WHAT DOES AN EHS DO?
Published: Jun 6, 2025 - The EHS (Environmental Health and Safety) Professional oversees compliance with environmental, health, and safety standards through regular inspections, audits, and risk assessments. This role involves implementing control measures and safety systems to reduce hazards and ensure regulatory adherence. The position also delivers EHS training and coordinates emergency plans to strengthen workplace safety and operational resilience.
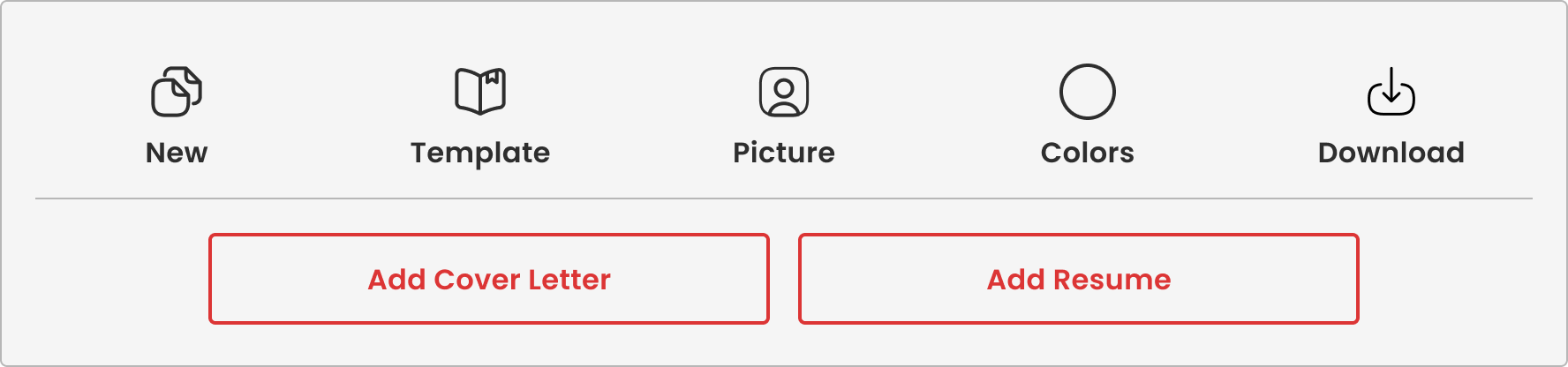

A Review of Professional Skills and Functions for Environmental Health and Safety
1. Environmental Health and Safety Culture Leader Duties
- Safety Framework Development: Develop a framework to promote a Zero Harm Safety Culture.
- Coaching and Mentoring: Coach and mentor the workforce, specifically around safety behaviours, accountability for safety, interventions, and creating a ‘zero harm culture’.
- Stakeholder Collaboration: Collaborate with key stakeholders, including the client, to ensure ultimate HSE practices and performance are realised.
- HSE Support: Provide HSE support and direction to all employees and subcontractors working on Abergeldie projects.
- Training: Provide training and verification of competencies for staff.
- Construction Methodology Advice: Provide advice in the development of construction methodologies to ensure practical controls and mitigation.
- HSEQ Platform Utilization: Champion the use of HSEQ platforms to ensure the accurate and timely reporting of all related matters to enable the extraction of relevant data on an ongoing basis.
- HSE Data Analysis: Coordinate the compilation and analysis of project-specific HSE statistics.
- Regulatory Compliance: Ensure compliance with all applicable health, safety, and environmental legislation.
- Authority Liaison: Liaise with relevant authorities for the team regarding HSEQ issues.
- Incident Investigation Support: Facilitate and assist project management teams when conducting accident and incident investigations (including ICAM investigations).
2. EHS Advisor Details
- EHS Oversight: Oversee day-to-day site EHS arrangements, provide support and guidance, and act as local contact for any EHS-related enquiries
- Risk Communication and SOP Training: Keep the Management Team informed on any potential risks, whilst providing support to the team in deploying/training on new SOPs or updates on any EHS-related processes
- Environmental Compliance: Ensure compliance with environmental legislation
- Emissions Monitoring: Maintain the environmental emissions monitoring program
- Groundwater Monitoring: Maintain the groundwater monitoring program
- Effluent Process Awareness: Maintain awareness of the site's effluent treatment process
- Incident Management: Ensure all accidents, incidents (hazards and near misses) are reported, recorded, investigated thoroughly, and any actions are effectively monitored until closure.
- Environmental Impact Control: Ensure that activities are undertaken with minimal impact on the environment and are compliant with local legislation.
- Local Training Engagement: Increase knowledge, competence, and engagement at a local level through effective training
- Lead Auditor Certification: Lead auditor trained (14001)
3. Senior EHS Advisor Responsibilities
- EHS Program Development: Develop procedures and programs to support the site’s EHS Management System
- EHS Leadership Support: Serve as a delegate for the EHSS Manager
- Compliance Auditing: Perform audits to assess compliance with regulatory requirements
- Safety Culture Engagement: Support stakeholder engagement to embed safety culture into the business
- EHS Reporting: Prepare reports and interface with regulatory agencies and GSK organizations in regards to EHS performance data
- EHS Training: Develop and provide EHS-related training
- Risk Assessment: Participate in EHS risk assessments and incident investigations
- Technical EHS Expertise: Provide technical expertise to line organizations as a Subject Matter Expert (SME)
- OSHA Regulatory Compliance: Work with OSHA General Industry regulations 29 CFR 1910, as they pertain to the manufacturing industry
- Data Presentation: Develop and present factual data to influence the decisions of others who are not under the immediate chain of command
- Commercial EHS Risk Facilitation: Facilitate commercial Environment Health and Safety risk assessment in commercial local operating companies to identify risks in critical areas
4. Environment, Health and Safety Analyst Job Summary
- Chemical Systems Management: Manage chemical management systems (MSDS/SDS systems) as they relate to EHS compliance and customer distribution, and other internal business systems or web-based systems.
- EHS Data Coordination: Develop, coordinate, and support existing data collection and employee communication as they relate to EHS-related systems.
- EHS Plan Development: Develop and support written EHS plans, programs, and procedures.
- Training Materials Update: Develop and update annual EHS training materials.
- Training Delivery Support: Assist EHS Director and safety positions with the delivery of annual and new employee training.
- Compliance Reporting Support: Assist all sites with EHS compliance reporting.
- Audit and Inspection: Participate in EHS auditing/inspections for compliance with risks.
- Executive Presentation Prep: Prepare presentations for delivery to executives and outside organizations.
- EHS Data Review: Review audits and EHS data to identify trends, risk issues, and repeat issues that should be escalated for improvement.
- Regulatory Reporting Compliance: Complete reporting documents required by the local, state, and federal government and associated agencies, and ensure timely payment of fees and other lawfully required monetary disbursements.
- Site Support Coordination: Support Prince Texas Energy locations, including the application and communication of training, risk assessments, and audits.
- EHS Standards Alignment: Ensure all sites' EHS standards, procedures, and practices are consistent with established company, environmental, and government regulations.
- Risk Assessment Planning: Assess, evaluate, quantify, and prioritize EHS risks for the organization and develop action plans for ensuring all significant risks are controlled and managed as part of the operational controls defined within the EHS management system, processes, and procedures
- Employee Safety Training: Provide EHS training to employees in support of achieving 100% engagement in risk assessments and a strong, positive safety culture
- Performance Metrics Tracking: Assist EHS Director in developing and monitoring organizational EHS metrics that drive improvement in EHS performance, e.g., near hit reporting, behavioral safety scorecards, ergonomic assessment, risk assessment data, environmental permit data, hazard reporting, etc.
5. Environmental Health and Safety Associate Accountabilities
- EHS Activity Management: Managing and overall responsible for EHS-related activities
- Document System Maintenance: Maintaining the EHS management system documents and ensuring enforcement
- Competency Training Oversight: Ensuring up-to-date competency training for all site staff in safe work practices and procedures
- Legal Compliance Assurance: Responsible for meeting all relevant legal and other requirements
- Contractor Qualification: Qualifying contractors and suppliers to ensure that they comply with the company’s site environmental, health, and safety standards and policies
- Risk Assessment Review: Conducting and reviewing risk assessment and aspects and impacts analysis, recommending safety measures, safe work procedures, and environmental matters
- Legal Implementation: Interpreting, disseminating, and implementing updated Workplace Safety and Health Act, environmental, and other legal requirements
- Ad-hoc EHS Tasks: Any other ad-hoc EHS duties as and when assigned by top management or the reporting supervisor
- Risk Control Support: Assist the team in the identification of workplace safety and health and environmental risks and the recommendation and implementation of the necessary control measures
6. HSE Coordinator Functions
- Safety Program Leadership: Provide leadership and support in the implementation of the Corporate Safety Program
- Site Safety Implementation: Assist management and project teams with the implementation of site-specific safety programs at the site level by working with site teams
- HSEQ Audit Support: Assist with internal/external HSEQ audits (e.g., COR, OHSAS, ISO)
- JHA and SWP Management: Develop and manage Job Hazard Analysis (JHA), Risk Assessments, and Safe Work Practices (SWP)
- Health and Safety Compliance: Ensure the Company’s Health and Safety complies with, or exceeds, applicable legislation
- Policy Implementation: Implement new and/or modified policies, procedures, and initiatives to enhance the program
- Workplace Inspection: Conduct routine site visits, inspect workplace facilities to ensure consistency with procedures and legislative requirements
- Issue Investigation: Investigate Health and Safety-related issues, liaise with governing bodies and other third-party inspectors, implement preventative measures, and follow up to ensure compliance
- Safety Training Delivery: Assist in the design and implementation of safety training programs and employee safety orientations, both on and off project sites
- Documentation Management: Maintain all required documentation and reports, manage Risk Assessments and processes
- Incident Mitigation: Address and mitigate Worker Near Miss, Incident, Accident, and Environmental incidents to analyze, identify, and communicate trends and frequency details
- JHSC Participation: Act as a member of, and a resource for, the company’s JHSC
7. Environmental Health and Safety (EHS) Coordinator Job Description
- Regulatory Plan Management: Maintain and update the requirements and recordkeeping of environmental regulatory required plans (i.e., SPCC, SWPPP, RCRA, Contingency Plan, Waste Minimization, etc.) and schedule, conduct, and track required training.
- Permit Application Support: Assist plants with permit applications for new sources or modifications, and manage/monitor current permit requirements.
- ISO 14001 Management: Lead and maintain the ISO 14001 management system, and participate in internal audits
- Regulatory Reporting: Coordinate, prepare, and submit regulatory reports (Form R, Tier II, Biennial Waste Reports, Air Emission Summary, NPDES, Storm water, Form U, DOT, etc.) by the required deadlines.
- Safety Initiative Leadership: Lead safety initiatives within the plant, and coordinate the Safety Committee activities
- Safety Culture Promotion: Create a safety vision for the plant and drive the culture in daily activities
- Incident Tracking: Track all safety incidents, safety observations, and suggestions to provide analysis on current and potential risks.
- Incident Investigation: Facilitate incident investigations to identify root causes and feasible corrective actions to prevent future incidents in the future.
- Workplace Safety Improvements: Recommend workplace changes to improve health and safety, using Job Safety Analysis, Ergonomic Studies, Safety Observations, and suggestion data.
- Workers' Compensation Collaboration: Collaborate with Human Resources on all Workers' Compensation initiatives to provide a proactive approach to preventing future claims.
- EHS Training Management: Conduct EHS training, track and maintain EHS training documentation such as training matrix, records, etc.
- EHS Project Implementation: Recommend and complete projects related to Continuous Improvements, Cost Savings Initiatives, and Process Improvements as related to EHS.
8. EHS Officer Overview
- Safety Oversight: Responsible for safety and discipline in the work area
- Induction and Equipment: Ensure that the induction training is conducted, and safety equipment is provided to new staff and visitors
- Equipment Distribution: Provide safety equipment to all persons who require the same on the terminal
- Refresher Training: Provide periodic refresher training on SOPs and safety standards to Safety Champions and Operations Supervisors
- Incident Response: Respond to the incident site immediately on receiving the intimation
- Incident Investigation: Carry out full investigations of all incidents and give hard copies to the documentation clerk to fill in the system
- Compliance Monitoring: Conduct random checks to monitor compliance with the safety policy
- Breach Investigation: In case any security personnel report a safety breach, start investigating
- Risk and SOP Development: Conduct Risk Assessments, define controls, and create standard operating procedures to decrease risk to employees
- SOP Compliance: Conduct rounds to check if standard operating procedures are followed
- Safety Reporting: Assists in the preparation of periodical reports regarding the Safety situation for the DP World Jeddah Management and the Regional Office
- Hazard Oversight: When working in the Hazard Area, physically oversee containers in a manner like to JIP rules
- Risk Standards Compliance: Implement and comply with DP World Fatal Risk and Safety Standards
9. EHS Specialist Details and Accountabilities
- Program Improvement Leadership: Leads programs to continuously improve safety and environmental programs on-site
- EHS Coaching: Coaches and develops others on the site's EHS programs and EHS matters.
- Agency Communication: Maintains contact with the various outside environmental and safety agencies.
- Regulation Monitoring: Monitors developments in EHS Regulations and interpretations of these by regulatory agencies.
- Regulation Advisory: Advise site management of changes in regulations or interpretations.
- Compliance Strategy Development: Develops and implements site strategies to ensure 100% compliance with all current and future EHS requirements.
- EHS System Improvement: Leads and implements improvements to EHS management systems and programs.
- Stakeholder Request Support: Assists in the timely response to external and internal stakeholder EHS requests and recommendations.
- Technical EHS Support: Provides technical support and advice to line management on new and existing processes and equipment in support of the EHS department's overall objectives.
- EHS Training Delivery: Develops and delivers EHS training to the site.
- Project EHS Input: Provides EHS input, guidance, and direction for the review of equipment modifications, new process introductions, and capital installations.
- SE Project Management: Leads SE-related projects and manages the execution of projects
- Risk and Incident Participation: Participates in risk assessments, inspections, audits, incident investigations, and implements and follows up on related CAPAs
- EHS Performance Reporting: Reports on EHS performance to management at regular intervals
10. Environmental Health and Safety (EHS) Specialist Tasks
- Training Delivery: Deliver training in classroom and hands-on settings
- Data Management: Gather and maintain records/data
- Issue Identification: Identify environmental, health, and safety issues
- Issue Resolution: Resolve minor safety issues and notify the supervisor of significant issues.
- Hazard Analysis Support: Assist with the development of job task hazard analysis, personal protective equipment analysis, trials, standard operating procedures, and formula safety checklists
- Safety Auditing: Conduct safety audits and periodic inspections
- Software Maintenance: Maintain safety and preventative maintenance software
- Result Communication: Communicate results and recommendations
- EHS Implementation Support: Act as a focal point for specific environmental, health, and safety implementation
- Incident Investigation: Participate in incident investigations and the corrective action process
- Regulatory Compliance: Work within state and federal safety regulations, corporate standards, policies, and procedures to ensure compliance
11. Senior EHS Specialist Roles
- Chemical Evaluation: Evaluate new chemicals and chemical use to ensure compliance with regulatory requirements, promote a safe work environment, and protect the environment.
- Hygiene Program Management: Manage/implement complex industrial hygiene programs for multiple facilities.
- Hazard Monitoring: Monitor industrial hygiene (chemical and physical hazards).
- Hygiene Survey Execution: Conduct routine and follow-up industrial hygiene surveys, prepare reports, recommend improvements, and communicate findings to site leadership.
- EHS Training: Provide training and information necessary to ensure that responsible personnel are aware of corporate and governmental EHS regulations and requirements.
- EHS Initiative Support: Assist department managers, supervisors, and employees with the implementation of creative approaches to improve safety, minimize environmental footprint and liability, and implement EHS initiatives.
- Regulatory Compliance Leadership: Direct and lead local regulatory compliance, including Title V, SPCC, EPCRA, RCRA, and storm water discharge.
- Permit Database Management: Create and manage a database for all regulatory permits and related documents.
- Waste Program Oversight: Oversee all aspects of the company’s recycling, solid, hazardous, bio-hazardous, and universal waste programs.
- Engineering Collaboration: Work with engineering in the design and installation of new or altered equipment or processes with the goal of eliminating or reducing health/safety hazards and environmental impact.
- Compliance Review Support: Assist in compliance reviews, risk assessments, audits, and inspections to support EHS and PGT objectives.
- Incident Investigation: Conduct and/or review incident investigations and the development of appropriate corrective and preventative actions (CAPA).
- EHS Inspection: Perform EHS inspections and assessments such as IH, PPE, LOTO, and machine guarding.
- Stakeholder Relations: Maintain positive and proactive relations with managers and employees, as well as customers and regulatory agencies.
12. Environmental Health and Safety Technician Details
- Safety Culture Promotion: Promote a culture of safety, quality, compliance, and continuous improvement throughout PENA
- Strategy Implementation Support: Partner with production supervisors and frontline employees to support implementing the set strategies to make PENA safer and more sustainable
- EHS Communication Plan: Help implement a compelling communication plan to promote EHS to employees
- Incident Response: Respond to incidents (injuries, near misses, property damages, etc), implement containment actions, and gather information for incident investigation purposes
- Incident Prevention: Spot, report, and prevent incidents on site, communicate clearly and interactively with employees, and coach them
- Incident Reporting: Write EHS incident reports, daily, monthly, and annually
- EHS Training: Provide training to employees, conduct EHS orientations, and onboarding
- Regulatory Awareness: Learn and maintain an awareness of regulatory standards and good industry practices
- Process Monitoring: Monitor processes for adherence to OSHA/EPA guidelines and the elimination of incidents
- Safety Auditing: Perform safety audits and work effectively with production employees/supervision
- Behavior Program Implementation: Implement various Behavior-Based Programs to promote proactive solutions
- 6S Adoption Support: Support areas across the plant in driving the adoption of 6S practices
13. EHS Technician Essential Functions
- Safety Orientation Training: Provides safety orientation and training for all employees
- EHSEP Development Support: Assist in the development of Project EHSEP
- Access Screening Management: Manages the project access screening programs (SA/background check)
- Emergency Procedure Training: Trains all site personnel on emergency, fire, and first-aid procedures
- First Aid Response: Renders first aid to any injured project personnel
- Incident Documentation: Documents all injuries, illnesses, near misses, property damage, or other safety or environmental events for the project
- EHS Reporting: Reports EHS information, injuries, statistics, equipment damage, etc., to Project and Regional/Corporate EHS management
- Record Maintenance: Maintains the incident and injury records and the investigation system
- OSHA Certification: Maintains current OSHA 30-hour standards and regulations certification
- Subcontractor Survey: Conducts surveys of subcontractor operations to ensure compliance with the project safety program, OSHA, state safety standards, and regulations
- Violation Reporting: Identifies violations and provides a report to the Project Manager for appropriate corrective action
- Safety Report Submission: Submits weekly safety reports to the EHS Director