WHAT DOES A MAINTENANCE TECHNICIAN DO?
Published: Jun 27, 2025 - The Maintenance Technician is responsible for installing, maintaining, and repairing machinery, equipment, and facilities following manufacturer guidelines and safety protocols. This role involves interpreting technical drawings, identifying parts needing replacement, and troubleshooting mechanical issues in coordination with production staff. Additionally, the technician completes tasks efficiently using shop mathematics and provides accurate daily reports of activities performed during their shift.
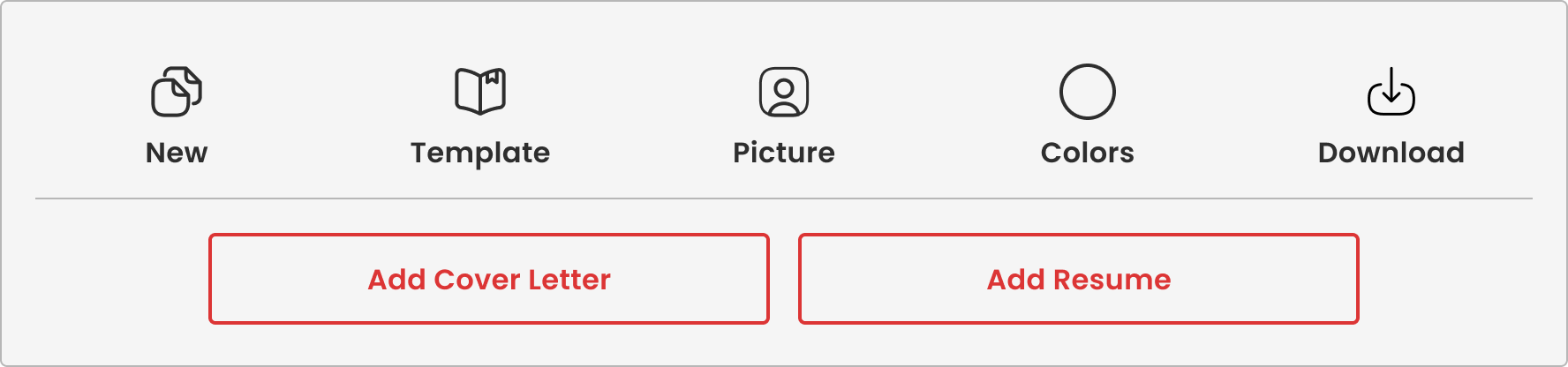

A Review of Professional Skills and Functions for Maintenance Technician
1. Maintenance Technician Accountabilities
- Troubleshooting: Troubleshoot and repair specific plant equipment.
- Diagnostics: Analyze test results, machine error messages, and information obtained from operators to diagnose and perform repairs.
- Preventative Maintenance: Perform preventative maintenance (PM), troubleshooting, inspection, calibration, installation, and all necessary support of equipment.
- Teamwork: Support and work as a team with the Electrical Maintenance Technicians.
- Inventory Management: Support parts inventory system accuracy.
- Machining: Create new parts with the use of available machining centers.
- General Duties: Perform miscellaneous plant duties as instructed by the supervisor.
- Safety Compliance: Follow and comply with all safety and work rules.
- Regulatory Compliance: Follow Environmental, Quality, and Safety Management System procedures and requirements.
2. Maintenance Technician Functions
- Equipment Observation: Learn the function of operating building equipment and systems as directed by the Chief and/or Assistant Chief Engineer by observing building engineers in their duties.
- Preventative Maintenance: Maintain a 90%+ on PM completion.
- System Optimization: Optimize the repair and operation of HVAC, electrical, and plumbing equipment and systems.
- Troubleshooting: Troubleshoot and repair equipment and system problems so that problems are resolved on the first attempt, cost-effectively.
- Tenant Service: Respond to tenant service requests in such a manner as to reduce tenant work orders and eliminate recurring problems.
- Work Order Management: Use Building Engines to complete tenant work requests, preventative maintenance assignments, and unscheduled maintenance tasks.
- Productivity Tools: Use various productivity-enhancing tools, such as a smartphone, in the completion of tenant work orders and preventative maintenance tasks.
- Energy Efficiency: Assist in fostering a work environment that promotes energy conservation and continuous improvement of engineering functions.
- Training Participation: Participate in Tabor Center engineering training programs and initiatives, such as TPC, or as suggested by the Chief Engineer.
- Leasing Support: Assist in leasing efforts.
- Safety Compliance: Comply with safety and environmental procedures, specifically hazardous communication programs and lockout–tagout programs.
3. Maintenance Technician Job Description
- Equipment Maintenance: Maintain, install, repair, and upkeep equipment, machinery, and facilities.
- Parts Identification: Identify parts or machines needing new or replacement parts.
- Mathematical Application: Utilize shop mathematics to complete assignments.
- Drawing Interpretation: Interpret drawings and schematics of equipment to properly adjust, maintain, or repair machinery.
- Troubleshooting: Respond to requests from production when mechanical issues have been identified and troubleshoot problems.
- Production Communication: Communicate with production to diagnose problems.
- Preventive Maintenance: Perform preventive maintenance according to the equipment manufacturer's recommendations.
- Task Efficiency: Complete assigned tasks with accuracy and efficiency regarding time and resources.
- Reporting: Provide daily reports of activities during the shift.
4. Maintenance Technician Overview
- Maintenance Execution: Carry out preventive and corrective maintenance on a wide range of mechanical and electrical machines.
- Vendor Sourcing: Source for contractors/vendors and services, and spares (mechanical and electrical).
- Vendor Engagement: Engage a relevant vendor for machine and facility repair.
- Scope Preparation: Prepare and provide the scope of work for machine and facility repair.
- Inspection Oversight: Oversee the maintenance and statutory licensing inspection of air pressure vessels, boilers, fire pumps, lifting equipment and gears, cooling towers, etc.
- Project Participation: Be part of the Improvement Projects assigned by the supervising manager.
5. Maintenance Technician Details and Accountabilities
- Maintenance Execution: Execute predictive and preventive maintenance according to plan.
- Corrective Maintenance: Execute corrective maintenance on time.
- Downtime Reduction: Reduce factory downtime caused by equipment malfunction due to maintenance issues, and identify equipment issues.
- Root Cause Analysis: Reduce recurrent equipment failures through true root cause analysis.
- Engineering Support: Support the engineering group with equipment validation and preventive maintenance development.
- Spare Parts Planning: Support for the development of the spare parts list to avoid long equipment downtime.
- Diagram Interpretation: Understand and read a flow chart diagram and PI&D.
- Statistical Analysis: Perform statistical analysis of the PMs done to verify the correct maintenance frequency.
6. Maintenance Technician Additional Details
- Repair Method Assessment: With support from Industrial Engineering, determine the best method of repair in terms of internal or outsourced repair.
- Equipment Installation: Support the installation of new production equipment.
- Equipment Servicing: Service and maintain facilities and production-related equipment.
- Electrical Knowledge: Understand industrial power or electrical qualifications.
- HVAC Inspection: Inspect and service industrial/residential HVAC systems.
- System Maintenance: Inspect, service, and maintain various support systems in buildings on plant premises.
- Machine Assessment: Inspect and assess the functionality of production machines.
- Mechanical Adjustment: Adjust mechanical parts using hand and machine tools.
- Part Fabrication: Fabricate parts for repairs and machine upgrades.
- Routine Maintenance: Conduct routine maintenance and safety checks.
- Production Communication: Communicate with the production team and maintain a clean work area.
7. Maintenance Technician Essential Functions
- Maintenance Procedures: Establish autonomous maintenance procedures and checklists for assigned equipment.
- Operator Training: Train operators to carry out autonomous maintenance and report potential problems.
- Equipment Safety: Ensure equipment is safe and always fit for operation.
- Preventative Maintenance Planning: Establish and carry out preventative maintenance plans.
- Spare Parts Planning: Identify and establish spare parts and maintenance material plans/inventory.
- Equipment Repair: Diagnose, repair, restore, and requalify any equipment failures.
- Problem Analysis: Engage in focused improvement through analysis of potential problems and failures.
- Equipment Monitoring: Monitor equipment health and productivity losses and lead improvement.
8. Maintenance Technician Role Purpose
- Troubleshooting: Troubleshoot equipment issues and make necessary repairs on time.
- Inventory Communication: Communicate with purchasing to maintain inventory levels of spare components.
- Maintenance Scheduling: Work with the production manager to schedule routine preventative maintenance.
- Work Area Organization: Maintain the overall orderliness of the maintenance area and the organization of replacement components.
- Machine Maintenance: Take responsibility for the maintenance, troubleshooting, and repair of production machines.
9. Maintenance Technician General Responsibilities
- Maintenance Management: Initiates, implements, and manages the maintenance program based on best practices with emphasis on preventive/predictive maintenance.
- Safety Program Coordination: Coordinates the development of company safety and health procedures and programs.
- Incident Investigation: Identifies, investigates, reports, and provides guidance relative to root causes for incidents, employee safety programs, and regulatory compliance relative to safety and health.
- Emergency Planning: Develops and implements solutions for emergency preparedness plans for the facility.
- Policy Consistency: Assists in ensuring consistency in safety policies and practices.
- Inventory Monitoring: Monitors the use and inventories of spare parts, maintenance supplies, and equipment, and initiates reordering.
- Equipment Repair: Maintains and repairs maintenance shop equipment.
- Downtime Reduction: Reviews the operations of plant equipment and systems constantly to minimize unplanned downtime, anticipate problems on time, and identify opportunities for improvement.
- Compliance Implementation: Customizes and implements safety and environmental compliance programs, including Hazard Communication, Lock Out Tag Out, Emergency Action Plans, Fire Prevention, Hot Work, Waste Management, and Permit Compliance.
- Training Facilitation: Conducts required safety and environmental training and tracks attendance.
- KPI Reporting: Maintains key performance indicator reporting for the facility, which includes injuries, incidents, energy usage, waste generated/recycled, and air emission calculations.
- SDS Management: Maintains facility safety data sheets, including review and approval process.
- Corrective Action Coordination: Coordinates the completion of safety and environmental corrective actions resulting from audits and inspections by customers, insurance providers, and regulatory agencies.
- Incident Leadership: Leads the incident investigation process and ensures corrective actions are completed.
- Safety Metrics Management: Maintains Westrock online safety metrics and audits.
- Site Management Support: Provide backup site management duties in the absence of the site manager.
Relevant Information