WHAT DOES A COST ANALYST DO?
Updated: Jan 06, 2025 - The Cost Analyst collaborates with Sales to refine pricing and identify opportunities for operational cost reductions. Through rigorous analysis of labor variances, rework, and production metrics, actionable insights are derived to support quantitative analyses and cost/benefit evaluations for improvement initiatives. The role also involves compiling cost and pricing data for governmental bids, ensuring meticulous inventory reconciliations, and enhancing electronic manufacturing solutions, while coordinating closely with operations and purchasing departments on material and production planning.
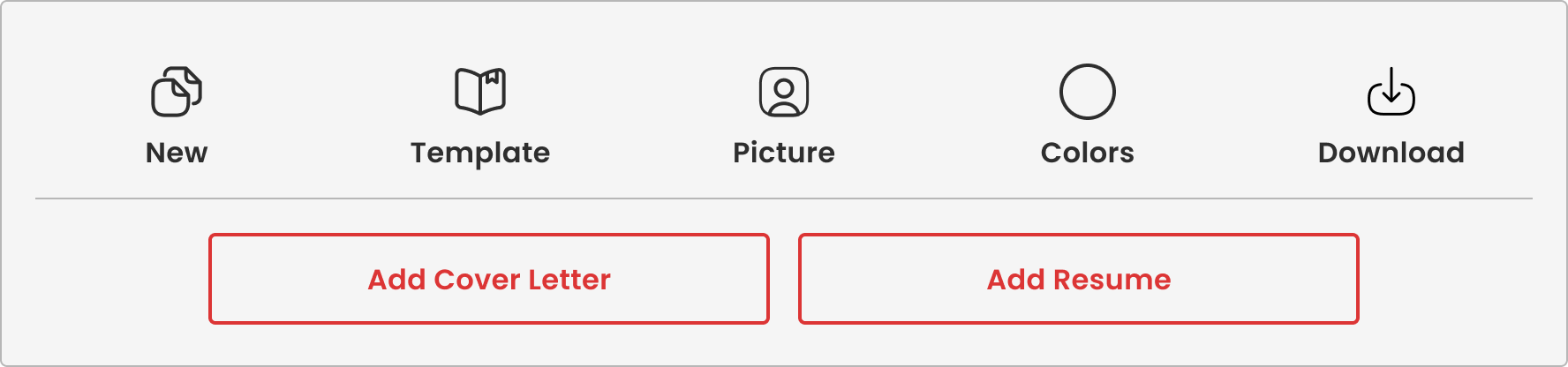
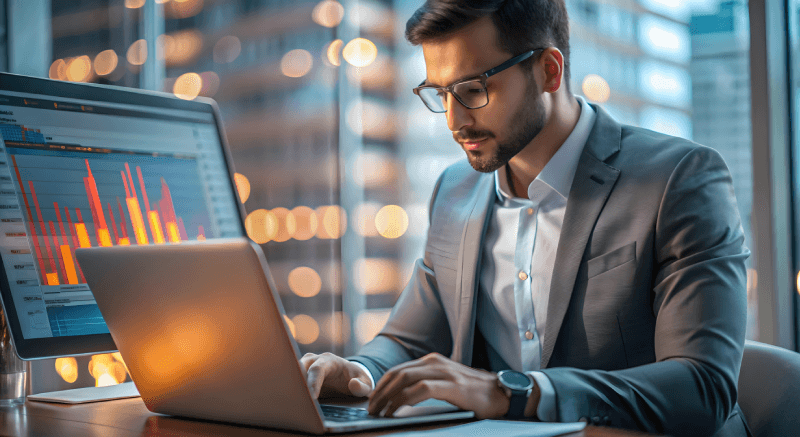
A Review of Professional Skills and Functions for Cost Analyst
1. Cost Analyst Duties
- ERP System Collaboration: Collaborate with manufacturing engineering, production, and materials procurement to ensure accurate costs are in the ERP system.
- Margin Forecasting: Forecast margin in backlog by program and customer.
- Sales Collaboration for Cost Reduction: Work with Sales on pricing and operations cost reductions.
- Production Variance Analysis: Analyze all significant labor, rework, and other production variances.
- Cost/Benefit Analysis: Conduct cost/benefit analysis and other quantitative analysis to support improvement initiatives.
- Project Control and Reporting: Control, track, and report on improvement projects.
- Governmental Bidding: Compile Cost and Pricing Data packages for large governmental bids.
- Inventory Reconciliation: Perform monthly reconciliations for inventory and thorough review of excess inventory calculations.
- Inventory Cycle Coordination: Coordinate regular cycle counts and annual physical count in the stockroom.
- IT Development for Manufacturing: Utilize IT skills to develop and improve electronic solutions for manufacturing.
- Inventory Management Support: Support the process of setting inventory levels, schedules, and availability of selected items either manufactured or purchased to meet production demands.
- Production and Purchasing Interface: Interface with operations personnel and the purchasing department on material status and production planning issues.
- SMOG Analysis: Responsible for analyzing and reporting on slow-moving and obsolete goods (SMOG) in coordination with the demand planner.
2. Cost Analyst Details
- Budget Management: Responsible for planning, data collection, control, and reporting of annual plant budget and periodic financial forecasts.
- Operations Reporting: Responsible for producing and evaluating operations performance reporting, including key performance indicator and variance analysis reporting in coordination with operations personnel.
- Financial Control: Responsible for the financial control (valuation) of inventories and manufacturing costs.
- Inventory Accounting: Manages accounting functions in support of annual physical inventories and periodic cycle counts.
- Cost Estimation Management: Manages the function of cost estimation, interfacing with and supporting product development teams on an ongoing basis.
- Data Coordination: Responsible for managing the process of maintaining correct Item master, BOM, and Routing files in coordination with Master Data.
- Productivity Reporting: Provides financial reporting and analysis in support of plant productivity initiatives (Low Cost Producer).
- Ad Hoc Reporting: Provides ad hoc reporting to support financial analysis of plant operations and prepares financial presentations.
- Standard Costing: Manages the function of setting standard costs.
- Policy Compliance: Ensures proper authorization and compliance with company disbursement policies.
- Capital Expenditure Control: Responsible for ensuring adherence to company policies, controls, authorization, and proper accounting for all plant capital expenditures.
- Financial Closing: Responsible for the Plant’s financial function of month end/year end closing in accordance with GAAP.
- Tax Assistance: Assists with property tax and sales tax planning and filing.
- Capacity Planning: Responsible for managing the analysis of Sales demand with respect to capacity planning, material and labor requirements in coordination with the demand planner and plant operations.
3. Cost Analyst Responsibilities
- Program Planning Support: Provide program planning support, including scheduling, budgeting, variance analysis, status reporting, and resource planning.
- Project Scope and Budget Management: Work with project leadership and technical team to develop, monitor, and analyze changes to the project scope, schedule, and budget for a variety of ongoing projects.
- Financial Forecasting: Prepare monthly and annual forecasts of project budgets, document monthly and annual project budget, monitor contract/project expenditures and report variances to management.
- Decision Support Information: Provide project leadership with clear, timely, and accurate information and make recommendations with which to make decisions.
- Financial Impact Analysis: Understand the financial impact of contractual, procedural, and technical issues in order to resolve or recommend solutions to various levels of management.
- Financial Deliverables Compliance: Ensure all financial deliverables are submitted, communicate with the customer to ensure financial requirements are met.
- Stakeholder Communication: Participate in Integrated Product Team (IPT) meetings to keep stakeholders informed of financial/schedule status updates.
- Integrated Schedule Development: Assist in the development/maintenance of Integrated Master Schedules.
- Proposal Support: Participate in proposal generation through Basis of Estimate (BoE) support, cost modeling, and providing input into cost volumes.
- Innovation Leadership: Generate improvement ideas, lead idea generation sessions.
- Solution Evaluation: Evaluate alternative solutions in WoW, process, system, or other.
- Process Design: Design (new and improved) processes including interaction by all stakeholders (RACI).
- ERP System Management: Review, manage, and update cost data in ERP system.
4. Cost Analyst Accountabilities
- Cost Accounting Management: Help plan, organize and execute major cost accounting tasks (physical inventory, year-end standard cost setting).
- Cost Reduction Planning: Works with department managers to develop and maintain annual cost reduction plan.
- Data Analysis: Analyzing data and providing information to calculate the impact of the reductions.
- Communication: Responsible for communicating this information to management to update monthly budget/forecasts.
- Variance Analysis: Prepares monthly variance analysis, participates in forecasting activities for variations and other cost components, and communicates performance to management.
- Warranty Reporting: Prepare and analyze monthly domestic and international warranty reports and provide variance information and recommendations to Management.
- Warranty Forecasting: Forecast future warranty trends/liability and report on financials.
- Financial Adjustments: Prepare warranty journal entries and accrual adjustments for monthly close.
- PPV Management: Review weekly PPV Report, identify and correct purchase price variances and issue monthly PPV report to Management.
- Costing Development: Work to develop and update costing for these new product launches.
- Inventory Oversight: Helps oversee annual physical inventory of three locations.
- Inventory Management: Communicating instructions to operations, overseeing the inventory input, reconciling differences, and booking the physical inventory adjustment.
- Costing Strategy Development: Develops costing strategies for new product.
5. Cost Analyst Functions
- Budget Coordination and Forecasting: Coordinates and participates in the annual budget and quarterly forecasting processes for assigned accounts.
- Results Consolidation: Consolidates various monthly results with commentary on key drivers.
- Spending Review Leadership: Leads monthly spending reviews with departments and anticipates future spending.
- Spending Analysis: Provides detailed explanations and analyses on departmental spending and key drivers vs. budget and forecast on a monthly, quarterly, and annual basis.
- Month-End Responsibilities: Performs month-end duties necessary for closing the books.
- Journal Entries and Accruals: Books necessary journal entries/accruals.
- Balance Sheet Reconciliations: Performs balance sheet reconciliations for assigned accounts.
- Inventory Analysis and Approval: Reviews and approves inventory reconciliations, inventory and freight forecasts, and deferred inventory analysis.
- Excess Inventory Analysis: Prepares quarterly Excess and Obsolete inventory analysis.
- Inventory Management Collaboration: Works with supply chain and inventory managers to properly identify, reserve, and write off slow-moving and obsolete inventory.
6. Cost Analyst Job Description
- Reporting Review: Review and report on all ETS’s approved nationally by region and variance type.
- Variance Analysis: Thorough investigation, analysis, and insight into root causes deriving variance.
- Opportunity Identification: Compare job orders raised to standard to identify opportunities, targeting quantity and value variances.
- Cost Analysis: Analyzing and reporting on preliminary costs incurred prior to site start.
- Recharge Identification: Identify re-charges due to incorrect ordering and ETS approvals.
- Calculator Review: Review internal calculators to ensure consistency and accuracy, recommend changes where necessary.
- Cost Audit: Audit site costs budgets vs. actual.
- Profit Analysis: Job Profit reporting review targeting margin erosion.
- Trend Monitoring: Monitoring trend movements on ETS incurred over and above standard orders, in particular site works.
- Economic Analysis: Review Economic classified ETS to track trade rate movement in regions.
- Improvement Reporting: Reporting monthly findings and putting forward recommendations and areas for improvement.
- Collaborative Analysis: Working closely with internal departments to understand context and provide feedback.
7. Cost Analyst Overview
- Operational Support Experience: Hands-on experience in supporting plant operations teams through budgeting, financial and operational controls, month-end close, cost and savings tracking, and variance analysis.
- Procurement and Logistics Analysis: Worked closely with procurement and/or logistics teams on providing business information, what-if analysis, and cost-saving evaluations.
- Cost Optimization Initiatives: Supported driving programmatic or sustained cost or optimization initiatives, resulting in significant savings to the Supply Chain.
- Performance Metrics Delivery: Delivered on time and accurately, key performance metrics, tracker action items, and follow-ups, and helped to identify root causes of operational challenges to drive higher levels of performance.
- Financial Management: Managed significant financial areas of the plant, from cost accounting, work order management, inventory management, budgeting, forecasting, fixed asset accounting, and controls.
- Culture of Accountability: Been part of creating or supporting a culture of accountability and responsibility within the operations team.
- Manufacturing Cost Analysis: Worked closely with the manufacturing/value-added department team to obtain inputs into the cost models and to review and analyze standard costs and bills of materials for completeness and accuracy.
- Cost Standards Analysis: Analyze monthly actual costs to ensure standards are in line.
- Cost Trend Analysis: Review and analyze various cost trends over time.
- Time Studies: Perform time studies on a regular basis, on manufactured products.
- Raw Material Cost Awareness: Be aware of and understand how changes in raw materials costs could affect costs and gross margins.
- New Product Cost Analysis: Analyze costs associated with new products and review if products fit into the business strategy.
8. Cost Analyst Details and Accountabilities
- Data Process Development: Develop data processes to enable more scalable/automated systems, processes, and reporting.
- Program Support: Support Ring OEM business and GCM teams on the day-to-day execution of the existent program implementation.
- Cost Management: Ownership of cost validation and pricing erosion processes, focusing on accuracy, controllership, and operational efficiency.
- Data Analysis: Retrieve and analyze data using Excel and other data management systems.
- Metric Monitoring: Monitor existent metrics, analyze data, and partner with internal teams to identify process and system improvement opportunities.
- Reporting Design: Design and implement reporting solutions to enable stakeholders to manage the business and make effective decisions.
- Project Leadership: Drive small to medium operational enhancement projects.
- Trend Analysis: Proactive investigation and root cause analysis of trends seen in business metrics.
- Strategic Insight: Sharing informed insight and recommendations based on data analyses that will drive automation, optimization, and scalability of core processes and/or strategy execution.
- Pricing Strategy: Determine customer pricing based on margin guidelines and suggest retail prices based on sales targets.
- Pricing Maintenance: Update and maintain pricing.
- Product Rationalization: Maintain and recommend product rationalization of current SKUs and set up regular reviews.
9. Cost Analyst Tasks
- Workplace Safety Compliance: Support and contribute to a healthy and safe work environment by following all workplace regulations, policies, and initiatives, including reporting all first aid injuries, accidents, and workplace hazards.
- Risk Management and Corrective Actions: Identify workplace risks and implement corrective actions.
- Health and Safety Communication: Communicate Health and Safety rules to all employees and ensure compliance.
- Role Model for Safety: Set a good example by adhering to the Health and Safety rules.
- Disciplinary Measures for Safety: Apply the Health and Safety disciplinary measures procedure if necessary and keep supporting documentation.
- Policy Adherence: Fully understand and adhere to all relevant Environmental, Health and Safety, Human Resources, Quality, Security, and Company policies and procedures.
- Cost Analysis Partnership: Partner with Finance, Engineering, and Operations in determining product costs, bill of materials (BOM), and overhead to ensure accurate costing.
- Production Variance Analysis: Analyze production variances, including fluctuations between forecast and actual, with understanding, explanation, and resolution of the same.
- Financial Reporting: Participate in monthly and quarter-close financial close and reconciliation.
- Inventory Analysis: Conduct quarterly inventory reserve analysis and generate reports for management.
- Process Improvement: Identify and support continual process and procedure improvements for increased efficiency in managing data for analysis.
- Strategic Financial Analysis: Build relevant ad hoc analysis for business insight and effective decision-making, related to key strategic Finance initiatives.
10. Cost Analyst Roles
- Cost Analysis: Review all jobs to ensure that reasonable costs exist for prep time, press time, finishing, shipping, plates, inks, paper and outside work.
- Data Entry: Entering of ink consumption from docket files received daily from Planners.
- Cost Discrepancy Research: Research and discuss discrepancies in costs with the various department managers.
- Rate Standardization: Establish standard rates and maintain standard rates system.
- Costing Support: Assist Data/Costing Clerk with day-to-day costing issues.
- Inventory Management: Participate in physical inventory cycle counting.
- W.I.P. Monitoring: Review W.I.P. inventory for all dockets monthly.
- Docket Management: Prepare listing of open dockets by planners for distribution to inquire status of open jobs.
- Docket Resolution: Resolve disposition of open dockets with Account Managers and Controllers.
- Report Preparation: Prepare the weekly, monthly KPI & metrics reports.
- Quality Maintenance: Maintain quality standards as per written or verbal instructions and follow all SOPs applicable to the work.
- Team Collaboration: Work as part of a team, follow and adhere to Transcontinental’s code of ethics, and participate in the Continuous Improvements efforts.
- Policy Adherence: Fully understand and adhere to all relevant Environmental, Health and Safety, Human Resources, Continuous Improvement, Security and Company policies and procedures.
- Regulatory Compliance: Work in compliance with the Occupational Health & Safety Act of Ontario, the Workplace Safety Insurance Act and all other applicable legislated environmental, health & safety regulations.