WHAT DOES A ELECTRICAL ENGINEERING MANAGER DO?
Published: Jan 02, 2025 - The Electrical Engineering Manager develops standardized test procedures and optimizes processes for efficiency. Assists in engineering software changes and supports sales with timely quotes to enhance business acquisition. Oversees KPI implementation, supervises team activities, and manages operating and capital budgets effectively.
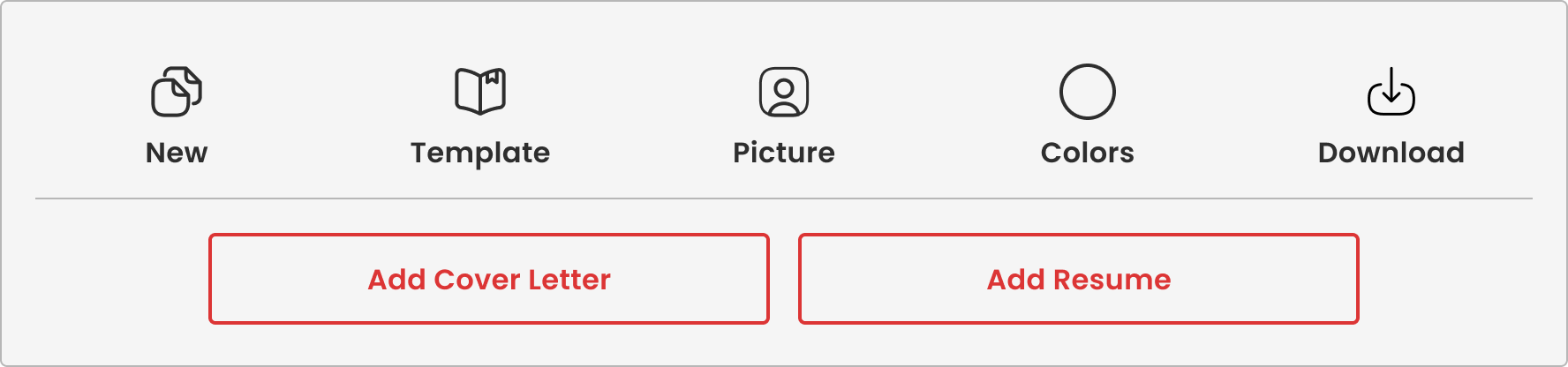
A Review of Professional Skills and Functions for Electrical Engineering Manager
1. Electrical Engineering Manager Duties
- Team Management: Manage a team of Electrical and Associate Electrical Engineers to ensure efficient job flow for high volumes of residential rooftop solar designs.
- Compliance Management: Maintain compliance with the company's electrical standards based on a deep understanding of applicable code intent and contractual obligations.
- Technical Review: Review and analyze the electrical integrity of more complicated jobs that get escalated.
- Research: Research engineering requirements for PV design and installation for existing and new markets.
- Industry Advocacy: Advocate for best practices from an industry perspective (internally and externally).
- Representation: Represent Sunrun in various PV industry code committees and national policy initiatives.
- Stakeholder Education: Work with and educate AHJs and Building Officials to negotiate unique requirements.
- Technical Support: Provide Electrical Engineering support for the PE Team, Site Technicians, Designers, Permit Coordinators, and Installers.
- Inspection Review: Review field inspections and provide Electrical Observations Reports.
- Mentorship: Train and mentor other licensed engineers.
- Policy Development: Define and roll out regional engineering policy to drive better business.
- Communications: Develop and deliver multi-mode communications that convey a clear understanding of the unique needs of different audiences.
- Leadership: Provide leadership, technical direction, and business guidance to engineers.
- Customer Focus: Understand drivers of customer satisfaction and strive to improve the customer experience.
- Process Improvement: Assist manufacturing in the development of processes necessary for efficient production as well as continuous improvement.
2. Electrical Engineering Manager Details
- Supervision: Supervise the work of others and communicate effectively with them.
- Record Keeping: Maintain records and prepare reports.
- Data Interpretation: Use and interpret data from a variety of electrical and electronic instruments and devices.
- Budget Management: Prepare and administer operating budgets.
- Capital Management: Prepare and administer capital projects and budgets.
- Agile Management: Manage hardware engineers and techs using Agile product lifecycle sprint planning and execution of complex technical projects including product specifications, architecture, and GANTT schedules with dependencies and outside resources.
- Standardization: Create test procedures and standards for engineering.
- Software Support: Assist in engineering change and release of the embedded controls software for variable AC/DC power supplies.
- Problem Solving: Make sense of complex, high quantity, and sometimes contradictory information to effectively solve problems.
- Process Optimization: Know the most effective and efficient processes to get things done, with a focus on continuous improvement.
- Sales Support: Assist sales in providing quotes on a timely basis and helping to land new business.
- KPI Management: Develop and implement scalable standards, procedures, and KPI’s and hold the engineering team accountable.
3. Electrical Engineering Manager Responsibilities
- Talent Development: Evaluate and develop the skills and productivity of the Electrical engineers and PCB technicians.
- Technology Monitoring: Continually monitor the latest technologies and methods to ensure Dwyer product development team is up to date with industry best practices.
- Innovation Management: Bring new ideas and technologies to known issues in the HVAC instrumentation market.
- Industry Engagement: Participate in industry associations to help keep Dwyer alert to changes in market needs and regulatory changes.
- Product Oversight: Oversee the design of new products and enhance existing products per Dwyer’s requirements specifications including performing required justification analysis prior to projects.
- Team Leadership: Lead a team of engineers and technicians in developing concepts and performing tests for new products and enhancements to existing products.
- Performance Metrics: Develop metrics to monitor the productivity and quality of the electrical engineering team and individual members.
- Outsourcing Management: Evaluate and justify the appropriate use of outsourcing for design work.
- Project Management: Develop ‘Statements of Work’ and Specification and actively manage outside resources to bring outsourced projects in on-time and on-budget.
- Production Support: Assist the manufacturing engineering team when needed to introduce new products to production.
- Customer Satisfaction: Achieve total customer satisfaction by delivering projects to time and cost constraints.
4. Electrical Engineering Manager Accountabilities
- Leadership: Direct management of electrical and controls engineers including power, pc boards, and PLCs.
- Project Management: Manage tasks and resources for design projects to support company goals.
- Technical Leadership: Provide technical leadership for engineers to ensure design requirements for the product are met and proper design tradeoffs are done.
- Design Review: Prepare and review controls schemes, single line diagrams, and electrical documentation.
- Analysis: Review analysis work supporting the electrical designs including power balancing and SPICE modeling.
- CAD Management: Set up and manage design controls using CAD, PDM, and engineering change management.
- Resource Management: Manage and allocate resources to support engineering, manufacturing, and R&D projects.
- Reliability Design: Integrate DFR (design for reliability) into the team.
- Interdisciplinary Collaboration: Work closely with other disciplines within the company to ensure the product design meets the product specifications.
- Safety Compliance: Work with safety/compliance to implement proper design solutions.
- Strategic Planning: Work with the VP of Engineering to establish timelines, resource planning, and goals for the team to support existing and ongoing company project needs.
- Vendor Management: Drive external resources including vendors and consultants to meet deadlines and support additional design/build efforts.
5. Avionics Electrical Engineering Manager Functions
- Staffing Coordination: Facilitate cross-organizational staffing support.
- Planning: Develop project or operational plans aligned to program objectives.
- Implementation: Implement plans to ensure business, technical, and customer requirements are achieved.
- Delegation: Assign authority and responsibility to employees to execute the plan.
- Collaboration: Operate in close partnership with other engineering teams and project teams.
- Communication: Interact directly with program management on multiple programs to provide status on programs and projects.
- Leadership: Oversee the development of people, processes, tools, and training required; establish metrics for safety, first-time quality, productivity, and affordability.
- Performance Management: Use these metrics to drive continuous measurable improvements.
- Resource Management: Forecast resource needs and obtain and manage personnel to meet project and daily operating requirements.
- Quality Assurance: Ensure workgroup products or processes meet customer, company, quality, industry, and regulatory requirements.
- Approval: Provide approval of workgroup technical approaches, products, and processes.
- Proposal Support: Support new business activities providing input and data to proposals based on actual costs incurred on past projects.