WHAT DOES A DIRECTOR OF MATERIALS MANAGEMENT DO?
Updated: Mai 27, 2025 - The Director of Materials Management defines and manages key metrics to assess business impact and value delivery. Collaborates with stakeholders to educate on automation capabilities, resolve complex issues, and ensure effective communication on process automation initiatives. Leads strategy identification and manages the deployment of automation products to drive business value and operational efficiency.
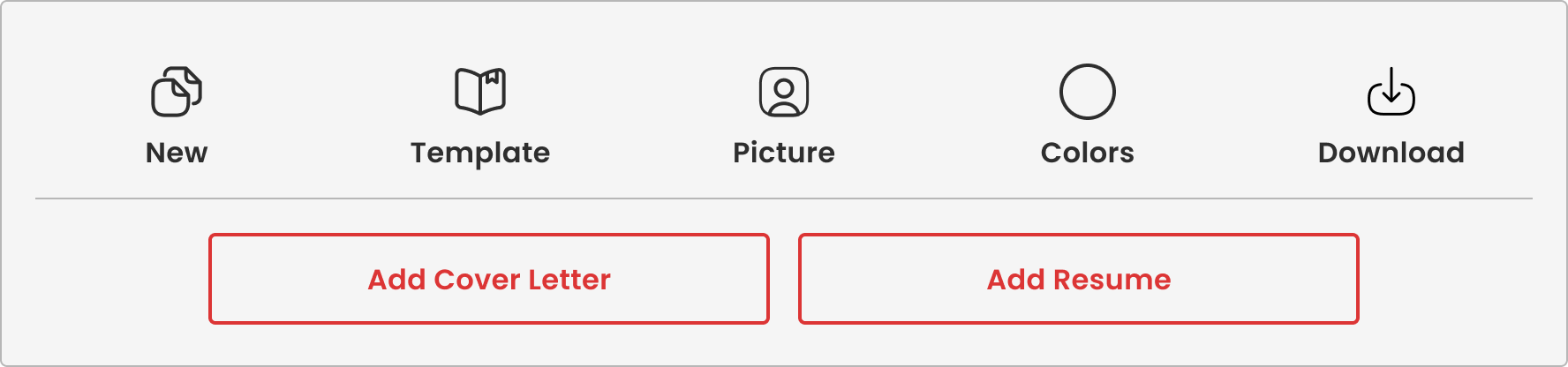
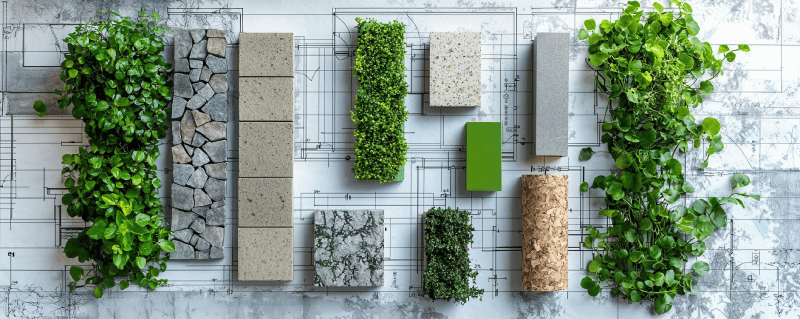
A Review of Professional Skills and Functions for Director of Materials Management
1. Director of Materials Management and Purchasing Duties
- Master Scheduling and Materials Management: Guides, directs, and manages the overall master scheduling, materials, purchasing, and production control activities of the company including raw and finished materials, storage, and inventory control.
- Inventory Control Regulation: Controls, measures, and regulates efficient inventory levels of materials and purchased items.
- Strategic Planning and Budgeting: Directs the preparation of short-term and long-range plans and budgets based on broad corporate goals and growth objectives.
- Departmental Oversight: Oversees the activities of all planning and purchasing departments in planning supply, procuring materials, equipment, and services.
- Cross-Functional Collaboration: Works closely with Sales, Supply Chain Management, Operations, and Engineering to balance customer responsiveness with capacity and material constraints.
- Inventory Control Management: Manages Inventory Control function to ensure the highest levels of accuracy while maximizing inventory turns, and may supervise personnel in any of the materials and purchasing areas.
- ERP System Utilization: Enables and implements the proper use of materials management within a multiple-site ERP environment.
- Policy and Procedure Development: Develops policies, practices, and procedures for utilizing the ERP system and deploying state-of-the-art planning and control techniques.
2. Director of Materials Management Details
- Management Reporting Development: Establish a regular and routine management reporting process that includes forecasts and status for shipping tools, material deliveries, kit issue and release performance, discrepant material processing, inventory levels, cost and lead time reduction, and status of excess/obsolete materials.
- Competency Building: Establish and build levels of planning and procurement competencies in the group to improve the scalability (volume, flexibility, and scope) of the business.
- Process Improvement Leadership: Drive improvements in the planning and procurement processes reducing variation, disruptions, and issues of the processes, while improving process cycle time and decision models.
- Material Requirement Management: Ensure material requirements for production, engineering, and service are effectively established, and deliveries of parts and kit releases are on time to meet manufacturing launches and shipments.
- Inventory Optimization: Ensure that inventory levels are optimized, and forecasted levels are achieved.
- Shortage Management: Ensure material shortages are tracked for a six-week build schedule and that actions are tracked, and contingency plans (and cut-ins) are established.
- Material Planning Direction: Direct Material Planning for the effective execution of work orders and the movement of materials through production and shipping.
- Production Oversight: Ensure the timely closure of production jobs and the issuance of variance reports and the timely disposition of discrepant materials.
- Supply Base Management: Manage the supply base, through the buyers, to secure and sustain the supply of parts that meet quality, delivery, lead time, and cost requirements.
- Supplier Performance Monitoring: Ensure the supply base is issuing respective scorecard monthly and has action plans to achieve the target levels of performance.
- Contract Management: Execute and manage the adherence to the terms and conditions of the supplier contracts, statements of work, and service agreements.
- Negotiation: Negotiate improvements in cost, lead times, and payment terms.
- Order Management: Ensure the timely execution or resolution of issues, with regard to the open order report with suppliers, ECO cut-ins, and invoice reconciliations.
- Warehouse Procedure Management: Ensure the disciplined execution of procedures and cutoffs within the Warehouse staff that efficiently receives and logs parts into the warehouse, optimizes part and location consolidation, and achieves daily shipping goals.
- Safety and Organization Maintenance: Ensure that all activities maintain and improve the level of safety and 5S discipline in the warehouse.
3. Director of Materials Management and Production Planning Responsibilities
- Operational Excellence Management: Maintain operational excellence, and manage all requirements and expectations for each business channel by maintaining or reengineering processes to improve inefficiencies, drive standardization, and/or increase profitability.
- Agile Opportunity Utilization: Access the opportunities across all business channels and leverage agile processes and decisions.
- Strategic Roadmap Development: Responsible for the overall three-year roadmap for all possible solutions for Centric Brands systems and application portfolios by understanding all benefits and limitations with a concentration in Materials Management & Production Planning.
- Systems Research and Coordination: Research and coordination of all new systems and applications.
- Warehouse Process Reengineering: Warehouse process reengineering, warehouse relocation strategies, and execution.
- Systems Development Decision-Making: A key decision-maker on development and implementations for all systems and applications.
- KPI Monitoring: Ensure the solutions are providing the expected benefits for each business channel through measurable KPIs.
- Application Performance Management: Responsible for application performance, including regular check-ins with each business channel and ensuring updates and fixes are carried out in a timely fashion.
- Compliance Documentation: Completion of documentation to show and ensure SOX compliance where applicable.
- Business Process Oversight: Oversight of all business processes and working to maintain best practices and standardization.
- Risk and Budget Management: Risk assessments, adhering to budgets, executing simulations, and data collection.
- Automation Roadmap Development: Develop management of Materials Management and Production Planning automation roadmap from idea through successful implementation, which will drive accountability amongst key stakeholders in Technology and Operations functions (COO, VP Supply Chain/Logistics, Production Operations, and Sales Operational Leaders).
4. Director of Materials Management and Production Planning Accountabilities
- Metrics Management: Define and manage key metrics to measure business impact initiatives and delivery against business value cases.
- Stakeholder Education: Educate key stakeholders in operations on automation capabilities and future opportunities.
- Strategy Identification: Identify strategies for the standardization and applicability of operational systems solutions.
- Communication Planning: Implement a communication plan regarding process automation to ensure status, risks, and remediation plans are clearly communicated to the executive team.
- Issue Resolution: Resolve complex issues that arise during the development and/or implementation of operational systems and document solutions as developed.
- Stakeholder Collaboration: Collaborate with key stakeholders to resolve and provide timely responses to inquiries.
- Future State Definition: Define the evolving future state of operational process automation products and services.
- Automation Deployment Management: Ensure the deployments of process automation products deliver strong business value in an efficient and effective manner.
- Requirements Drafting: Draft acceptance criteria and user story to better facilitate discussions with the executive team about business requirements prior to the implementation of financial products.
- Project Decision Making: Drive key decisions with the key stakeholders on project scope, budget, staffing, interdependencies, and timing.
- Framework Development: Develop robust frameworks and methods to understand the current state of operational system solutions, identify gaps, propose improvements, evaluate solution alternatives, prioritize requirements, and drive consensus to achieve the requirements of the acceptance criteria.
5. Director of Materials Management Functions
- Team Leadership: Supervise, train, and motivate Purchasing department colleagues and thoroughly understand all duties and responsibilities.
- Supplier and Quality Management: Ensure that the department works closely with the Executive Chef, and the Excom Members to purchase the highest quality products while constantly searching for the lowest price.
- Procurement Logistics: Establishment and maintenance of the logistics of procurement.
- Policy Development: Development and enhancement of purchasing and cost control policies and procedures.
- Negotiation: Negotiate cost-effective purchases for all Capex and FF&E items, while meeting all MOHG guidelines and quality specifications.
- Purchase Order Management: Generate purchase orders on approval requisitions, obtain necessary authorization, and obtain authorization from the Director of Finance and General Manager prior to processing these orders.
- Price and Supplier Management: Obtain competitive price quotations and confirm purchase availabilities, establish a purchasing reporting package and database of supplier information and ensure that there are sufficient supplies on hand for all inventoried items for each department by coordinating regular inventories with Stores.
- Storage Management: Ensure that all storage areas are secure, clean, and properly organized and in line with the MOHG health and safety requirements.
- Inventory Management: Establish and maintain par stocks on all inventoried items, keeping in mind that inventory levels must be kept as low as possible without compromising the efficiency of the hotel.
- Quality Control Auditing: Conduct regular quality control audits to ensure colleagues are properly trained and performing duties following established procedures and conduct food supplier premise checks with the Executive Chef before registering the supplier as a vendor to ensure the supplier is compliant with HACCP standards.
- Regulatory Compliance: Maintain regulatory requirements, including all state, federal, and local regulations.
- Ethical Compliance: Comply with all organizational policies and standards regarding ethical business practices.