GLOBAL QUALITY DIRECTOR SKILLS, EXPERIENCES, AND JOB REQUIREMENTS
Published: Apr 18, 2025 - The Global Quality Director brings extensive experience in global quality systems, supply chain metrics, and lean practices. This role requires leading international quality teams and executing strategic supply chain initiatives. The director ensures excellence through strong supplier management and team development.
Essential Hard and Soft Skills for a Global Quality Director Resume
- Design Validation
- Product Maintenance
- Quality Assurance
- Root Analysis
- ISO Management
- Audit Closure
- QMS Implementation
- Process Assessment
- MES Integration
- CAPA Execution
- Cross-Communication
- Problem Solving
- Issue Resolution
- Knowledge Sharing
- Customer Focus
- Team Leadership
- Succession Planning
- Client Relations
- Complaint Resolution
- Team Development
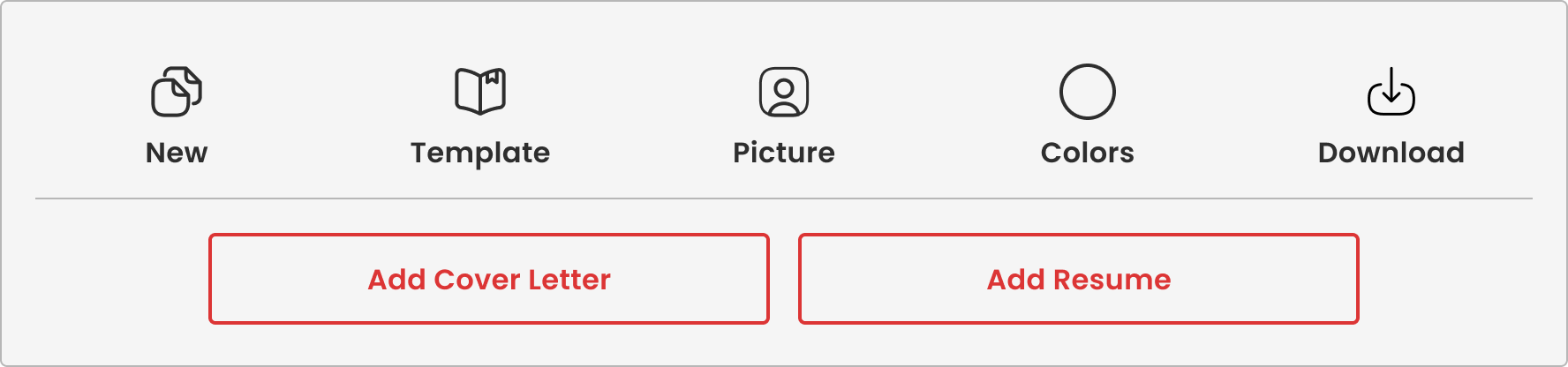
Summary of Global Quality Director Knowledge and Qualifications on Resume
1. BA in Manufacturing Systems with 4 years of Experience
- Previous formal training and certification in Quality Assurance management
- Demonstrated and proven capability in setting up and managing an effective quality system
- Industrial experience in Life Sciences in a hands-on Quality Assurance capacity, demonstrating capability in all aspects of the job requirements
- Experience in different functions of Operations or R&D
- Ability to manage global quality assurance in an unbiased and consistent manner
- Strong teamwork, leadership, organization, and communication skills
- Previous Quality Assurance experience in engineering and manufacturing environments
- Working knowledge of safety requirements, legal standards, and quality system requirements
- Good in English and Mandarin
- Able to track records of new product launches, new sites set up and business transfers
2. BA in Quality Management with 5 years of Experience
- Working experience in the Quality field within an MNC culture with exposure to managing global sites
- Strong in design quality or Advanced Quality Engineering background, experience in NPI/R&D
- Experience in plastic injection molding, assembly or medical devices
- Strong communicator with proficiency in English and Chinese to communicate with the Asia and Europe teams
- Experience in an FDA-regulated pharmaceutical and/or medical device industry environment
- Strong knowledge of current global Good Clinical Practice (GCP) for designing, recording and reporting trials that involve the participation of human subjects
- Current and in-depth knowledge of audit techniques and government regulatory inspection procedures
- Working knowledge of current Good Manufacturing Practice (cGMP) regulations
- Strong project management, leadership, problem-solving, and organization skills
- Excellent interpersonal and communication skills
3. BA in Logistics and Quality with 3 years of Experience
- Experience in reporting and presenting with a metrics-based approach
- Understanding and experience with process mapping, presenting, teaching, and facilitating
- Proven ability to lead programs/projects/teams to a successful conclusion through superior presentation and teaching skills
- Experience driving performance and results with functional teams using a continuous improvement methodology such as 6 Sigma, Lean, OEE, and/or others
- Ability to interface and effectively influence all levels of the organization
- Strong interpersonal, communication, and presentation skills with a focus on coaching and influencing others
- Ability to communicate that to the whole organization in a way that creates excitement and activates transformational change
- Proficient computer skills with a desired knowledge of Word, PowerPoint, Excel, Smartsheet and Visio
- Able to lead, influence, motivate and generate teamwork among a cross-functional group of stakeholders located throughout our global offices
- Proven track record of delivering results in a high-performance continuous improvement environment through implementation of and expertise with the latest quality system and lean management methods
4. BA in Quality and Compliance with 2 years of Experience
- Strong analytical and problem-solving skills required including a thorough understanding of how to interpret customer business needs, translate them into operational requirements and then lead the implementation cross-functionally
- Ability to develop an effective lean roadmap across functions with appropriate metrics and tracking
- Able to be a change agent and self-starter, able to take the initiative and push projects forward as well as constructively and convincingly challenge the views of others when required to bring about positive change
- Good written and verbal communication skills with the ability to operate successfully across an organization at all levels
- Competent in the use of Microsoft Office and ERP systems, Lean tools, and Value stream mapping
- Ability to navigate through ambiguity and rapid growth and adapt to change
- Ability to be agile and effectively collaborate in a dynamic, cross-functional matrix environment
- Must have certifications such as PMP, Six Sigma Certifications
- Experience in a manufacturing environment, specifically in metalworking or medical device manufacturing
- Project Management and Lean Manufacturing experience
- Working knowledge of ISO 9001:2015, ISO 13485:2015, 21 CFR and cGMPs
5. BA in Regulatory Affairs with 4 years of Experience
- Working experience in Biologics and Pharma
- Experience in the biopharmaceutical Industry in a Manufacturing, Quality, Technical, or Regulatory position or a combination thereof and/or working with a regulatory health authority
- Experience leading or supporting commercial manufacturing sites through global health authority inspections
- Ability to identify and implement phase-appropriate compliance strategies to support the E2E product lifecycle
- Demonstrated ability to apply effective risk management approaches that provide a proactive means of identification and control of potential quality issues
- Demonstrated experience leading through influence and working in cross-functional / matrix teams to investigate and manage quality and compliance-related issues
- Demonstrated ability to make and act on decisions while balancing speed, quality and risk
- Ability to think clearly and decisively and remain calm under adverse conditions
- In-depth knowledge of quality systems principles and applications
- Excellent communication and interpersonal skills
6. BA in Quality Systems with 3 years of Experience
- Experience in operations/manufacturing quality, supplier quality, and/or quality management systems
- Working experience managing and developing a quality program and quality team in a manufacturing environment
- Experience in the electronics industry
- Statistical analysis experience in a quality department for a manufacturer of electrical or mechanical products
- Must qualify for industry-recognized quality programs such as Six Sigma, Lean, and TS16949
- Experience managing an ISO-9001 program
- Proficient in computer literacy in MS Office, databases, and statistical computer programs
- Excellent written and verbal communication skills, and a proven ability to communicate with personnel in all areas of an organization
- Previous experience working in the global pharmaceutical and medical device industry
- Experience working with external service providers
7. BA in Lean Operations with 6 years of Experience
- End-to-end global quality experience in positions of increasing responsibility in high-growth environments
- Experience leading quality teams within the consumer goods industry
- Experience traveling internationally and knowledge of major associated customs in global regions, especially in Asia
- Extensive experience establishing and managing quality performance metrics for all aspects of the supply chain (vendor scorecards, FTQ, RTY, cost of quality)
- Deep expertise and experience managing global quality systems including Quality Assurance, Quality Control and RMA processes
- Excellent team mentoring and coaching skills with a demonstrated track record of building and developing high-performing global teams
- Must have a broad and versatile set of skills capable of managing a variety of different supplier types and locations globally
- Strategic thinker with the ability to roll up sleeves to get work done
- Demonstrated ability to develop, communicate, and execute a multi-year global supply chain strategy
- Deep understanding of lean practices
8. BA in Strategic Operations with 2 years of Experience
- Demonstrated ability to act as a change agent with manufacturing partners to lead improvements
- Critical thinker with strong analytical skills employing ROI and root cause analysis
- Inquisitive, detail-oriented, fact-based, and data-driven
- Strong drive for results with ability to thrive in a fast-paced, constantly changing environment
- Excellent oral and written communication skills
- Ability to work in a matrix environment and build strong relationships by being transparent, reliable and delivering on commitments
- Ability to provide innovative, compliant ideas or alternatives that create value including seeking new information and external insights
- Pragmatic in approach with demonstrated ability to make sound, risk-based decisions
- Good knowledge of statistical tools and appropriate use of Design of Experiments (DOE) when developing recommendations
- Demonstrated ability to work independently and with groups of people/teams in a complex changing environment