish, and maintain a performance measurement system
- Establish performance goals and provide policy assessments and reporting for senior management
- Manage shop floor meetings
- Provide suggestions and strategic advice for key decisions and changes
- Manage projects ranging from small improvement projects to new product implementations
- Employing Lean methodologies to build a culture of Continuous Improvement
- Leading and facilitating Lean workshops, events, and training sessions around Value Stream Mapping, TPI, Kanban, Standard Work, etc.
- Identifying and eliminating waste within business practices and production
- Assisting the Director of Operations in developing and implementing a Continuous Improvement strategy
Skills on Resume:
- Lean Management (Hard Skills)
- Performance Measurement (Hard Skills)
- Policy Reporting (Hard Skills)
- Strategic Advising (Soft Skills)
- Project Management (Hard Skills)
- Lean Facilitation (Hard Skills)
- Waste Elimination (Hard Skills)
- CI Strategy Support (Hard Skills)
13. Continuous Improvement Manager, Precision Cast Products, Mesa, AZ
Job Summary:
- Plans, coordinates, and directs quality management programs designed to ensure continuous improvement of products and processes consistent with established GPE standards.
- Develops performance specifications and analyzes statistical data to determine proposed quality control methodologies for the sustainability expectancy of current solutions and processes are effective.
- Formulates and maintains quality control objectives and coordinates objectives with other leaders in GPE.
- Plans, coordinates and directs inspection and testing of project engineering deliverables to manage adherence to quality processes, standards, and deliverables for GPE’s internal and external customers.
- Investigate customer complaints regarding the quality and adjust quality process standards
- Aligns the focus of continuous improvement efforts with the objectives and strategies of GPE.
- Identifies the GPE continuous improvement team’s resource needs.
- Sets process metric goals in partnership with GPE groups and decision-makers to drive performance improvement in the project lifecycle.
- Provide Six Sigma project (coaching) to project team members, Green Belts, and Champions (using Lean Six Sigma methodologies).
- Analyze, investigate, and pursue resolution of any corrective actions or complaints identified for the engineering team, coordinating the communication of progress both internally and with Dematic’s Quality team and Environment, Health and Safety team
Skills on Resume:
- Quality Management (Hard Skills)
- Statistical Analysis (Hard Skills)
- Quality Objectives (Hard Skills)
- Inspection Coordination (Hard Skills)
- Complaint Resolution (Soft Skills)
- Strategy Alignment (Soft Skills)
- Resource Planning (Hard Skills)
- Six Sigma Coaching (Hard Skills)
14. Continuous Improvement Manager, Quality Solutions Tech, Greensboro, NC
Job Summary:
- Act as an expert consultant/advisor/facilitator to help business units implement transformational and continuous improvement process changes
- Coordinate kaizen teams to prepare for project launches, ongoing project tracking, and provide analysis of tangible savings
- Conduct analysis, generate ideas, and identify business process improvement opportunities that would lead to significant productivity enhancements and Owner satisfaction
- Develop KPI’s, dashboards and other reporting to measure results against standards
- Synthesize information and meeting notes to create presentation materials for senior leaders
- Represent the Operations Team when working with other departments on cross-functional initiatives
- Collaborate with Blackbelts, Greenbelts, Yellowbelts and the Lean Guiding Team to ensure annual departmental objectives are on track
- Support Yellow belt enterprise training programs and offer ongoing mentoring
- Maintain compliance with all audit, risk management requirements and internal policies
- Develop publish-ready content and communications related to Continuous Improvement and Lean Strategy through various channels
- Train and coach others on innovative techniques to identify opportunities within existing processes
- Suggest best practices to leverage as new processes are being implemented.
Skills on Resume:
- Process Consulting (Soft Skills)
- Kaizen Coordination (Hard Skills)
- Opportunity Analysis (Hard Skills)
- KPI Development (Hard Skills)
- Executive Communication (Soft Skills)
- Cross-Functional Collaboration (Soft Skills)
- Lean Mentoring (Soft Skills)
- Compliance Support (Hard Skills)
15. Continuous Improvement Manager, Fabricated Parts Inc., Fort Wayne, IN
Job Summary:
- Train, support, and coach everyone in the company in Lean systems thinking, culture, behaviors and methodologies.
- Mentoring those who wish to achieve higher accreditations (Lean Systems Green and Black Belts).
- Working with every team across the company to deliver Year-on-Year savings through excellent project execution.
- Develop and monitor risk-management procedures and analyze non-conformance costs to identify and report recurring issues.
- Mentors and develops the capabilities of others in process excellence, lean principles, statistical tools, and change management practices.
- Develops and builds relationships with decision-makers to propagate cultural transformation.
- Facilitates kaizen events, acting as an advisor to facilitate troubleshooting and resolving complex problems within GPE groups across the North American regional offices.
- Supports a corporate-wide lean culture by engaging stakeholders outside of GPE.
Skills on Resume:
- Lean Coaching (Soft Skills)
- Accreditation Mentoring (Soft Skills)
- Project Execution (Hard Skills)
- Risk Analysis (Hard Skills)
- Capability Building (Soft Skills)
- Cultural Transformation (Soft Skills)
- Kaizen Facilitation (Hard Skills)
- Stakeholder Engagement (Soft Skills)
16. Continuous Improvement Manager, Industrial Systems Corp., Sparks, NV
Job Summary:
- Promote accelerated implementation of ABS from casting to shipping
- Assist in developing and strengthening the ABS Principles and Concepts with key customers and key suppliers
- Assist departments in training, developing and properly utilizing Rapid Problem Solving
- Assist departments in a better understanding of hoshin planning, step change activities, kaizen, and 5S deployment
- Drive REX's vision and goals to reduce machine unplanned downtime and leverage predictive data.
- Lead the development and implementation of the overall Total Productive Maintenance (TPM) program, including establishing the standardized visual system, the overall assessment process, training, and building a system for engaging volunteers for TPM events.
- Lead the overall kaizen plan to engage the workforce in eliminating waste through ABS and in growing their ABS capabilities.
- Ensure that ABS and Reliability activities are tied to closing business gaps and generating value for Lancaster Operations.
- Identify and evaluate opportunities for cost reduction and/or productivity improvements with regard to maintenance activities, particularly seeking to minimize the investment required for spare parts and maintenance supplies.
- Evaluate equipment failures and failure history to identify and recommend potential capital or expense projects to eliminate equipment failures.
Skills on Resume:
- ABS Implementation (Hard Skills)
- Customer Collaboration (Soft Skills)
- Problem Solving Training (Soft Skills)
- Hoshin Planning (Hard Skills)
- Downtime Reduction (Hard Skills)
- TPM Leadership (Hard Skills)
- Kaizen Engagement (Soft Skills)
- Maintenance Optimization (Hard Skills)
17. Continuous Improvement Manager, Dynamic Production Services, Yonkers, NY
Job Summary:
- Manage and drive EHS improvements for employees and contractors.
- Lead in a manner that recognizes that accident, injury, and environmental incident prevention are equal in importance to production, quality, delivery, recovery and cost control.
- Accepts the responsibility to work safely and promote safety consciousness among other employees using the tools of Human Performance (HP).
- Partner with the Procurement function to ensure appropriate contracts and service agreements are in place to support the operations.
- Support a culture of continuous improvement and reliability.
- Lead the Team culture and steering committee for the Lancaster site.
- Build a vision for the continued evolution of team norms and expectations.
- Ensure that Reliability principles are leveraged to meet environmental compliance and ISO 14001 standards across all operations and shifts
- Coach and develop the skills of direct and indirect reports.
- Provides the systemic improvements and waste elimination efforts (through kaizens) to achieve/exceed plant objectives.
- Develop, own, monitor, and achieve a major maintenance expense budgeting process across the facility
Skills on Resume:
- EHS Management (Hard Skills)
- Safety Leadership (Soft Skills)
- Contract Coordination (Hard Skills)
- Reliability Culture (Soft Skills)
- Team Building (Soft Skills)
- Compliance Standards (Hard Skills)
- Coaching Development (Soft Skills)
- Budget Management (Hard Skills)
18. Continuous Improvement Manager, Optimal Operations Group, Lincoln, NE
Job Summary:
- Review and Management of Current Operating Standards related to Back End and Front End Operations in Stores.
- Evaluation of performance and efficiencies as it relates to Receiving, Replenishment, Put-away, and RTVs, Omni-Channel Fulfilment, POS, Pricing, and Price Communication in stores.
- Identify and implement opportunities to enhance performance through effective use of business intelligence tools (BI).
- Participate in the development, installation and training of system enhancements.
- Identify opportunities to train processes to maintain operating standards and achieve Operational Excellence.
- Work directly with stores to ensure efficient execution.
- Work directly with stores to identify and eliminate inefficiencies.
- Communicate opportunities for improvement to both Field and Central Leadership.
- Recognize performance opportunities and react promptly to address and improve issues as they arise.
- Work as a liaison between Corporate Logistics and the stores to address logistics issues as they arise.
Skills on Resume:
- Standards Management (Hard Skills)
- Performance Evaluation (Hard Skills)
- BI Implementation (Hard Skills)
- System Training (Hard Skills)
- Process Training (Hard Skills)
- Store Collaboration (Soft Skills)
- Efficiency Optimization (Hard Skills)
- Corporate Liaison (Soft Skills)
19. Continuous Improvement Manager, Process Excellence Partners, Little Rock, AR
Job Summary:
- Prioritize, plan, and execute multiple supply chain process improvement initiatives aimed at improving process efficiency, reducing costs, or improving reliability
- Collaborate with key stakeholders across the organization to proactively identify risks, align on priorities, and develop/implement solutions that span multiple functions
- Serve as the subject matter expert on vendor-to-DC supply chain processes, and represent the Procurement team in key business decisions
- Identify gaps in current supply chain processes, and forecast future gaps based on product and operations roadmap, bringing innovative solutions to the project pipeline to ensure continue scale operations at a rapid pace
- Partner with the supply chain technology team to ensure that systems and processes are thoroughly integrated, meet current/future business requirements
- Support the creation of standard operating procedures and documentation across different areas of the supply chain
- Build, develop, and lead a small team of continuous improvement analysts
- Participate in training and the successful execution of physical inventory
- Assist in the resolution of facilities and equipment issues
Skills on Resume:
- Process Improvement (Hard Skills)
- Stakeholder Collaboration (Soft Skills)
- Supply Chain Expertise (Hard Skills)
- Gap Analysis (Hard Skills)
- Tech Integration (Hard Skills)
- Procedure Standardization (Hard Skills)
- Team Leadership (Soft Skills)
- Inventory Execution (Hard Skills)
20. Continuous Improvement Manager, Efficiency Engineers, Boise, ID
Job Summary:
- Work with leadership and employee teams to resolve implementation issues, managing communication processes as well as ensuring consistency in implemented processes and programs.
- Facilitates continuous improvement interventions and employee involvement teams throughout the site and associated sites
- Assures that predicted improvements are implemented, measured, driven to closure, and provide operational results.
- Assures that predicted savings are tracked and validated.
- Develops a clear and compelling Continuous Improvement Strategy for their location in close cooperation with the Plant Director and the Sr. Director Continuous Improvement
- Actively seeks and evaluates process improvements in the plant and translates them into CI projects, helping to increase output and efficiency in the plant
- Holds project meetings and ensures their follow-up by monitoring the progress of planned improvements to assure their timely execution
- Operates cross-functionally to assure information flow and understanding of overall process improvement direction and expected results.
- Helps define and maintain KPI structure at the plant and regional level
Skills on Resume:
- Implementation Management (Soft Skills)
- Improvement Facilitation (Soft Skills)
- Improvement Assurance (Hard Skills)
- Savings Tracking (Hard Skills)
- Strategy Development (Soft Skills)
- Process Evaluation (Hard Skills)
- Project Meetings (Soft Skills)
- Cross-Functional Operations (Soft Skills)
21. Continuous Improvement Manager, Norwood Manufacturing Inc., Springfield, MO
Job Summary:
- Lead the plant Continuous Improvement function to implement and sustain a strong Lean program and culture while ensuring the delivery of key Quality, Service and Cost Objectives
- Support other plant locations to ensure the overall lean program and culture advance for Hollister
- Develop a Continuous Improvement implementation plan in line with the Global Continuous Improvement (CI) Strategy and Plant Strategy
- Participate as a key member of the Global CI team
- Develop and standardize the Continuous Improvement of global programs
- Participate as part of the Plant Leadership Team at the local site to engage, gain buy-in, and support for the implementation of changes
- Implement the CI plan in conjunction with the operating area using lean tools
- Lead improvement projects/programs such as Kaizen, Value Stream Mapping, 5S, and manage the Cost events to reach the desired future state and assure sustainability
- Foster a culture of continuous improvement through front-line employee engagement with standard work, on-the-floor problem-solving solving and idea generation
- Gain and develop lean knowledge to train and coach the plant organization on CI methods, lead lean events and drive lean culture
- Teach lean tools and methodology at all levels within the plant
Skills on Resume:
- Lean Leadership (Soft Skills)
- CI Planning (Hard Skills)
- Strategy Alignment (Hard Skills)
- Team Engagement (Soft Skills)
- Project Execution (Hard Skills)
- Lean Training (Hard Skills)
- Problem Solving (Hard Skills)
- Culture Building (Soft Skills)
22. Continuous Improvement Manager, Apex Plastics Group, Dalton, GA
Job Summary:
- Lead a team of Continuous Process Improvement professionals, providing direction and support to achieve the company's goals in delivery, cost, cash and customer satisfaction
- Drive a culture of Continuous Process Improvement, data-driven decision making and effective project management across the organisation
- Collaborate with the Supply Chain Operations leadership team to identify and implement projects, process improvements, increased efficiency, and cost reduction
- Execute projects end-to-end and be able to offer key insights and present findings to senior leaders and stakeholders
- Gather and translate the voice of key stakeholders and work cross-functionally to truly understand the business processes and drive improvements
- Conduct gap analysis through surveys, workshops, and external reviews of the business
- Benchmark processes, both internally and externally, and strive to introduce and implement best-in-class practices and solutions
- Institutionalise process mapping to address cycle time and efficiency challenges across the supply chain and operations, end business processes
- Understanding and sharing of LEAN principles to drive productivity with a focus on efficiency, cost avoidance and gross margin improvement
- Prepare presentations to senior leaders, introducing recommendations and highlighting any risks and costs associated with these changes
- Provide ongoing coaching and mentoring to Sponsors, Black Belt / Green Belt candidates on the proper use of tools and improvement processes
- Drive a governance and cadence to ensure that performance is measured, shared and acted upon promptly
Skills on Resume:
- Lean Leadership (Soft Skills)
- CI Planning (Hard Skills)
- Strategy Alignment (Hard Skills)
- Team Engagement (Soft Skills)
- Project Execution (Hard Skills)
- Lean Training (Hard Skills)
- Problem Solving (Hard Skills)
- Culture Building (Soft Skills)
23. Continuous Improvement Manager, Heritage Tool & Die, Erie, PA
Job Summary:
- Facilitate successful new product launches
- Work with a cross-functional team to develop control plans, enhanced inspection activities, pilot production runs, and successful capability studies
- Drive efforts to develop new products that meet or beat cost expectations and quality standards
- Assist in providing leadership and direction to all employees, including management team members, in the principles, concepts and execution of the Company
- Drive continuous improvement across Mansfield, TX, manufacturing operations to achieve results
- Develop, mentor, motivate, and coach employees on how to utilize the Company to accomplish the company's goals and objectives in the areas of quality, customer service levels, productivity, safety and working capital management
- Help develop and prepare tools, processes and policies about the Company's methods and objectives
- Utilize Pareto analysis and other Company tools to identify areas with opportunity for significant improvement
- Develop and facilitate plans to improve areas where major opportunities exist
- Prioritize efforts of significant impact and tactical benefit for plant metrics
- Work closely with key stakeholders to establish metrics and timelines for Company activities
- Assist with communication of expectations, deliverables, goals, etc., to drive desired outcomes and promote successes
- Evaluate individual product margins to identify opportunities to improve profitability
- Use tools such as Value Stream Maps to facilitate these efforts
Skills on Resume:
- Product Launches (Hard Skills)
- Cross-Functional Coordination (Soft Skills)
- Cost Management (Hard Skills)
- Leadership Support (Soft Skills)
- Performance Coaching (Soft Skills)
- Process Development (Hard Skills)
- Opportunity Analysis (Hard Skills)
- Stakeholder Alignment (Soft Skills)
24. Project Controls Continuous Improvement Manager, Ridgefield Packaging LLC, Ridgefield, WA
Job Summary:
- Validate project programmes and progress from both a buildability and technical perspective via audits and hold-point gateways
- Critical and Near-Critical Path analysis, and identification of the true drivers of project performance by forensic analysis
- Monitor and validate project KPI's and validate RAG assessments to inform project risk assessment
- Contribute to the efficient way planning and project controls are undertaken by providing feedback on lessons learnt and processes, and solutions to ISG management
- Identify and assist the management of project risk
- Contribute to problem-solving both at the strategic and project levels
- Develop relationships with internal teams, consultants, clients and suppliers
- Support planners and non-planners in principles, techniques and software
- Ad-hoc support to key live and tender projects
Skills on Resume:
- Project Auditing (Hard Skills)
- Path Analysis (Hard Skills)
- KPI Validation (Hard Skills)
- Process Feedback (Soft Skills)
- Risk Management (Hard Skills)
- Strategic Problem-Solving (Soft Skills)
- Stakeholder Relations (Soft Skills)
- Planning Support (Hard Skills)
25. Continuous Improvement Manager, TriPoint Engineering Services, Tulsa, OK
Job Summary:
- Act as an agent of change, owning and promoting the corporate Continuous Improvement (CI) vision under the direction of the Senior Manager of Continuous Improvement
- Collaborate with plant management to craft and implement a site-specific Continuous Improvement plan that is aligned with the corporate Continuous Improvement Plan
- Work closely with the Plant manager to systematically drive the Continuous Improvement vision, implement Continuous Improvement projects, improve OEE, and reduce operational losses
- Successfully train and coach the facility team members in the use of Continuous Improvement
- Champion business processes across the account
- Create and nurture a network of business process contacts across the Account, working across multiple delivery streams (finance, contract management and property management)
- Oversee and support the creation of business processes for the account to include a library of generic process maps that can be adapted to fit any public sector PM delivery during contract mobilisation
- Ensuring that mapping is fit for purpose and is reviewed at timely intervals
- Ensure that best practice is adopted across all contract locations
- Representing the account on all internal and external business process matters
Skills on Resume:
- Change Leadership (Soft Skills)
- CI Planning (Hard Skills)
- OEE Improvement (Hard Skills)
- Team Coaching (Soft Skills)
- Process Ownership (Hard Skills)
- Cross-Functional Networking (Soft Skills)
- Process Mapping (Hard Skills)
- Best Practice Adoption (Soft Skills)
26. Continuous Improvement Manager, Beacon Process Solutions, Waco, TX
Job Summary:
- Manage regular activities for the operational team of Charging and Enforcement Policy Advisors to facilitate continuous improvement, change delivery and incident resolution
- Identify areas of operational delivery for quality assurance audit and conduct a review
- Ensure reports are completed on time and to the required quality standards, mitigating and escalating risks
- Support the Senior Business Analyst with ad hoc analysis and annual accounts assurance checks
- Contribute to the effective monitoring of supplier performance outputs, identifying issues and supporting the contract management team by escalating evidenced concerns promptly
- Manage and complete allocated project work, ensuring it is delivered by the brief
- Assist the management team in delivering coaching and support to individuals/teams to achieve competence and development in their role
- Providing functional delivery of continuous improvement and quality management across the airline
- Responsible for all improvement tools and techniques, control of all key operational processes and project management of key process changes
- Manage the improvement process through its complete life cycle from initial opportunity through to sign off and execution
- Develop best practice business and operational processes
- Experience in supporting process improvement and/or sustainable excellence
- Support and deliver the implementation of system upgrades and projects
- Develop a culture of continuous improvement and lean thinking
Skills on Resume:
- Operations Management (Hard Skills)
- Quality Assurance (Hard Skills)
- Risk Mitigation (Hard Skills)
- Data Analysis (Hard Skills)
- Supplier Monitoring (Hard Skills)
- Coaching Support (Soft Skills)
- Process Lifecycle (Hard Skills)
- Lean Culture Development (Soft Skills)
27. Continuous Improvement Manager, Copper Ridge Foods, Boise, ID
Job Summary:
- Acts as an overall continuous improvement ambassador and actively supports the change to coach and promote the use of new methods to drive efficiencies and standardization across the company
- Guide the management on the development and maintenance of continuous improvement capabilities to support operational excellence
- Provide support and guidance to all functions in the application of lean/continuous improvement techniques
- Manage process-related projects from start to finish
- Track, monitor, and report regularly on project status
- Monitor process improvement milestones to ensure on-time completion and sustainability
- Responsible for the achievement of process and continuous improvement KPIs in terms of profitability, quality and timing
- Develop, propose, prioritize, and execute process improvement projects
- Key tasks to include process mapping and process writing
- Design a repository/Document Control Center and establish a process to review, validate and maintain all documents and templates
- Use Lean and Six Sigma process improvement skills (i.e., value stream mapping, Kaizen, Charters, 5S, Gemba walks, root cause analysis) to identify and develop solutions that drive operational improvement
- Collaborate with IS/IT leaders to identify opportunities for improvement, organize resources, select and implement the appropriate solutions that simplify, standardize and ultimately bring cost reductions
- Ensure projects are delivered successfully
- Produces timely, detailed summaries and high-level reports
- Provides process improvement and digitalization implementation schedule
- Lead the development and execution of strategic planning aimed at reviewing the process and continuous improvement portfolio, facilitating information-gathering workshops to highlight opportunities and remove roadblocks
- Define the scope, objectives and estimated results of process improvement-related projects
- Leads project crew members through the process management methodology to complete desired outcomes
- Ensures that the proper Process methodologies, improvement analysis, and fact-based/data-driven decision-making are effectively applied throughout the projects
Skills on Resume:
- CI Advocacy (Soft Skills)
- Operational Excellence (Hard Skills)
- Lean Application (Hard Skills)
- Project Management (Hard Skills)
- KPI Achievement (Hard Skills)
- Process Mapping (Hard Skills)
- Digitalization Support (Hard Skills)
- Strategic Planning (Soft Skills)
28. Systems Reporting and Continuous Improvement Manager, Harbor Precision Machining, Traverse City, MI
Job Summary:
- Ensure compliance with relevant financial requirements, developing, implementing, and operating budgets for management activities
- Develop, document, implement and manage Supply Chain policies, processes, workflows, and templates which support adoption and education by internal customers and stakeholders
- Ensure alignment of Supply Chain outcomes with Supply Chain Plan, Corporate Plan, and stakeholder compliance standards
- Report on Supply Chain policy and framework
- Support the development of a proactive risk culture and compliance
- Support the provision of requirements for Internal Audit Processes and report on the status of initiatives because of prior Audit Findings
- Training and Systems development, implementing best practices across the ecosystem of requisition-to-pay systems, processes, and policies within Transgrid
- Implementing and supporting continuous improvement initiatives
- Working on regular process reviews and detailed process mapping of Supply Chain functions to map improvement elements, de-bottle functions and limit wastage in the process
Skills on Resume:
- Budget Management (Hard Skills)
- Policy Development (Hard Skills)
- Standards Alignment (Hard Skills)
- Risk Compliance (Hard Skills)
- Audit Support (Hard Skills)
- Systems Training (Soft Skills)
- Process Mapping (Hard Skills)
- CI Implementation (Hard Skills)
29. Continuous Improvement Manager, Skyline Assembly Works, Lexington, KY
Job Summary:
- Develop and deploy a CI strategy aligned with the division's strategy
- Update the CI development plan covering plant CI objectives, CI key activities and CI competence
- Develop an annual CI master plan for the plant
- Conduct EBS PULL workshop and identify key projects at plant levels, monitor progress and make sure to achieve target goals
- Deploy applicable CI tools to support plant goals
- Lead annual VSM event for plant level and guide product/department level VSMs
- Drive transactional projects through BPI to improve business processes
- Overall owner for plant level cost out, facilitate IDB workshop, build up project pipeline and drive execution
- Analyze cell and manufacturing layout, capacity, line balancing and facilitate to work out the improvements for productivity
- Through effective communication and CIF deployment, promote CI cultures within the plant, therefore engage all levels in the organization, also share plant best practices through the division platform
- Build up plant CI competency through providing professional coaching and mentorship to CI key members and the CI project team, and strengthen the bench depth within the plant
- Coordinate OpA and ELSS assessment, track actions and follow up
Skills on Resume:
- CI Strategy Development (Hard Skills)
- Master Planning (Hard Skills)
- Workshop Facilitation (Soft Skills)
- Tool Deployment (Hard Skills)
- VSM Leadership (Hard Skills)
- Process Improvement (Hard Skills)
- Cost Reduction (Hard Skills)
- CI Culture Promotion (Soft Skills)
30. Continuous Improvement Manager, Westfield Contract Manufacturing, Muncie, IN
Job Summary:
- Identifies, suggests, and implements best practices to facilitate the best solutions and methods that will optimize processes in all areas of the business
- Works with main clients and project and business leaders to identify the gap between current and desired results
- Analyzes current processes and designs improvements
- Leads cross-functional teams to project completion and project implementation
- Employs Six Sigma or related methodology and analytics into organizational operations to accomplish business objectives
- Works with senior-level management to integrate the Six Sigma or a related approach into the company’s business strategy
- Projects often include business suppliers and customers to fully integrate the Six Sigma methodology into the entire product value stream
- Design and implement a performance quality and improvement strategy and governance process for Brussels Hub
- Monitor the performance quality, identifying focus areas to drive and improve the performance and service quality of Brussels Hub towards customers
- Consolidate structural operational performance issues towards all stakeholders, and take actions to improve and remove these issues
- Follow up on quality spot-checks in various operational areas, to ensure all processes are following the GSOP and ISO standards
- Identify new and alternative approaches to improve the effectiveness and efficiency of business and operational processes, in line with the overall strategy and objectives of the Hub
- Roll out a structured approach, based on Continuous Improvement/First Choice, to lead process improvement processes and workshops
- Lead the QCC and SST teams, which are in charge of real-time monitoring on customers/shipments, and shipment recovery
Skills on Resume:
- Process Optimization (Hard Skills)
- Gap Analysis (Hard Skills)
- Cross-Functional Leadership (Soft Skills)
- Methodology Integration (Hard Skills)
- Performance Strategy (Hard Skills)
- Quality Monitoring (Hard Skills)
- Standard Compliance (Hard Skills)
- Customer Recovery (Soft Skills)
31. Continuous Improvement Manager, Mountain Valley Glassworks, Missoula, MT
Job Summary:
- Develop comprehensive business cases to support project prioritization and goals
- Observe and analyze operational processes, identifying improvements to eliminate waste and inefficient process steps and product flow
- Identify key and standard performance metrics and perform quantitative analysis to establish an objective baseline performance and forecast improvement margins
- Coordinate and lead teams involved in all aspects of the CI process
- Primary owner for the implementation of process improvements
- Responsible for the creation of value stream maps, risk analyses, measurement plans, short and long-term project solutions and capital project proposals
- Effectively communicate process opportunities, plans for solution, status of improvement implementations, and validation of results across all levels of the organization
- Develop and integrate metrics and KPIs that aid in monitoring the success of each project against goals
- Maintain proper and frequent communication among project sponsors, owners and team members
Skills on Resume:
- Business Case Development (Hard Skills)
- Process Observation (Hard Skills)
- Performance Analysis (Hard Skills)
- Team Leadership (Soft Skills)
- Improvement Implementation (Hard Skills)
- VSM Creation (Hard Skills)
- Organizational Communication (Soft Skills)
- KPI Integration (Hard Skills)
32. Continuous Improvement Manager, Bluestone Industrial Coatings, Cheyenne, WY
Job Summary:
- Develop and execute engineering projects targeted at predetermined opportunities with the support of other functions
- Identifying waste and cost reduction opportunities, bringing them to fruition
- Develop business cases and capital project justifications
- Short-lead travel to sites for operations and customer support
- Manage a continuous improvement program for the company
- Initiate improvement events
- Work with the plants on plant-level initiatives
- Report results to senior management
- Delivery Lead for business improvement workstreams
- Ensuring value-based delivery and evidence-based outcomes
- Support and provide management to BI Team members
- Central point of contact for all ongoing and identified pipelines of work relating to improvements
- Accountable for the improvement pipeline and delivery management
- Coach and mentor the business in key business improvement/lean/agile methodologies
Skills on Resume:
- Engineering Projects (Hard Skills)
- Cost Reduction (Hard Skills)
- Capital Justification (Hard Skills)
- CI Program Management (Hard Skills)
- Improvement Events (Hard Skills)
- Delivery Leadership (Soft Skills)
- Pipeline Management (Hard Skills)
- Methodology Coaching (Soft Skills)
33. Continuous Improvement Manager, Canyon Crest Logistics, Billings, MT
Job Summary:
- Manage the Sort Centre improvement plan to focus on the best customer experience at the lowest cost
- Help drive the implementation of Lean Standard Work at all levels of the site
- Disseminate Lean Standard Work principles across teams
- Develop a culture of continuous improvement and lean thinking
- Contribute to and facilitate Kaizen activities
- Train and support all levels in Kaizen activities
- Support, manage and validate the implementation of ATS ACES process changes
- Coordinate and prioritize process improvement activities and resources
- Standardize processes and actively share best practices across the CI network to avoid duplication
- Analyse process performance at a process path level
- Liaise between SC and EU to drive leverage of cross-SC process excellence
- Maintain strong relationships with ACES and Operations
Skills on Resume:
- Improvement Planning (Hard Skills)
- Lean Standard Work (Hard Skills)
- CI Culture Development (Soft Skills)
- Kaizen Facilitation (Hard Skills)
- Process Validation (Hard Skills)
- Resource Coordination (Hard Skills)
- Performance Analysis (Hard Skills)
- Stakeholder Collaboration (Soft Skills)
34. Continuous Improvement Manager, ForgeFlow Metalworks, Ogden, UT
Job Summary:
- Develop manufacturing operating system implementation plans for the related factory with a clear focus on zero defects, zero losses and a total involvement culture
- Put in place the standard MOS pillar structure (TPM pillar structure), enabler of the MOS continuous improvement programme in the plant
- Work effectively with cross-functional departmental leads (production, engineering, quality, safety, logistics, finance and HR) in rolling out the MOS programme
- Support the plant manager in the strategy deployment
- Agrees and puts in place standard performance indicators to measure consistency/compliance pillars progress and business contribution per pillar
- Actively monitor and follow up on the key performance indicators
- Based on monitoring of plant performance indicators, identify and manage efficiency issues that arise in the plants and develop plans/programmes for improvement
- Supports performing deep-dive analysis on efficiency issues
- Work closely with global pillar leaders to improve manufacturing operating system development and implementation
- Exhibit a strong focus on people development within own area and consistently improve capabilities and engagement in the local pillar leaders and members
Skills on Resume:
- MOS Implementation (Hard Skills)
- Pillar Structure Setup (Hard Skills)
- Cross-Functional Alignment (Soft Skills)
- Strategy Deployment (Hard Skills)
- KPI Monitoring (Hard Skills)
- Efficiency Improvement (Hard Skills)
- Deep-Dive Analysis (Hard Skills)
- People Development (Soft Skills)
35. Continuous Improvement Manager, Delta Fabrication Solutions, Topeka, KS
Job Summary:
- Establish an open feedback loop to promote a culture of transparency to influence and implement change
- Analyse processes and procedures and investigate shortfalls, issues, and complaints in current business processes
- Develop and prioritise process enhancement strategies across current systems and processes/procedures to identify continuous improvement opportunities
- Form multi-disciplinary teams with business participants to ensure buy-in and ownership of the outcomes
- Prepare continuous improvement business cases for endorsement (where appropriate)
- Build internal stakeholder relationships and collaborate with these stakeholders to implement improvements to IIP's practices
- Manage internal stakeholder relationships through regular, effective communication on continuous improvement projects
- Ensuring appropriate training is provided to IIP stakeholders when a change arises
- Ensuring sound documentation is established to facilitate in-depth understanding and responsibility over systems, processes and individual responsibilities
- Cultivate an ongoing change management culture and drive strong engagement with all key stakeholders in line with the Mirvac Values, including mentoring and coaching contributors
Skills on Resume:
- Feedback Culture (Soft Skills)
- Process Analysis (Hard Skills)
- Strategy Development (Hard Skills)
- Team Collaboration (Soft Skills)
- Business Case (Hard Skills)
- Stakeholder Engagement (Soft Skills)
- Change Training (Hard Skills)
- Mentoring Support (Soft Skills)
36. Continuous Improvement Manager, Ozark Valley Systems, Fayetteville, AR
Job Summary:
- Champion, develop and sustain a culture of continuous improvement (CI) and knowledge about related methodologies/ activities (Lean, Six Sigma, ALPS) across all areas of the site with a strong focus on manufacturing and operations
- Develop and expand local capabilities in applying continuous improvement tools and methods (Lean, Six Sigma) and promote a structured problem-solving approach
- Inject passion for this activity by providing a vision and direction for the future development and performance of the site
- Support and challenge the workforce and local MT in direction setting, prioritization (timing, resources, and sequence of actions) and implementation of improvement activities to best achieve the targets for the key performance indicators of the yearly site improvement plan
- Identify, validate, initiate and drive new improvement opportunities and promote the passion for excellence and delivering on commitments and values
- Manage the improvement project funnel including scoping, project assignment, resource planning, tracking of progress and benefits and controlling the sustainability of outcomes
- Supporting the customer's strategic change programme across warehouse and transport operations
- Supporting the development and growth of the M&S account
- Supporting the development strategy, including responsibility for the development of new solution sets
- Support the development and introduction of innovative solutions
- Facilitate, support and lead the generation of improvement opportunities based on KPI, Cost, Performance and Quality defects
Skills on Resume:
- CI Culture (Soft Skills)
- Lean Promotion (Hard Skills)
- Vision Leadership (Soft Skills)
- KPI Alignment (Hard Skills)
- Opportunity Identification (Hard Skills)
- Project Management (Hard Skills)
- Strategic Support (Soft Skills)
- Solution Development (Hard Skills)
37. Continuous Improvement Manager, Sandstone Mechanical, Rapid City, SD
Job Summary:
- Direct, develop and foster a culture of structured continuous improvement across the route, aligned to the continuous improvement strategy and framework
- Accountable for the effective delivery and engagement management and delivery of portfolio initiatives to deliver the continuous improvement strategy
- Manage the visibility, development and deployment of lean training across the route, including lean tools, techniques, leadership skills and behaviours
- Identify, coach and mentor local change agents on continuous improvement and lean tools, and support agents to make valuable contributions to the business and remain strategically aligned
- Develop training plans to meet business demand and maintain training and capability matrices
- Direct and drive a sustained culture of continuous improvement, challenging existing processes, exploring new ways of working, observing and benchmarking, providing feedback and change analysis and supporting proposals
- Work with route teams to identify and improve areas of poor performance through the deployment of lean tools and techniques
- Own and govern portfolios in line with business frameworks and benefit realisation models within agreed timeframes in budget and quality
- Establishing reporting mechanisms to deliver progress and KPI reports
- Highlighting risks to delivery and establishing countermeasures for resolution and tracking
- Manage the route plan for ‘Better Every Day’ improvements, taking ownership of the maturity assessment and managing the delivery of associated improvement activities
- Work across the route, region and business to embed strategic alignment across the route
Skills on Resume:
- CI Leadership (Soft Skills)
- Portfolio Delivery (Hard Skills)
- Lean Training (Hard Skills)
- Change Coaching (Soft Skills)
- Capability Planning (Hard Skills)
- Process Challenge (Soft Skills)
- Performance Improvement (Hard Skills)
- Strategic Alignment (Soft Skills)
38. Continuous Improvement Manager, Keystone Circuitry Inc., Reading, PA
Job Summary:
- Work safely by Rio Tinto's health, environment, safety, and community standards, as well as actively protecting and promoting an "injury-free" culture
- Lead and develop a team of Business Improvement and Productivity professionals
- Collaborate with the operations, technical, and central teams to set the direction of the productivity program
- Identify bottlenecks and opportunities for improvement projects to improve safety, employee engagement and productivity
- Act as the Site Lead for the deployment of the Rio Tinto Safe Production System (RTSPS)
- Support compliance with standardized processes, systems, and tools
- Apply and explain LEAN and Six Sigma concepts and methods
- Provide training for business improvement tools and methodologies
- Promote and establish a culture of improvement and mentor teams in implementing sustainable change
- Support management committees on strategic activities
- Facilitate the delivery of the portfolio of initiatives by engaging and supporting owners and developers
- Comprehensively coordinate transformation in its area of responsibility to deliver value to sites and business by supporting the execution of improvement projects
- Organize and prepare workshops to build full potential
- Define and supervise improvement approaches for complex issues
- Respond to ad-hoc requests to support urgent operational issues
Skills on Resume:
- Safety Leadership (Soft Skills)
- Team Development (Soft Skills)
- Program Direction (Hard Skills)
- Opportunity Identification (Hard Skills)
- System Deployment (Hard Skills)
- Lean Application (Hard Skills)
- Improvement Training (Hard Skills)
- Change Mentoring (Soft Skills)
39. Associate Continuous Improvement Manager, IronHill Modular, Athens, GA
Job Summary:
- Manage and execute broad improvement project deliverables as part of the SSP Program team on time, accurately, and technically correct, with quantifiable change
- Work with SSP Program team members, IT and Operations
- Provide specific project deliverables and manage assigned deliverables as part of the larger SSP Program under the guidance of the SSP Product Owner
- Close work with all levels in the organization that would comprise the team, and work across any potential process
- Direct accountability to the Product for the projects and deliverables assigned that fall within the Product Owner’s areas of responsibility
- Assess performance after each project and discuss feedback with the manager
- Coach and mentor team members and associates on how to apply and use improvement tools
- Deploy the Industrial business system, including the associated tiered accountability meetings at the SV level and the next 2 levels, to drive business strategy execution
- Support the development of the Electrical SV foundational BU process for business excellence (not inclusive of manufacturing processes)
- Lead capability development across all SV functional areas to drive operational excellence and a continuous improvement foundation
- Deploy proven problem-solving tools and methods widely across the organization
- Partner with senior leaders to champion a continuous improvement mindset and culture in the organization
Skills on Resume:
- Project Execution (Hard Skills)
- Cross-Functional Collaboration (Soft Skills)
- Deliverable Management (Hard Skills)
- Performance Assessment (Hard Skills)
- Team Coaching (Soft Skills)
- System Deployment (Hard Skills)
- Capability Building (Soft Skills)
- Culture Championing (Soft Skills)
40. Continuous Improvement Manager, Cascade Composite Materials, Bend, OR
Job Summary:
- Manage CI activities and drive culture by cultivating the use of CI strategies and tools
- Work with departments to establish CI objectives that align with strategic goals
- Lead and establish priorities for CI personnel
- Create, Evaluate, Communicate and share best practices
- Apply statistical principles to evaluate and improve processes
- Build and lead cross-functional process improvement teams
- Meet deadlines and manage multiple projects
- Work well in teams and make daily decisions with minimal guidance
- Effectively lead others and maintain the trust and cooperation of others
Skills on Resume:
- CI Strategy (Hard Skills)
- Goal Alignment (Hard Skills)
- Team Leadership (Soft Skills)
- Best Practice Sharing (Soft Skills)
- Statistical Analysis (Hard Skills)
- Process Improvement (Hard Skills)
- Project Management (Hard Skills)
- Decision Making (Soft Skills)
41. Continuous Improvement Manager, Allied Motion Parts, Evansville, IN
Job Summary:
- Establish a continuous improvement culture through the deployment of network operating systems coupled with a strong customer-focused strategy
- Drive operational excellence by leading large-scale transformations, including analytical assessment and definition
- Identify short-, mid-, and long-term opportunities that will transform the culture and produce results
- Understanding and aligning with the network's continuous improvement strategy and goals
- Leading a cross-functional team in the development of a standard problem-solving framework (systems, processes, tools, behaviors)
- Collaborating with others to ensure applicability and effectiveness across multiple functional areas
- Building a problem-solving practices road map with standard assessments and criteria
- Partnering with internal training resources to develop learning pathways, certification criteria and process, and training materials
- Deploying the problem-solving framework and process throughout the organization, including on-site problem-solving kaizen events to build capability
- Continually improving systems, processes, and tools
- Align specific and critical metrics that drive operational efficiency and improve customer experience
Skills on Resume:
- CI Culture (Soft Skills)
- Operational Excellence (Hard Skills)
- Opportunity Identification (Hard Skills)
- Framework Development (Hard Skills)
- Cross-Functional Collaboration (Soft Skills)
- Training Design (Hard Skills)
- Kaizen Deployment (Hard Skills)
- Metric Alignment (Hard Skills)
42. Continuous Improvement Manager, Copper State Tooling, Mesa, AZ
Job Summary:
- Analyse financial and performance reports to identify, recommend and implement methods to reduce waste, inefficiencies and non-value added activities
- Analyse and understand principles of operations for processing and packaging system (process/equipment/methods) capabilities to identify, develop, and execute improvement opportunities
- Coach and lead others to execute problem-solving using lean methodologies
- Lead and facilitate Root Cause Analysis (RCA), SIPOC, and DMAIC problem-solving projects
- Own the LSS project agenda with regular project reviews for progress vs productivity tasks and ensure that corrective A3s are on track and reviewed through the weekly QCDM format
- Develop long-range plans, goals and strategies to ensure the MOH productivity of the site
- Responsible for IPS, Standard Settings and top losses for the assigned area
- Identifying opportunities and working with production teams and site teams to resolve issues using Focused Improvement Tools
- Seeking/using best practice within PepsiCo, by owning the Starfleet agenda for the site
- Developing PIE pipeline talent
Skills on Resume:
- Waste Reduction (Hard Skills)
- Process Analysis (Hard Skills)
- Lean Coaching (Soft Skills)
- Problem Solving (Hard Skills)
- Project Oversight (Hard Skills)
- Strategic Planning (Hard Skills)
- Loss Identification (Hard Skills)
- Talent Development (Soft Skills)
43. Continuous Improvement Manager, Prairie Wind Components, Lincoln, NE
Job Summary:
- Identify and prioritize improvement projects and Kaizen activities
- Develop implementation plans and ensure execution of these plans
- Lead and implement assigned DPP projects and Kaizen activities
- Ensure sustainability and continue improvements of previous projects and continue the same trend in all shops
- Provide training to the organization on Lean Culture
- Support increasing productivity in all areas
- Support and drive the improvement of a specific project according to the growth of the business
- Deploy and ensure compliance with the lean culture within production areas
- Responsible for savings projects and eliminating waste throughout the production cycle
Skills on Resume:
- Project Prioritization (Hard Skills)
- Implementation Planning (Hard Skills)
- Kaizen Leadership (Hard Skills)
- Sustainability Focus (Soft Skills)
- Lean Training (Hard Skills)
- Productivity Support (Hard Skills)
- Business Growth Alignment (Soft Skills)
- Waste Elimination (Hard Skills)
44. Continuous Improvement Manager, Redwood Valley Automation, Redding, CA
Job Summary:
- Lead/support the lean production deployment
- Involved/take part in the standardization of the manufacturing process and management process
- Design or delegate equipment and tooling layout, configuration and specifications
- Initiate the request for the purchase of replacement parts and tooling
- Receive and inspect the incoming equipment, tooling and spare parts
- Study, support and initiate the continuous improvement projects regarding the efficiency improvement, wastage reduction and so on
- Take part in problem-solving including manufacturing process, quality, plant layout and overall supply chain
- Deliver intensive guidance and training to project members, I/E and managers for mastering and implementing lean knowledge
- Lead manufacturing cost improvement projects and be responsible for the results
Skills on Resume:
- Lean Deployment (Hard Skills)
- Process Standardization (Hard Skills)
- Tooling Design (Hard Skills)
- Equipment Inspection (Hard Skills)
- Efficiency Improvement (Hard Skills)
- Problem Solving (Hard Skills)
- Lean Training (Soft Skills)
- Cost Reduction (Hard Skills)
45. Continuous Improvement Manager, Apex Mold & Plastics, Waterloo, IA
Job Summary:
- Support the management team to define local KPIs and ensure performance management cycles/tools are in place and followed across the company operations
- Implement and sustain continuous improvement initiatives and activities across the area
- Act as a change agent to develop and implement a systematic approach to continuous and sustainable improvement
- Lead workshops, training, meetings, and events with site teams to promote/execute standardisation and CI, and bridge gaps between expectations and reality
- Together with the local sites leadership team, analyse the ‘as is’ in terms of customer satisfaction, process standardisation and execution, functional organisation, wastes and inefficiencies, etc
- Identify current processes and/or gaps and propose solutions to improve outcomes
- Coordinate and review all functional excellence activities in area and develop change management strategies to ensure the successful implementation and adoption of changes
- Sustain CI deployment and maturity in the site’s teams in coordination with product owners
- Act as a true ambassador for CI and articulate the advantages and how to deliver a better service to customers at a lower cost
Skills on Resume:
- KPI Management (Hard Skills)
- CI Implementation (Hard Skills)
- Change Leadership (Soft Skills)
- Workshop Facilitation (Soft Skills)
- Process Analysis (Hard Skills)
- Solution Development (Hard Skills)
- Change Strategy (Soft Skills)
- CI Advocacy (Soft Skills)
46. Continuous Improvement Manager, Flint River Operations, Macon, GA
Job Summary:
- Active participation in the Supply Chain Control Tower Strategic Initiative, leading business cases definition and reviews for simulations and control tower pilot
- Drive continuous improvement initiatives across the value chain and on terminals
- Develop and apply the scope of loss elimination workshops for SCO key sites
- Lead on-site Root Cause Problem Solve sessions and upskill local teams
- Contribute to the Operational Excellence program for Operations Europe by actively leading the Continuous Improvement Networks currently in place at SCO
- Participate in the Yara Productivity System forums as the SCO representative
- Build continuous improvement capability across SCO in Europe through formal training, hands-on coaching and utilization of skill matrices
- Implement and track the evolution of lean manufacturing self-assessment / develop specific improvement plans with key stakeholders
- Promote the development and implementation of a performance management system on the terminals
Skills on Resume:
- Strategic Leadership (Soft Skills)
- Value Chain Improvement (Hard Skills)
- Loss Elimination (Hard Skills)
- Root Cause Analysis (Hard Skills)
- CI Network Leadership (Soft Skills)
- Capability Building (Soft Skills)
- Lean Assessment (Hard Skills)
- Performance Management (Hard Skills)
47. Continuous Improvement Manager, Northern Light Manufacturing, Bismarck, ND
Job Summary:
- Responsible for ensuring compliance with Health and Safety regulations as laid down in company procedures and Government legislation and integrating these into CI working methods
- Developing effective working relationships across all areas of the business
- Effectively managing and deploying process improvement projects based on CI principles to achieve quantified results in line with FY targets
- Create resource project plans, delivering commitments on time and updating key stakeholders on the project status
- Completion of all relevant documentation and compliance with all Business Transformation governance processes
- Develop and sustain the deployment method that progresses improvements from pilot to full rollout
- Creation of appropriate documentation in the approved format to support the deployment and sustainment of individual projects into BAU
- Engagement of the Retail Communication team in a timely fashion on all project work streams
- Supporting the physical design and implementation phases of CI projects and purchasing materials, equipment and visual systems involved with prototype development
- Influencing key stakeholders including Retail, H&S, PP and L&D, to integrate improvements into BAU and include relevant compliance tools
- Accountable for facilitating listening groups to identify opportunities for further improvements and build and maintain the project's hopper
- Carry out any other reasonable tasks from time to time by the Retail Change Manager, Exec and Business sponsors
- Identifying and acting upon opportunities to promote and develop the Retail Change brand to strengthen CI awareness and capability
- Support Area Managers to ensure their stores are working to standard as requested by the Divisional Director
Skills on Resume:
- Safety Compliance (Hard Skills)
- Cross-Functional Relations (Soft Skills)
- CI Project Management (Hard Skills)
- Resource Planning (Hard Skills)
- Governance Adherence (Hard Skills)
- Deployment Sustainment (Hard Skills)
- Stakeholder Influence (Soft Skills)
- Standards Support (Hard Skills)
48. Continuous Improvement Manager, Mesa Verde Industrial, Farmington, NM
Job Summary:
- Positive leadership and motivation of a CI team- including development of clear goals and development plans
- Manage CI plans and activities for the business and oversee their implementation
- Manage the CI budget and minimize costs to ensure the total Operational budget is achieved
- Build trusted business relationships by providing CI advice to all departments
- Liaise with global CI teams across Kraft Heinz as well as external networks to ensure the delivery of best practice initiatives
- Manage projects to ensure all projects meet objectives and agreed timelines and budgetary requirements
- Driving a continuous improvement culture through identifying, organising and implementing improvement projects/programmes across the organisation
- Ensuring business impact and value realisation in a growing and fast-changing environment, focusing on people, processes and systems
- Inspiring, advising, coaching and training management and stakeholders on approach, methodologies and responsibilities
- Reporting project status through the existing Agile Improvement Portfolio, working closely with the Portfolio Manager to ensure its success and identifying and implementing improvements to this way of working
Skills on Resume:
- Team Leadership (Soft Skills)
- CI Planning (Hard Skills)
- Budget Management (Hard Skills)
- Relationship Building (Soft Skills)
- Best Practice Sharing (Soft Skills)
- Project Oversight (Hard Skills)
- CI Culture Promotion (Soft Skills)
- Agile Reporting (Hard Skills)
49. Continuous Improvement Manager, Bluegrass Tech Works, Bowling Green, KY
Job Summary:
- Working within a team of Business Improvement specialists, accountable for discovering opportunities, defining the best route to realise benefits and then delivering those initiatives and the benefits into life
- Lead cross-functional, cross-P&L initiatives or more complex initiatives
- Working closely with Project Managers to determine roadmaps, helping ensure prioritisation and help drive continuous and incremental improvement
- Operate across business functions to engage stakeholders, teams and colleagues to ensure effective collaboration and engagement throughout the product development lifecycle
- Mapping journeys end-to-end to document the status quo, whilst also identifying opportunities for improvement across systems, people and processes
- Own the creation and management of epics, features, user stories and acceptance criteria (through relevant development software tools)
- Create end to end process maps and user flows to help define/articulate customer journey and operational processes, identifying opportunities to streamline/lean/build right first time
- Use data and analytics to help inform decisions and ensure an adequate rationale is in place for all requirements
- Take a hands-on approach to product testing/QA, working closely with business stakeholders, quality assurance and the scrum team
Skills on Resume:
- Opportunity Discovery (Hard Skills)
- Cross-Functional Leadership (Soft Skills)
- Roadmap Planning (Hard Skills)
- Stakeholder Engagement (Soft Skills)
- Journey Mapping (Hard Skills)
- User Story Creation (Hard Skills)
- Process Optimization (Hard Skills)
- Data-Driven Decisions (Hard Skills)
50. Continuous Improvement Manager, Legacy Industrial Group, Columbia, SC
Job Summary:
- Develop and implement a robust training program to address operating procedures in the process areas
- Train new colleagues on ADM programs and site rules
- Display a commitment to lead, participate in, and support ongoing safety engagement
- Serve as the site implementation leader and subject matter expert for PE across the complex
- Actively lead and coach the site steering team and pillar teams
- Examine a variety of losses (safety, quality, production, cost) and apply PE methods to correct and sustain their improvement
- Work closely with the Plant Manager to translate the PE vision into tactical deployment plans that deliver sustained results
- Provide tools, resources, and training to department teams as they incorporate PE methods into their standard work
- Serve as a trusted resource for plant and department leaders using PE methods for continuous improvement and sustained results
- Responsible for driving health score improvements and increasing PE impacts (revenue generation and savings) at the complex
- Conduct regular touchpoints with PE practitioners to ensure that teams are staying true to the PE process
- Maintain the PE Wave Initiative to capture and record PE savings for the complex
- Follow key Wave Initiatives and escalate/intervene to offer support and resources if efforts fall behind schedule
- Maintain the PE Hopper as the single source of truth for plant priorities and work closely with various COEs to ensure that company priorities are being taken into account
- Pursues continuing education on PE methods and makes the same opportunities available to other leaders, colleagues, and pillar teams
- Assist the Plant Manager with mentoring and developing Shift Leaders, Department Superintendents, and Process Engineers to adopt a Continuous Improvement mindset
- Provide coverage for the Plant Manager and Department Superintendents
Skills on Resume:
- Training Development (Hard Skills)
- Safety Leadership (Soft Skills)
- PE Implementation (Hard Skills)
- Coaching Teams (Soft Skills)
- Loss Analysis (Hard Skills)
- Tactical Deployment (Hard Skills)
- Priority Management (Hard Skills)
- Leadership Mentoring (Soft Skills)
51. Continuous Improvement Manager, Everline Assembly Services, Lafayette, LA
Job Summary:
- Lead Continuous Improvement activities within the ABB E-Mobility organization
- Deliver on key performance indicators for the business, cost savings and optimizing transactional processes
- Prepare, mentor and review Continuous Improvement projects
- Direct and control all work performed within the project framework of the DMAIC phases
- Responsible for daily communications and formal project reviews with both the project sponsor and stakeholders
- Develop strategies for process improvement across customer services, supply chain, purchasing and manufacturing
- Analyse data to identify trends and recommend process /business improvement opportunities
- Manage initiatives/projects to drive continuous improvement in Customer Experience across regions
- Planning and implementing continuous improvement projects
- Monitor the volume of contacts at the interval level, activity codes, overall onsite/offsite shrinkage, variations in AHT, and any other real-time events that contribute or impact negatively in the execution of planned productivity hours to meet SLAs
- Co-plan with Ops to create and optimize the schedule, following region-specific labor laws
- Constant interaction with Operations on-site performance, including staffing compliance, skilling status, and outages
- Provide visibility and reporting capabilities of main SLAs and KPIs related to intraday and scheduling functions such as adherence, shrinkage components, and projected interval compliance
Skills on Resume:
- CI Leadership (Soft Skills)
- KPI Delivery (Hard Skills)
- Project Mentoring (Soft Skills)
- DMAIC Execution (Hard Skills)
- Stakeholder Communication (Soft Skills)
- Process Strategy (Hard Skills)
- Data Analysis (Hard Skills)
- Scheduling Optimization (Hard Skills)
52. Continuous Improvement Manager, Cedar Lake Systems, Eau Claire, WI
Job Summary:
- Responsible for the assessments of processes about implementation, quality, and target achievement (SLA)
- Responsible for the definition of process improvements and the implementation in cooperation with internal/external stakeholders and in cooperation with an external supplier
- Reviewing the effectiveness of quality improvement measures and initiating quality assurance measures
- Developing an audit plan and its implementation under global and regional aspects as well as in close cooperation with global teams
- Managing and monitoring Ofsted EIF inspection to Grade 2 and above
- Implementing quality improvement processes and procedures, and monitoring compliance to ensure a positive impact
- Co-ordinating, reviewing and monitoring the annual Self-Assessment Report and quarterly position statements in liaison with the Head of Royal Navy Apprenticeships, Apprenticeship Operations Manager, and the Head of Quality Improvement and New Projects
- Overseeing Apprentice Voice processes and surveys are being delivered and analyzed for continuous improvement requirements
- Liaising with the Teaching and Learning observations team to monitor the quality of teaching being delivered, meeting with the expected standards
- Preparing reports for internal stakeholders on quality monitoring results, analysis, and trends to inform risk mitigation
Skills on Resume:
- Process Assessment (Hard Skills)
- Improvement Implementation (Hard Skills)
- Quality Assurance (Hard Skills)
- Audit Planning (Hard Skills)
- Compliance Monitoring (Hard Skills)
- Stakeholder Reporting (Soft Skills)
- Survey Analysis (Hard Skills)
- Teaching Quality Review (Hard Skills)
53. Continuous Improvement Manager, Union Hill Fabrication, Roanoke, VA
Job Summary:
- Work with the CI committee to build up and develop a Continuous Improvement culture
- Work with functional heads to make sure sustainable 5S principles are ingrained in the culture everywhere
- Share improvements across the organization in a structured way to stimulate kaizen
- Schedule and facilitate Kaizen Workshop plan across the year and prepare the plan to make sure that employees are trained to know the difference between Kaizen and problem solving
- Facilitate the team to identify and eliminate of all forms of waste, variation and overburden based on Value Stream Mapping and strategy
- Step change projects are strategically executed to both improve KPIs and improve local CI capability
- Continuously optimize process confirmation to ensure fulfillment of agreed standards
- Continuously improve Visual Management to support maintaining the standard, setting priorities and providing transparency to roles and responsibilities
- Continuously improve the escalation procedure across all functions, to ensure a clear response to escalations from all levels
Skills on Resume:
- CI Culture Development (Soft Skills)
- 5S Integration (Hard Skills)
- Kaizen Facilitation (Hard Skills)
- Waste Elimination (Hard Skills)
- Strategic Execution (Hard Skills)
- Process Confirmation (Hard Skills)
- Visual Management (Hard Skills)
- Escalation Management (Soft Skills)
54. Continuous Improvement Manager, Gulfstream Parts & Supply, Pensacola, FL
Job Summary:
- Act as a liaison between Technology Operations and business units to increase transparency and awareness of the services provided by Global IT
- Managing and building relationships with key stakeholders, managing escalations and queries, and keeping the customer updated until resolved
- Conducting Service Reviews, reporting KPI’s and other metrics to business unit stakeholders and gathering feedback
- Identifying areas for continuous and sustainable improvement in the quality and efficiency of services, and working with the wider teams to implement these initiatives
- Creating and improving global processes and procedures to ensure a consistent service, including the Global IT work intake process and demand management for IT project requests
- Assist with projects and compliance initiatives to drive a better customer experience
- Tracks, validates, and analyzes initiatives in assigned areas
- Supports strategic planning, implementation, and analysis of projects through meetings with partners and area leaders
- Drives personal projects to successful implementation
- Works with area leaders to establish and execute a strategy for meeting the annual PIC goal
- Acts as a subject matter expert on the PIC process
- Fosters and enables a continuous improvement culture across the company through active engagement of associates in process improvement initiative identification and implementation
Skills on Resume:
- Stakeholder Management (Soft Skills)
- Service Transparency (Soft Skills)
- KPI Reporting (Hard Skills)
- Service Improvement (Hard Skills)
- Process Development (Hard Skills)
- Project Support (Hard Skills)
- Strategy Execution (Hard Skills)
- CI Culture Engagement (Soft Skills)
55. Continuous Improvement Manager, Snowcap Manufacturing LLC, Bozeman, MT
Job Summary:
- Lead end-to-end process improvement and effect complex and sensitive productivity improvement initiatives within a well-developed management of change framework
- Responsible for business case development and undertaking business efficiency reviews with the view to embedding a leadership culture that strives to achieve excellence in team culture aligned with V/Lines' code of conduct
- Review, design, and implement a comprehensive Modernisation strategy
- Utilise strategic and analytical information, stakeholder feedback, current trends, industry best practice and emerging developments
- Assist the Train Services team in achieving its Operational and Safety objectives through the delivery of its operational strategy
- Work with the member services leadership team to deliver business improvement initiatives
- Manage multiple simultaneous projects requiring frequent communication, organisation/time management and problem-solving skills
- Work with the Op Ex coaches in supporting the quarterly Operational Excellence capability reviews, identifying areas for improvement, resulting in departmental improvement plans
- Be the "Voice of the Customer" when assessing the effectiveness of processes and operational procedures
- Support the development of a process governance framework for the business, ensuring that roles and accountabilities are clearly understood
Skills on Resume:
- Process Improvement (Hard Skills)
- Business Case Development (Hard Skills)
- Strategy Implementation (Hard Skills)
- Stakeholder Insight (Soft Skills)
- Operational Support (Hard Skills)
- Project Management (Hard Skills)
- Customer Advocacy (Soft Skills)
- Governance Framework (Hard Skills)
56. Continuous Improvement Manager, Pioneer Precision Systems, Grand Junction, CO
Job Summary:
- Communicates customer, regulatory and organizational requirements to assure product quality, contract compliance and customer satisfaction
- Implements the performance measurements necessary to effectively evaluate organizational performance and trends in product quality, services, customer satisfaction and the cost of poor quality
- Uses the results of performance evaluation to target improvement efforts
- Collaborates with Purchasing on the development and implementation of a supplier management strategy
- Assess supplier capabilities and monitor supplier quality to ensure desired levels of performance
- Collaborates with Engineering on new product development and design review for quality/reliability issues
- Oversees the Advanced Product Quality Planning (APQP) process
- Develops a Lean Strategy to be implemented Division-wide
- Guides Lean initiatives within the Division
- Ensures the Division is implementing the company's Lean System, the principles, techniques, and methodologies
- Ensures ongoing education of all employees in the Division
- Promotes a continuous learning environment
Skills on Resume:
- Quality Compliance (Hard Skills)
- Performance Evaluation (Hard Skills)
- Improvement Targeting (Hard Skills)
- Supplier Management (Hard Skills)
- Product Development Support (Hard Skills)
- Lean Strategy (Hard Skills)
- Employee Training (Soft Skills)
- Continuous Learning (Soft Skills)
57. Continuous Improvement Manager, Freedom Valley Technologies, Scranton, PA
Job Summary:
- Ensures establishment and maintenance of excellent relationships with provider organizations
- Leads activities related to outreach and serves as liaison to provider organizations and physician practices for assigned programs
- Assures compliance with established quality program standards
- Coaches practice in the collection and management of relevant program data
- Analyzes trends regarding practice performance to inform coaching plans and opportunities for shared learning events
- Prepares and submits various reports to management
- Works with other relevant provider organizations and statewide groups, as applicable, to coordinate and align quality improvement efforts
- Plans detailed special projects and leads project planning teams and workgroups using various continuous QI tools and methodologies
- Recommends courses of action to management in the development and completion of special projects requiring quality and process improvement skills
- Supports integration with other related initiatives
- Identifies and facilitates opportunities to integrate the project with other QI initiatives
- Develops and disseminates relevant project materials, communications, surveys, etc.
Skills on Resume:
- Provider Relations (Soft Skills)
- Outreach Leadership (Soft Skills)
- Quality Compliance (Hard Skills)
- Data Coaching (Soft Skills)
- Performance Analysis (Hard Skills)
- Project Planning (Hard Skills)
- QI Integration (Soft Skills)
- Material Development (Hard Skills)
58. Continuous Improvement Manager, Horizon Flow Engineering, Charleston, WV
Job Summary:
- Provides direct practice facilitation and QI coaching to practice teams, ongoing training, consultation and monitoring to facilitate practice redesign and/or other QI improvements for designated practices
- Provides support to existing practice coaches where those exist, with the ultimate goal of developing QI capacity of the practice team to make improvements in practice operations and/or clinical quality
- Develops relationships and works with consumer organizations
- Identifies and shares best practices through webinars, website and/or QI learning sessions
- Stays abreast of new developments and industry trends related to best practices in clinical QI and practice transformation
- Creates educational materials (webinars, brochures, etc.) for providers and conducts provider training
- Makes presentations to individuals and groups as indicated
- Ensures appropriate communication with key stakeholders
- Works with health program staff to create and update web-based communications and information
- Contributes to health programs and project communications
Skills on Resume:
- Practice Coaching (Soft Skills)
- Capacity Building (Soft Skills)
- Stakeholder Engagement (Soft Skills)
- Best Practice Sharing (Hard Skills)
- Trend Awareness (Hard Skills)
- Educational Development (Hard Skills)
- Public Speaking (Soft Skills)
- Health Communication (Hard Skills)
59. Continuous Improvement Manager, Red River Processing, Shreveport, LA
Job Summary:
- Coordinate selected cross-departmental initiatives that may affect ALK Madrid production site, ensuring the execution of those on time and on budget, and with the quality
- Identify, define and execute initiatives that will improve compliance, efficiencies, yields or throughputs
- Coordinate the Operational Excellence initiatives for the ALK production site in Madrid
- Directly leading initiatives or supporting main departments on the identification, definition and execution of them
- Work closely with the main production site areas to troubleshoot processing problems and develop solutions that support business objectives and overall production strategy
- Support departments in establishing, reporting and improving key metrics (KPIs)
- Lead local roll-out of company methodology, processes, tools, templates and training related to Operational Excellence
- Promote spreading the Operational Excellence mindset at the ALK production site in Madrid
- Provide support to benchmarking that enables head-to-head productivity comparison between production sites in ALK and peers outside ALK
- Actively participate in the Global Operational Excellence network
Skills on Resume:
- Cross-Department Coordination (Soft Skills)
- Initiative Execution (Hard Skills)
- Operational Excellence (Hard Skills)
- Process Troubleshooting (Hard Skills)
- KPI Improvement (Hard Skills)
- Methodology Deployment (Hard Skills)
- Benchmarking Support (Hard Skills)
- Global Collaboration (Soft Skills)