WHAT DOES AN INVENTORY MANAGER DO?
Published: Jun 25, 2025 - The Inventory Manager oversees formal inventory procedures, conducts cycle counts, and generates reports to ensure accuracy and operational transparency. This role drives process improvement initiatives, audits compliance, and manages both salaried and hourly team performance to maintain effective inventory control systems. The manager also collaborates with senior leadership on financial reporting, payroll, and vendor management while ensuring compliance with safety and regulatory standards.
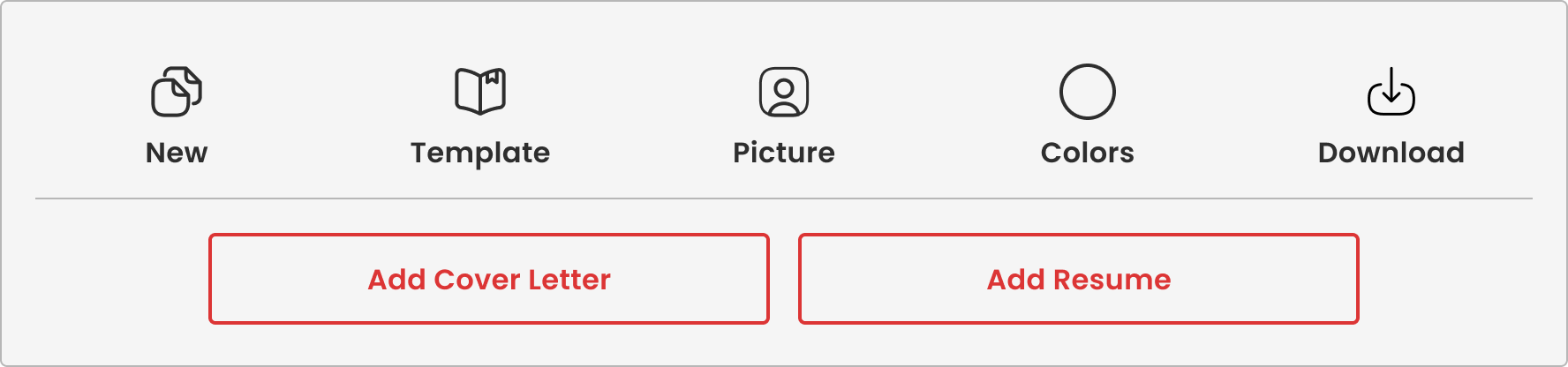

A Review of Professional Skills and Functions for Inventory Manager
1. Inventory Manager Duties
- Business Judgment: Exercise good business judgment independently while performing essential functions
- Inventory Analysis: Ensure inventory is accurate in the system through thorough analysis
- Cycle Counting: Oversee and conduct Cycle Count inventory processes to ensure accuracy and timely execution
- Count Scheduling: Schedule finished goods inventory cycle counts while maintaining strict records
- Team Development: Develop a successful Inventory team to ensure success for the department and team members
- ERP Management: Maintain ERP inventory records by entering journal entries based on the Cycle Count results
- Label Accuracy: Support the warehouse team to ensure the correct labeling of all products/materials
- Material Oversight: Oversee and evaluate raw material requisition procedures
- Inventory Metrics: Maintain a set of metrics related to inventory management accuracy
- Record Evaluation: Maintain and evaluate inventory records every quarter
- Receiving Audit: Audit and evaluate the receiving accuracy of all raw material receipts to ensure, among other things, compliance with traceability requirements
- Shortage Notification: Notify purchasing of shortages or other problems that could impact product availability
- Procedure Instruction: Instruct warehouse staff on proper procedures for locating and utilizing product inventory
- Salvage Management: Manage and monitor the inventory salvage process
- Task Management: Manage multiple tasks simultaneously and handle adverse and urgent situations with rapid changes in priorities
2. Inventory Manager Details
- Inventory Management: Responsible for managing the total North America Shave Grooming inventories totaling approximately $100M USD
- Metric Delivery: Drive and deliver key metrics such as inventory projections, DIIs, OTIF
- Process Optimization: Implement process improvements to optimize inventory position
- Plant Coordination: Coordinate with up to six internal Global plants that make up a complex network in supplying Finished and WIP items for the market
- Supplier Alignment: Ensure third-party suppliers to ensure inventory levels are in line with projections
- Forecast Management: Forecast North America inventory projections to meet the business needs, as well as meet the DII goals
- SLOB Oversight: Manage the Shave Finished Good Slobs and provide support to the Supply Planning teams on RAW/WIP Slobs for disposition
- SOP Communication: Provide a monthly focus on Regional S&OP (as a communication channel)
- Projection Ownership: Be the presenter/owner of any meeting that requires inventory projections such as operational pre-plan / financial inventory projections etc
- Business Planning: Provide support and help manage the Operational Annual Business Planning process
3. Inventory Manager Responsibilities
- Safety Stock: Implement the Statistical Safety Stock process for the North America region in order to maintain DII and OTIF goals for the Shave business
- Gap Analysis: Provide root cause analysis to inventory gaps along with mitigation plans and strategies to correct gaps in order to stay on plan
- Launch Oversight: Provide lead coordination on product restage transitions and oversight on new product launches
- Inventory Optimization: Manage any product prebuilds and capacity in order to drive overall inventory optimization
- Order Fulfillment: Achieve OTIF customer service order fulfillment objectives while maintaining inventory levels at days in inventory (DII) goals
- Plan Coordination: Work with Demand Planning, Finance and Operations on the annual business plan (ABP) in terms of annual plant volume and inventory investment projections
- SKU Management: Collaborate with Brand Managers on SKU Segmentation and Rationalization efforts to effectively manage SKU portfolios
- Financial Planning: Provide support to the North America Supply Chain team during the Annual Financial Planning process
4. Inventory Manager Job Summary
- Inventory Control: Create, establish and evolve the inventory management and control function
- Best Practice: Ensure best practice within all site inventory teams
- SOP Alignment: Through the implementation of new ways of working in line with robust SOPs
- Stock Accuracy: Develop routines and procedures that contribute to maintaining accurate stock files
- Root Analysis: Undertake Root cause and trend analysis, then proactively educate the inventory and operational teams on issues that arise, which could have been solved at source
- Inventory Audits: Conduct detailed audits of all inventory functions across the network
- Team Leadership: Line management of the inventory teams and Inventory Controllers across the laboratory network
- Performance Management: Actively manage their activity and also their development, which includes being responsible for performance reviews, coaching and development, leading a high-performing team and supporting succession plans
- Discrepancy Resolution: Investigate and reconcile significant stock discrepancies
- Stock Adjustment: Adjusting stock records and reporting on route causes
- Physical Checks: Manage, control and undertake physical stock checks
- Waste Control: Pin-point current areas of stock wastage, excess usage, loss and implement control measures
- Count Process: Develop and implement a robust Count process across the network under a single methodology
- Annual Counts: Plan, attend and oversee annual stock counts in all locations to ensure completion to a satisfactory standard
- Obsolete Stock: Identify, manage, coordinate and minimize the occurrence of aged and obsolete stock
- Receipting Process: Develop and oversee the delivery and receipting process to minimize delays and internal discrepancies
- Warehouse Setup: Maintenance and upkeep of warehouse details for new and existing lines to maximize efficiency of travel and storage in the warehouses
- Demand Planning: Build and embed demand and supply planning processes to ensure stock availability and flexibility
- Warehouse Profiling: Ongoing warehouse profiling and involvement in new warehouse layout design to maximize usage and convenience for site users
- Inventory Reporting: Produce both regular and ad hoc reports relating to inventory levels and accuracy
- Findings Presentation: Presenting findings to senior management and colleagues at all levels of the business
- Packaging Issues: Identify packaging issues and actively build relationships with the stock control and purchasing teams
- ERP Limitations: Understand current ERP limitations and contribute towards implementing new systems
- Quality Contact: Act as the first contact point for all quality-related matters within the Business Unit and follow up with the QA department for a prompt resolution
- Team Education: Proactively educate the inventory and operational teams on arising issues
- Team Support: Support the wider management team in creating a great place to work
- Continuous Improvement: Facilitating effective communication, promoting best practice, helping develop a culture of continuous improvement, plus contributing to and supporting plans as they evolve and grow the business
5. Inventory Manager Accountabilities
- Policy Management: Write and/or update all inventory management policies, processes and procedures
- Team Supervision: Manage an inventory analyst
- Inventory Oversight: Manage inventory through the Ziosk Enterprise, including equipment in offices and deployed in the field
- Inventory Reporting: Prepare detailed reports on inventory operations, stock levels and forecasts
- Order Submission: Submit orders for new inventory
- Deployment Planning: Participate in regular inventory and implementation meetings to provide forecasts and understand upcoming deployments
- Asset Tracking: Partner with the Service Center and IT teams to track all company assets and validate that processes are being followed
- Team Collaboration: Collaborate with Service Center employees to ensure all business goals are met
- Supply Planning: Partner with the Supply Chain and Service Center teams to plan new equipment arrival, storage and deployments
- Vendor Management: Own 3rd party relationships for external storage, device disposal
- Budget Forecasting: Provide a budget forecast for all 3rd party services and inventory purchases
- Solution Evaluation: Evaluate new inventory solutions and work with the CIO on product selection
6. Inventory Manager Functions
- Asset Deployment: Manage and deploy on-street assets (bike stations)
- Spare Management: Manage workshop spares (bike parts)
- Fleet Oversight: Manage a small vehicle fleet
- Stock Auditing: Regular stock-takes and alignment
- Contractor Supervision: Managing contractors performing on street installations
- KPI Delivery: Own and deliver against KPI's for the operations and supply chain
- Stock Maintenance: Making sure the stock levels are maintained
- System Development: Help to develop stock management systems
- Team Liaison: Liaise and communicate with the wider Serco supply chain team and suppliers
- Process Improvement: Seek to continually improve processes and identify areas of potential weaknesses
- Team Motivation: Inspire the inventory team to care about customers, brand and products
7. Inventory Manager Job Description
- Inventory Strategy: Reporting to the VP of Operations and aligning with all departments to support strategic and business goals
- Cross-Team Collaboration: Build strategic partnerships with Sales and Logistics to optimize stock liquidation and manage overstock, end-of-season, and obsolete inventory
- Inventory Reporting: Provide regular and insightful stock reports and analyses for management, including ATS, ageing, and returns
- Process Alignment: Work with regional logistics managers to ensure timely, accurate inventory processes and manage warehouse counts and discrepancy investigations
- Partner Coordination: Maintain system accuracy based on warehouse stock, implement dashboards, and collaborate with 3PL partners and auditors for streamlined inventory operations
8. Inventory Manager Overview
- NetSuite Management: Maintain accurate inventory records using NetSuite and RF Smart systems
- Inventory Evaluation: Evaluate and monitor inventory levels of raw materials and finished goods
- Product Maintenance: Manage product setup and updates to ensure data accuracy
- Audit Execution: Organize and conduct semi-annual inventory audits for compliance and accuracy
- Cross-Department Coordination: Collaborate with department heads to uphold inventory count integrity
- Reporting Support: Assist the Tax Manager by preparing reports related to promotional and boxed product tracking
9. Inventory Manager Details and Accountabilities
- Vendor Management: Oversee hardware and software vendor relations, including process development and maintenance
- Demand Forecasting: Use SFDC reporting to forecast hardware and virtual appliance needs
- License Oversight: Manage Microsoft CLA renewals, VLSC portal administration, and license inventory purchasing
- Inventory Coordination: Collaborate with Accounting and Support teams to manage hardware and license inventory
- Approval Review: Evaluate and approve or escalate hardware/software swap requests
- Program Monitoring: Track open volume license and evaluation programs for accuracy
- Partner Relations: Maintain strong relationships with third-party partners and outsourcing companies
10. Inventory Manager Tasks
- Team Supervision: Supervise I/C associates to include staffing, training, coaching, performance management, and problem resolution
- Data Analysis: Interprets and analyzes numerical data and performs a basic level of inventory control analysis, handles stock adjustments
- Report Accuracy: Responsible for ensuring that the Daily Scratch Sheet is completed correctly and on time
- Inventory Management: Manages an acceptable level of inventory cost-effectively
- Vendor Communication: Communicates with vendors and company personnel positively and proactively
- System Accuracy: Responsible for ensuring that the product received is entered into the system correctly
- Issue Resolution: Analyzes inventory issues and information
- Problem Solving: Taking any necessary action to resolve
- Stock Monitoring: Maintaining surveillance of possible dead items, monitoring zero balance items/inventory high-dollar items
- Product Inspection: Manages the area to include reviewing checkouts, checking for outdated products, handling salvage products, checking inbound freight, monitoring slots for damaged products, checking slotting errors, and monitoring rotation
- Invoice Processing: Ensure all purchase orders and incoming internal invoices are accounted for, checked in and submitted correctly
- Report Preparation: Preparing and reconciling daily, weekly and monthly inventory and production reports
- Inventory Coordination: Coordinating and managing monthly/quarterly physical inventories and the development of follow-up reporting
- Procedure Compliance: Responsible for ensuring that all month-end, quarterly and year-end procedures for cigarettes and non-cigarette are followed and all deadlines are met
- Stock Counting: Responsible for actual inventory counts
- SOX Compliance: Meet all SOX compliance, processes, and procedures
11. Inventory Manager Roles
- Customer Support: Serves customers and internal teams as primary contact and source of information on inventory and inventory data requests
- System Setup: Ensure the accurate set-up of the client inventory system from receipt to fulfillment
- Discrepancy Resolution: Monitor and reconcile discrepancies and variations
- Report Generation: Generate reports for the customer and internal departments and distribute accordingly
- Client Coordination: Work closely with customers on inventory specifications
- Task Monitoring: Monitor and respond to internal task requests relating to data and inventory
- Data Accuracy: Work with the EOS Data Analytics team to ensure data integrity and accuracy on the service
- Dashboard Reporting: Accountability for accurate and timely dashboard reporting to the Operations Manager
- Asset Processing: Process internal asset changes and new build asset information on the Facebook system
- Tech Implementation: Participate in implementation meetings for new technologies and services
- Procedure Development: Develop and refresh inventory control operating procedures and train all staff accordingly
- Equipment Management: Manage and maintain all RFID Equipment, ensuring any defects are reported accordingly
12. Inventory Manager Additional Details
- Partner Management: Manage and expand relationships with current shipping partners FedEx, Purolator, UPS, and LTL brokers
- Risk Assessment: Identify risks and opportunities as shipping partners introduce new products and policies
- Performance Monitoring: Monitor partner shipping performance and work with them to resolve friction points
- Partner Integration: Drive the process of shipping partner selection and integration including evaluation, recommendation, cost analysis, negotiations, and launch
- Shipping Solutions: Identify and execute shipping solutions to support new category expansions (furniture, overweight items, etc.)
- Forecast Ownership: Develop a vision for inventory planning and own inventory forecasting for the eCommerce channel to support cross-functional stakeholders
- Carrier Communication: Communicate with carriers regarding timely customs clearance, invoicing, fees, etc., to ensure timely service and accurate billing
- Reporting Submission: Track information and submit reports to management and accounting
- Demand Analysis: Review historical data and current sales trends, research demand drivers, and evaluate forecast results
- Quota Planning: Manage the preseason planning and quota process, working with the Supply Chain Manager to develop department plans that support broader category/brand strategies
- Inventory Flow: Responsible for in-season inventory movement to ensure that eCommerce out-of-stocks are minimized
- Result Communication: Regularly communicate financial results, forecasts, and action plans to eCommerce leadership and cross-functional partners
- KPI Tracking: Maintain and report KPIs such as forecast accuracy, in-stocks/out-of-stocks, on-time delivery, etc.
- Shortage Resolution: Highlight shortages promptly with a resolution action plan
- Cross Collaboration: Develop and maintain strong relationships cross-functionally with Sales, Accounting, and Operations
- Team Supervision: Manage the Inventory Specialist who facilitates the movement of inventory through the fulfillment network
- Shipment Synchronization: Synchronize shipments with 3PLs to update inventory, verify invoices, and enter cost allocation in the JDE/ERP system
13. Inventory Manager Essential Functions
- Performance Monitoring: Maintains and improves operations by monitoring system performance, identifying and resolving challenges, completing process audits/analyses, and preparing and completing action plans
- Strategy Planning: Determines operational strategies by conducting needs assessments related to inventory storage, capacity needs, and receiving procedures
- Goal Setting: Establishes quotas and goals to ensure productivity and quality standards
- Staff Coaching: Places emphasis on coaching, motivating, and retaining staff
- Process Automation: Works toward converting manual processes to automated ones where reasonable and efficient
14. Inventory Manager Role Purpose
- Process Standardization: Ensure that effective and efficient inventory management, forecasting, and planning processes are implemented and standardized
- Inventory Analysis: Analyze and report on inventory and inventory changes month over month, per country
- Root Analysis: Conduct root cause analysis for inventory drivers and define countermeasures
- Forecast Management: Set inventory targets and manage ongoing monthly forecasts per country
- Inventory Optimization: Initiate initiatives to optimize inventory while maintaining SLAs
- Process Improvement: Drive continuous improvement and cost savings programs
- KPI Development: Develop and execute against business-critical KPIs and metrics
- Control Compliance: Ensure proper PO controls and inventory management standards are followed
- Team Development: Manage, develop, and train team members to ensure a strong, effective workforce
- Stakeholder Interface: Serve as the key interface between service, local, regional, and global inventory teams
- Legal Compliance: Comply with all local laws and regulations
15. Inventory Manager General Responsibilities
- Team Leadership: Lead a team of 5-10 people who receive, put away, and conduct inventory counts of supplies
- Vendor Management: Manage vendor relationships and place orders for supplies to ensure adequate stock on hand
- Stock Execution: Manage and execute the receiving and stocking of all medication
- Supply Coordination: Work closely with the medication purchasing team to communicate medication supply issues
- Material Testing: Work with the operations engineering team to test and roll out new materials
- Inventory Collaboration: Partner with the ICQA Manager on all inventory management issues
- Process Improvement: Lead special projects related to process improvement and inventory management
16. Inventory Manager Key Accountabilities
- Team Motivation: Cultivate and inspire the Inventory Team to take initiative and maintain an immaculate inventory system
- KPI Alignment: Set departmental KPIs that align with company values, ensuring all products can be stocked on time
- System Development: Develop, manage, and improve internal systems, including the use of a modern inventory management software
- Forecast Planning: Work with Operations and Finance teams to accurately complete product forecasting and planning and issue purchase orders
- Process Optimization: Create and iterate processes focused on improving efficiency, reducing waste, and heightening customer experience
- Variance Resolution: Investigate inventory discrepancies, conduct root cause analysis, and execute corrective actions for inventory variances
- Staff Development: Identify and act on growth and education opportunities for the Inventory team, ensuring each individual is set up for success
- Data Communication: Set up reporting and communication channels with other departments, allowing for seamless cross-departmental collaboration and transparency of information
17. Inventory Manager Roles and Details
- Team Oversight: Oversees team of inventory, purchasing and warehouse employees
- System Management: Manages inventory and purchasing system to monitor purchases, deliveries, shipments and stock levels
- Procedure Evaluation: Evaluates deliveries, shipments and product levels to improve inventory control procedures
- Supply Analysis: Analyzes daily product and supply levels to anticipate inventory problems and shortages
- Schedule Optimization: Manages schedules of employees, deliveries and shipments to optimize operations
- Staff Communication: Communicates with inventory employees to meet business goals and address personnel issues
- Relationship Development: Develops business relationships with suppliers and clients
- Cost Reduction: Proposes strategies to reduce costs and improve procedures of supply chain logistics
- Demand Forecasting: Monitors demand and analyzes data to anticipate future supply and logistical needs
- Progress Reporting: Reports on inventory levels, supply chain progress, procedural efficiency and personnel issues to upper management
- Employee Training: Manages the training of inventory employees
- Process Improvement: Ensures a proactive approach for all processes within the inventory, purchasing and warehouse departments
18. Inventory Manager Responsibilities and Key Tasks
- Change Management: Responsible for maintaining effectiveness when experiencing major changes with tasks and/or work environment
- Team Communication: Ensure communication is happening among all interested parties in regards to inventory movement and other items
- Access Control: Ensuring limited access to the premises inventory
- Threshold Monitoring: Monitor inventory thresholds and communicate these to Senior Management
- Inventory Protocols: Follow inventory protocols for inventory management (intake, organization, recording data, and distribution)
- Kit Preparation: Prepare inventory distribution kits according to specifications
19. Inventory Manager Duties and Roles
- Strategic Leadership: Accountable for large multi-departmental areas or locations with significant impact on business unit results and organizational strategy
- Team Management: Manages a team of senior-level exempt individual contributors and first-level managers that typically support a complex business unit
- Performance Oversight: Responsible for hiring, setting and monitoring of annual performance plans, coaching, and career development
- Process Enablement: Ensures that the proper tools are in place to support the team and the processes
- Operational Planning: Plans, directs and monitors high-end operational/tactical activities of the Staff
- Strategic Execution: Staff members' primary focus is on either high-end tactical or broad strategic issues or a combination of both
- Executive Consulting: Consults with business leaders to guide and influence strategic decision-making within a broad scope
- Advisory Expertise: Acts as a key advisor to senior management on the development of overall strategies and long-term goals of the organization
- Issue Resolution: Applies expert subject matter knowledge to manage staff activities in solving the most complex business/technical issues within established frameworks
- Global Initiatives: Oversees the development and delivery of complex initiatives that can impact the supply chain globally, typically requiring the leadership of cross-functional and/or cross-regional teams
20. Inventory Manager Roles and Responsibilities
- Inventory Compliance: Ensure the accuracy, timeliness, cost effectiveness and regulatory compliance in all inventory and distribution activities
- Reconciliation Leadership: Lead the monthly Inventory Reconciliation process to ensure appropriate inventory control
- Physical Coordination: Coordinate annual Physical Inventories with 3PL and Airtech inventory locations
- Data Analysis: Analyze data to establish the inventory and financial impact and make adjustments
- Industry Awareness: Stay abreast and understand industry trends that can improve Airtech processes and suggest improvements to operational efficiency
- Shipment Oversight: Ensure timely receipt, shipment, and invoicing of all raw materials and finished goods packaging materials stored at third-party manufacturers' and warehouse facilities
- Stock Planning: Ensure material plans and safety stock in the Distribution Centers support and align with the customer fulfillment strategies
- Problem Solving: Analyzes complex business problems and provides analytical and business process support that will be instrumental in the formation of distribution strategy, cost savings, and continuous improvement efforts
- Inventory Balancing: Balance inventory between distribution centers by identifying products to be transferred including SKUs, quantities, timing, and cost
- Performance Reporting: Report inventory value and turns performance and variance analysis to senior management
- Root Investigation: Perform root cause investigations of complex inventory discrepancies and suggest corrective actions
- Master Setup: Work with other supply chain departments and sales personnel to set up the correct SKU master data information in the ERP system
- Activity Reporting: Create and analyze monthly transactional reports to review 3PL activity and performance
- Trend Identification: Identify trends and work with peers to offer guidance in process and procedure improvements
- Launch Expertise: Subject matter expert in new country launch setup and 3PL transition and configuration for SKUs, inventory and distribution data
- Order Fulfillment: Ensure accurate and timely order fulfillment management by maintaining and processing backorders, item substitutions, order counts, delays, cancellations, etc.
- Process Development: Develop SOPs, process maps, and serve as a training partner for new members
- Process Expertise: Subject matter expert in all Inventory and Distribution processes
- Team Coaching: Provide leadership, coaching, and/or mentoring
- Partner Interface: Interface with global partners to ensure the smooth operation of the globalized inventory
- Project Support: Support special departmental project initiatives around cost reduction, process improvement, and new system enhancements
21. Inventory Manager Duties
- Supply Coordination: Collaborate with other WPS managers to determine supply needs
- Material Purchasing: Purchase supplies and materials according to specifications in coordination with the accountant
- Procedure Supervision: Coordinate and supervise receiving and warehousing procedures with the accountant, manager and the production manager
- Supply Distribution: Oversee the distribution of supplies in the organization
- Inventory Control: Control inventory levels and ensure the availability of materials during emergencies
- Staff Supervision: Supervise, evaluate and coach subordinates
- Supplier Relations: Maintain relationships and negotiate with suppliers
- Record Maintenance: Keep detailed records on procurement activity, materials quantity, specifications etc.
- Order Forecasting: Assist in forecasting to plan future orders
- Procedure Optimization: Devise ways to optimize inventory control procedures
- Level Inspection: Inspect the levels of business supplies and raw materials to identify shortages
- Stock Assurance: Ensure product stock is adequate for all distribution channels and can cover direct demand from customers
- Warehouse Organization: Ensure warehouse inventory is kept organized and properly labeled
- Cycle Counting: Perform cycle counts on a regular schedule and as needed by request of management
- Delivery Reconciliation: Record daily deliveries and shipments to reconcile inventory
- Order Processing: Issue, maintain, and close pick orders for inventory material/supplies to be used
- Demand Monitoring: Use software to monitor demand and document characteristics of inventory
- Stock Replenishment: Place orders to replenish stock, avoiding insufficiencies or excessive surplus, in coordination with the accountant
- Need Anticipation: Analyze data to anticipate future needs
- Supplier Evaluation: Evaluate suppliers to achieve cost-effective deals and maintain trust relationships
- Goal Collaboration: Collaborate with warehouse employees and other staff to ensure business goals are met
- Stock Reporting: Report to upper management on stock levels, issues etc.
- Meeting Attendance: Attend weekly company status and safety meetings
- Report Scanning: Scan the weekly Safety meeting report and send it to accounting department
- Project Imaging: Take pictures for each completed fabricated project and or custom mockups and send via email/scan
- Form Scanning: Scan all Panel usage forms for each project or mockup
- Ticket Submission: Bring accountant aluminum usage ticket for all trim and aluminum use from WPS Warehouse for inventory control
- Slip Scanning: Scan all packing slips and shipping paperwork for each shipment
- Document Matching: Match the packing list and Purchase Order
- Defect Reporting: Report any errors, damages or defects right away to the Production manager
- Ticket Scanning: Scan delivery ticket for all materials received and send to Production Manager, Accountant, Office Manager and Project Manager
- Inventory Maintenance: Maintain inventory of all panel material, extrusions, accessories and warehouse supplies and advise the Production Manager of items
- Shop Supervision: Supervise the production shop and ensure they are producing enough work per day
- Package Coordination: Coordinate the packaging of panel material and ensure packages are packed in very well-protected crates or boxes
- Maintenance Monitoring: Monitor machine maintenance requirements and log when maintenance is completed
- Fabrication Quality: Ensure fabrication is done in a quality manner with minimal mistakes
- Production Reporting: Prepare daily production reports showing what work was completed and what materials were used
- Tool Management: Monitor all tools, ensuring they are taken care of properly and stored properly
22. Inventory Manager Details
- Procedure Implementation: Responsible for implementation and best practice for procedures and controls to manage the overall inventory levels and availability for all material types on site
- Inventory Optimization: Make recommendations for improvements to ABC stratification and Safety Stock levels by site
- Delivery Planning: Work with the procurement organization to optimize delivery plans
- Plan Generation: Generate site inventory and SMOG Plans through collaboration with regional SC&PM teams and the Global Inventory Manager
- Transit Optimization: Work with logistics and distribution to optimize transit lanes to reduce overall inventory
- Integrity Oversight: Oversee site inventory integrity results through ongoing validation processes
- Root Analysis: Identify the Root Cause and implement corrective actions for out-of-tolerance items
- Policy Implementation: Implement policies and procedures to mitigate site excess inventories
23. Inventory Manager Responsibilities
- Procedure Execution: Execute formalized inventory procedures
- Cycle Counting: Generate detailed cycle counts to provide measurable inventory results
- Report Creation: Create inventory reports for both internal and external use
- Project Implementation: Identify, prioritize, develop, and implement complex cross-functional inventory control process improvement projects
- Strategy Development: Develop and implement strategies to simplify processes, improve accuracy, and operating efficiency
- Process Auditing: Perform audits to ensure compliance with all processes and measure effectiveness
- Team Direction: Provide appropriate direction and support to team members to ensure inventory control effectiveness
- Performance Management: Manage the performance of salaried and hourly employees, resolve issues, and ensure policy compliance
- Stakeholder Collaboration: Collaborate with senior management and customers to meet needs and expectations
- Payroll Oversight: Responsible for employee payroll
- Profit Analysis: Analyze weekly and monthly P&L statements, provide financial data and operational reports
- Vendor Management: Handle accounts payable, vendor quotes for materials, and customer invoicing
- Safety Training: Hold Safety and Security meetings, provide training, and ensure compliance with safety regulations
24. Inventory Manager Job Summary
- Strategy Execution: Execute the material management strategy to support the company’s business and financial objectives
- Inventory Monitoring: Monitor inventory levels to avoid excess, shortages, and expiration
- Procurement Coordination: Coordinate daily procurement activities with Supply Chain Specialists and Buyer/Planners across multiple sites
- Delivery Scheduling: Work with the Procurement Team to ensure delivery schedules enable continuity of supply
- Backorder Resolution: Ensure supplier back orders are resolved promptly without stockouts
- Process Development: Work with Supply Chain to develop material storage and delivery processes for Lab Operations
- Warehouse Management: Manage 3rd party warehouse locations and associated costs
- Material Release: Collaborate with Quality Control and Assurance to ensure timely material release
- BOM Maintenance: Maintain the Bill of Materials for each assay with DevOps and Lab Ops
- Variance Reporting: Monitor monthly variances and report to management
- Scrap Reduction: Ensure material changes and process improvements minimize scrap costs
- Returns Management: Work with Procurement and Finance on the RMA process for vendor returns
- VMI Program: Establish and maintain VMI programs to support global operations
- KPI Tracking: Manage inventory KPIs and supplier on-time delivery metrics
- Process Improvement: Lead continuous improvement initiatives using lean manufacturing concepts
- SOP Compliance: Ensure compliance with SOPs and regulatory requirements (FDA, GMP, ISO)
- Safety Adherence: Follow environmental, health, and safety protocols
- Shift Flexibility: Maintain availability to work outside of a regular shift
25. Inventory Manager Accountabilities
- Stockroom Oversight: Work closely with the Stockroom Supervisor to oversee all stockroom activities
- Material Accuracy: Ensure materials are accurately received, orders are filled promptly, and inventory balances remain accurate
- Process Improvement: Champion robust material transaction processes with a focus on continuous improvement
- Inventory Monitoring: Monitor inventory levels, enforce FIFO usage, and optimize stockroom organization
- Forecast Enhancement: Continuously improve forecasting techniques, methods, and approaches
- Discrepancy Resolution: Investigate inventory discrepancies, manage stock counts, and perform reconciliations