WHAT DOES A FABRICATION SUPERVISOR DO?
Updated: Jun 12, 2025 - The Fabrication Supervisor ensures a safe and comfortable work environment while setting and monitoring task deadlines. This role involves daily performance evaluations, skill enhancement for staff, and promoting effective intra-team communication and flexibility. Responsibilities also include providing on-the-job training, facilitating cross-training in various trades, and offering consistent feedback to both foremen and leadership on multiple performance metrics.
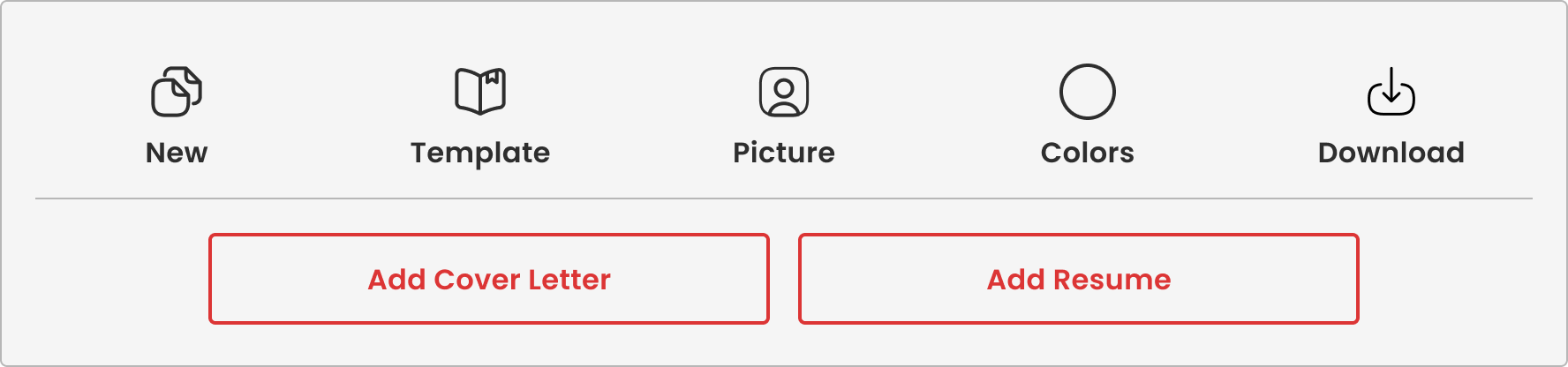

A Review of Professional Skills and Functions for Fabrication Supervisor
1. Fabrication Supervisor Duties
- Team Supervision: Supervise production employees by planning and assigning work, adjusting schedules to meet production requirements, analyzing and resolving work problems, inspecting materials to verify conformance standards, and coordinating with other departments.
- Performance Management: Managing and evaluating performance including coaching employees, conducting appropriate appraisals, and administering discipline, employee training and development, assigning and directing work ensuring proper safety equipment is worn and proper safety procedures are being used.
- Quality Control: Supervise the quality and quantity of products being produced by employees.
- Production Planning: Study production schedules and estimate hourly requirements for completion of job assignments.
- Policy Interpretation: Interpret company policies for employees.
- Process Improvement: Recommend measures to improve production methods, equipment performance, and product quality.
- Problem Resolution: Analyze and resolve work problems or assist workers in solving work problems.
- Record Keeping: Maintain production/quality records and ensure records are filled out correctly and timely.
- Coordination: Confer with other supervisors to coordinate activities of the department.
- Emergency Management: In the absence of higher authority, manage emergencies.
- Team Coaching: Direct & Coach Team Members for Safety, Quality, Cost, Delivery, Standardized Work, and Continuous Improvement.
- Schedule Management: Manage the daily Master Schedule from weekly forecast and daily schedule changes.
2. Fabrication Supervisor Details
- Health & Safety Compliance: Respect health & safety policy and apply it to seek a safe environment for the employees.
- Product Development Participation: Participate in the different phases of new product development.
- Continuous Improvement: Lead continuous improvement by using Lean Manufacturing techniques.
- Safety Activities: Perform activities related to safety.
- QMS Compliance: Participate in compliance with the QMS (Quality Management System) determined for role in relation to the standard ISO9001: 2015.
- Quality Issue Reporting: Identify and report any quality and compliance issues and support corrective actions.
- Work Hour Planning: Plan and maintain daily worked hours and control overtime to meet KPI goals.
- Environmental & Quality Standards: Responsible for applying all requirements related to EMS, ISO9001/14001/50001 Green Spirit.
- Energy Management: Follow, promote, and demonstrate both knowledge and understanding of the plant energy policy and identify the Significant Energy Uses (SEU’s), operational controls, maintenance, objectives, and energy indicator performance.
3. Fabrication Supervisor Responsibilities
- Administrative Support: Administrative tasks including production reporting, material procurement, and all shop performance reports.
- Program Promotion: Promote Fab Shop programs and policies.
- Safety Leadership: Lead all safety standards and seek improvements.
- Team Meetings: Hold regular production meetings with the team.
- Improvement Leadership: Lead involvement in all Fab/Plant improvement programs and Lean initiatives.
- Reporting Compliance: Meet all Fabrication Support Group reporting requirements.
- Quality Assurance: Ensure a high level of product quality while seeking improvements.
- Production Standards Maintenance: Make certain that production and efficiency standards are maintained.
- Cross-functional Communication: Regular communication with Sales, Service, Application Engineering, Fab Service Specialists.
- Team Morale: Bring a positive attitude to the position and be aware of team morale.
- Equipment Maintenance: Lead equipment maintenance and improvement.
- Quality Troubleshooting: Troubleshoot product quality & make improvements.
- Local Reporting Compliance: Satisfy all local Plant reporting requirements.
- Core Values Adherence: Understand and practice ADS Core Values.
4. Fabrication Supervisor Job Summary
- Supervision Fundamentals: Implement the Ten Fundamentals of Supervision.
- Workplace Safety: Ensure the working environment is conducive to worker comfort and safety.
- Time Management: Set and monitor time goals for all tasks.
- Performance Monitoring: Monitor the work performance of staff daily and undertake assessments.
- Skill Development: Enhance and encourage the skill development of staff.
- Timekeeping Management: Monitor timekeeping and verify hours.
- Team Communication: Encourage effective communication and flexibility within the team and gain an understanding of needs and problems.
- Motivation & Morale: Provide motivation, maintain a high level of morale, and minimize confrontation.
- On-the-job Training: Ensure on-the-job training and instruction is provided for trainees and apprentices.
- Cross-Training: Provide avenues for cross-training production staff in multiple trade skills.
- Performance Feedback: Provide feedback to the Foreman or Manager on performance.
- Leadership Feedback: Provide constant feedback to leadership regarding Quality, Cost, Delivery, Safety, and Morale.
5. Fabrication Supervisor Accountabilities
- Compliance Management: Ensures compliance of all work is IAW Austal procedures and NAVSEA Standard Items.
- Repair Management: Manage repair efforts in various offsite locations.
- Requisition Management: Generate requisitions for leadership approval to be obtained from inventory.
- Material Efficiency: Ensure the economic use of materials to meet targets of quality and material elimination.
- Consumable Control: Control issuing and consumption of consumables.
- Equipment & Machinery Management: Control and maintain records of company equipment and machinery under control.
- Maintenance Coordination: Ensure regular maintenance of company equipment and machinery is undertaken in conjunction with the relevant Department.
- Process Improvement Communication: Communicate process improvement potential with equipment requests.
- Workplace Safety: Ensure a safe working environment is maintained meeting standards in addition to local government agencies and ships force requirements.
- Injury Management: Attend to injuries of staff and follow up with necessary paperwork.
- Safety Culture Promotion: Promote a culture of a safe working environment stressing hot work safety, cleanliness of work area, compliance to procedures, and safety requirements.
Relevant Information