WHAT DOES A COST ENGINEER DO?
Updated: Jan 06, 2025 - The Cost Engineer provides crucial cost controlling support to buyers and design engineers during the concept and product development phases, establishing and managing cost activities for supplier cost reduction. Monitors cost variances and movements against agreed targets, ensuring budget expenditures are accurately captured for purchasing. Assists in supplier development and negotiations, while also conducting reviews of internal financial systems to enhance cash flow, working capital, and balance sheet management.
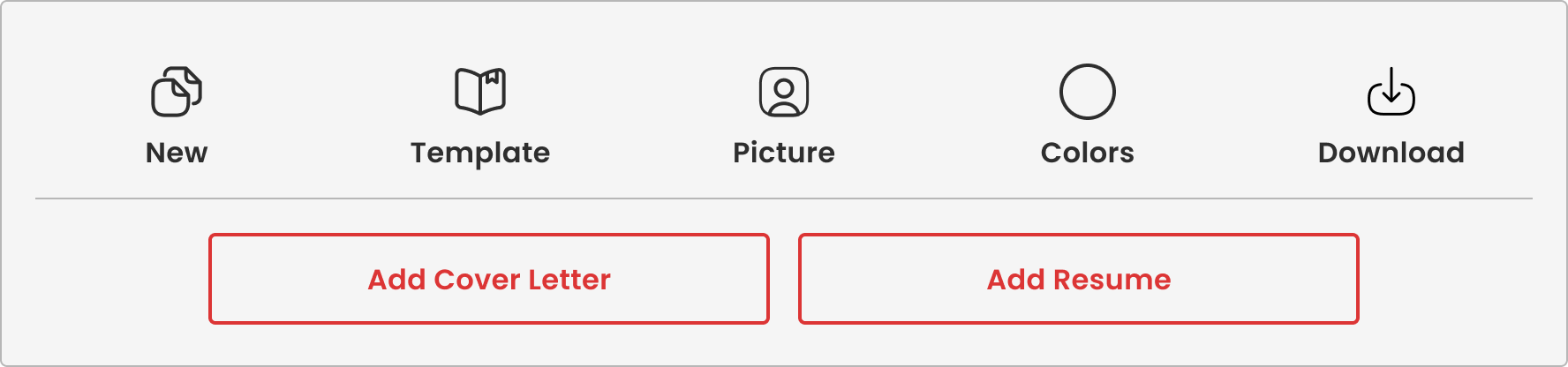
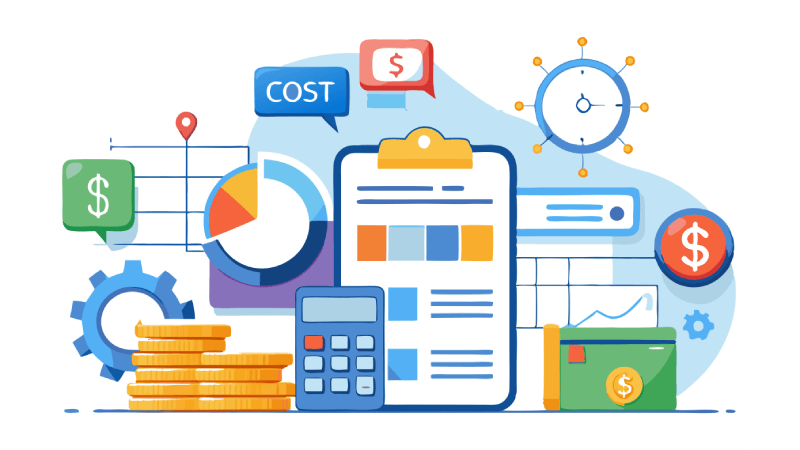
A Review of Professional Skills and Functions for Cost Engineer
1. Cost Engineer Duties
- Database Management: Maintain the Cost Management database and ensure that forecast and budgeted costs align with cost flows for Earned Value purposes.
- Reporting Development: Develop and contribute to the weekly and period reporting requirements.
- Financial Forecasting: Participate in re-forecasts as required by the Programme.
- Project Control Deployment: Deploy and implement the Project Control requirements included in contracts.
- Contract Interface Management: Interface with contract administration on contract issues and status of changes.
- Change Assessment Support: Aid with the assessment of changes.
- Cost Study Preparation: Participate in the preparation of cost studies using historical data, statistical analysis, and cost and quantity comparisons.
- Technique Development: Develop new techniques as required to meet specific needs within the specified parameters.
- Change Identification Assistance: Assist projects in identifying and assessing changes.
- Value Engineering Participation: Participate in and contribute to Value Engineering studies
2. Cost Engineer Details
- Specification Analysis: Analyze plans and specifications for clients.
- Team Collaboration: Collaborate with small teams to develop accurate and complete cost estimates.
- Technical Review: Provide technical reviews of design, analysis, and specifications.
- Problem Solving and Budget Monitoring: Problem-solve any issues and monitor project budgets.
- Invoice Analysis and Reporting: Review and analyze sub-contractor invoices and provide progress reports.
- Cost Analysis: Perform cost-to-complete analysis for all cost elements.
- Order Review: Review task orders for contractors and sub-consultants.
- Financial Reconciliation: Analyze change order and bid award values against current budget and prepare reconciliations.
- Negotiation Strategy Participation: Participate in team meetings to prepare negotiation strategies.
3. Cost Engineer Responsibilities
- Cost Control Support: Provide cost controlling support to Buyers and Design Engineers during the concept and product development phase.
- Supplier Cost Management: Establish and manage cost activities with suppliers for cost reduction.
- Cost Variance Monitoring: Monitor and identify cost variances and movements from agreed targets.
- Budget Expenditure Monitoring: Monitor budget expenditure to ensure that all budget expenditures are captured for purchasing.
- Project Coordination Support: Coordinate and support the design, development, manufacture, and introduction of components and systems.
- Supplier Development Assistance: Assist in the development of existing and new suppliers.
- Supplier Negotiation Assistance: Assist in negotiation with a supplier with the support of the buyer and Supplier Quality Engineer.
- Financial System Review: Conduct an initial review of internal financial systems, processes, and controls.
- Cash Flow Management: Manage cash flow and working capital.
- Balance Sheet Management: Manage balance sheet and ensure financial integrity.
- Senior Management Support: Provide robust support for senior management.
4. Cost Engineer Accountabilities
- GD&T Review: Review of Part print and GD&T requirements.
- Tooling Quoting: Quoting of Die Tooling, check fixtures, and Assembly processes.
- GD&T Data Review: Review part data and GD&T information.
- RFQ Management: Send out Requests for Quotes to Tool vendors for costs.
- Cross-functional Coordination: Interfaces with other individuals in the organization to obtain costs and process information.
- Cost Estimation Support: Review all data supplied by Sales Team, estimate blank sizes using software, and process data from tools shops.
- Pre-source Participation: Internally estimate cost and attend pre-source meetings.
- Quoting System Management: Enters data into Internal Quoting System to complete quotes for Sales Team.
- Job Tracking: Maintain job tracking daily/weekly/monthly.
- Cost Impact Analysis: Identify and quantify requirements that impact costs such as labor, engineering, tooling, etc.
- Estimating Process Improvement: Provides improvement recommendations to cost estimating procedures to reduce future discrepancies between estimated and actual costs.
- Quoting Process Identification: Identifies process required to quote jobs for customers.
5. Cost Engineer Functions
- Cost Estimation: Estimate supply and/or production costs of parts and assemblies rolled up to an air vehicle design.
- Data Analysis: Analyze technical data, including 3D models prior to design completion, to ensure the optimum design for cost manufacturing processes is used.
- Material and Process Optimization: Establish the optimum raw material and manufacturing process to obtain the best production cost.
- Value Engineering Support: Support the Value Engineering team in forecasting accurate air vehicle direct operating costs.
- Negotiation Leadership: Prepare and lead negotiations of production costs with partners.
- Cost Reporting Management: Manage and issue cost reports.
- Continuous Improvement Participation: Participate in continuous improvement activities of partnership processes.
- Audit Compliance: Carry out Contractor and 3rd Party Audits as required to ensure compliance with conditions of Contract.
- Tender Support: Support Procurement Team members in Tender Preparation and Tender Analysis.
- Contractor Performance Analysis: Participate in Contractor efficiency improvement initiatives resulting from analysis of planned vs actual Contractor performance data.
- Cost Control & QS Function: Provide cost control and QS function on a portfolio of Refinery Projects, in alignment with Business demand.