FACILITIES MAINTENANCE MECHANIC RESUME EXAMPLE
Published: Feb 28, 2025 - The Facilities Maintenance Mechanic ensures compliance with all health and safety standards, prioritizing safety in every action. Manages daily maintenance operations for refinery equipment, including pumps, compressors, and vehicles, ensuring efficient functioning and safety. Provides leadership to other technicians, directs daily tasks, and handles complex troubleshooting and installations, fostering a collaborative work environment.
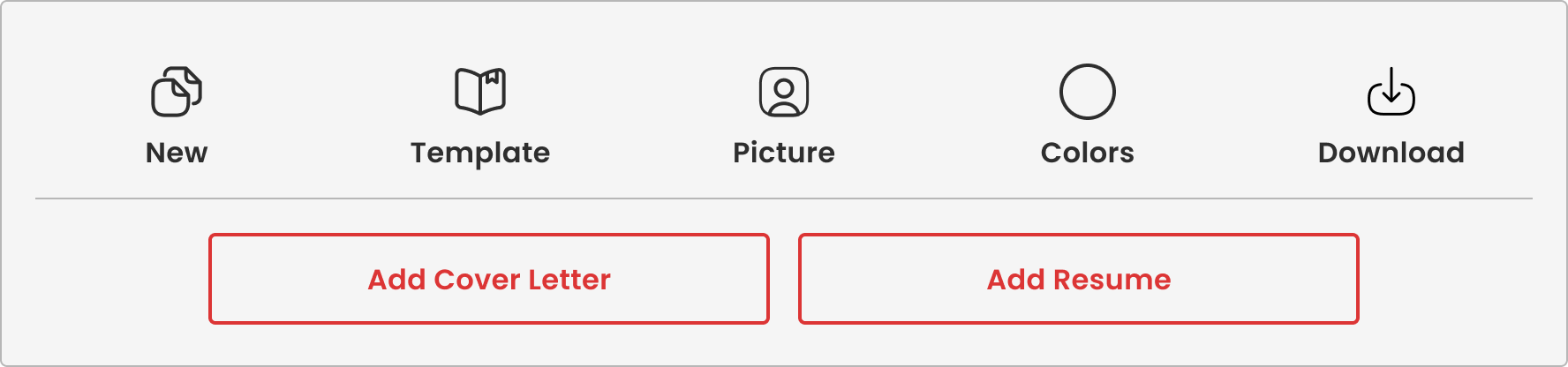
Tips for Facilities Maintenance Mechanic Skills and Responsibilities on a Resume
1. Facilities Maintenance Mechanic, Coastal Industrial Solutions, Miami, FL
Job Summary:
- Maintains critical/non-critical equipment at a high level of reliability.
- Documents daily activities as required by SOP, departmental policies, and/or other work instructions.
- Evaluate and repair a wide variety of machinery and equipment using acquired knowledge, skills and experience, the company-supplied tools, some fabrication of parts, and new and/or used but serviceable repair parts.
- Perform repairs to parts or equipment that may require cutting, brazing, TIG/MIG, or stick welding.
- Performs advanced troubleshooting of facility equipment and machinery if required with the guidance of the Facilities Maintenance Manager.
- Identifies parts to be repaired, inventories critical spare parts, and recommends ordering of non-stock items.
- Performs preventative maintenance requirements (PMRs) and unscheduled maintenance services when scheduled.
- Performs high-quality maintenance services completing jobs thoroughly.
- Manage building repair and maintenance projects including sourcing suppliers for budgets and capital improvement projects, and monitoring adherence to budgets and schedules.
- Availability to be on call to respond to building emergencies, 24/7.
- Maintaining compliance documentation required for reporting to federal, state, and local municipalities.
Skills on Resume:
- Equipment Reliability (Hard Skills)
- Documentation (Hard Skills)
- Machinery Repair (Hard Skills)
- Welding (Hard Skills)
- Troubleshooting (Hard Skills)
- Inventory Management (Hard Skills)
- Preventative Maintenance (Hard Skills)
- Project Management (Soft Skills)
2. Facilities Maintenance Mechanic, Western Technical Services, Denver, CO
Job Summary:
- Ensures Health and Safety is the number one priority by complying with all safe work practices, policies, and processes and acting in a safe manner at all times
- Responsible for daily directing and performing preventative and routine maintenance on a variety of refinery equipment including, but not limited to: pumps, compressors, vehicles, basic instrumentation, heat exchangers, pressure vessels, and other equipment.
- Advises plant personnel on maintenance equipment-related concerns.
- Ensures that all safety practices are followed during maintenance activities.
- Communicate immediately to the Maintenance Supervisor any safety issues that cannot be immediately resolved at his level.
- Is responsible for the daily scheduling and prioritization of Maintenance activities.
- Provides leadership and direction, when required, to the other Maintenance Technicians while promoting a team-oriented work environment
- Performs installation of simple office furniture apparatus, and room setups for conferences, meetings, and events
- Conduct scheduled inspections for service and preventive maintenance on non-complex safety and operational equipment and fixtures.
- Performs routine troubleshooting and repairs to non-complex accessories and fixtures throughout the facility
- Transportation of confidential documents for Shredding
- Snow/Ice removal and inclement weather clean-up
- Assigned tasks and duties are performed in compliance with OSHA safety regulations
Skills on Resume:
- Safety Compliance (Hard Skills)
- Maintenance (Hard Skills)
- Advisory (Soft Skills)
- Communication (Soft Skills)
- Scheduling (Soft Skills)
- Leadership (Soft Skills)
- Installation (Hard Skills)
- Troubleshooting (Hard Skills)
3. Facilities Maintenance Mechanic, Riverfront Manufacturing, Portland, OR
Job Summary:
- Repairs, maintains, patches and paints and installs electrical, HVAC, mechanical, refrigeration, and electronic theater systems and equipment in accordance with applicable building codes and safety regulations
- Assists with facilities projects as necessary (e.g. location of facility systems, zones, water & power distribution, and pick up, store or distribute stock)
- Utilizes and maintains electric hand tools and voltage devices to perform duties
- Maintains and repairs a variety of equipment and systems such as furniture lifts, plumbing, electronic theater systems, energy management, electrical, mechanical, HVAC, carpentry, as well as daily operations
- Troubleshoots and performs routine inspections, repairs, and maintenance of facility systems and equipment (e.g. water, power distribution, exhaust, fire alarms, emergency procedures, gas and electrical distribution, fans, motors, blowers, pumps and sprinklers)
- Performs a daily walk-through of the facility with designated lists
- Operates and repairs equipment such as forklifts, maintenance vehicles, and tow motors
- Prepares progress reports, and informs Facility Manager of project/task status and deviation from goals/tasks
Skills on Resume:
- Electrical Installation (Hard Skills)
- HVAC Maintenance (Hard Skills)
- Equipment Repair (Hard Skills)
- Tool Utilization (Hard Skills)
- System Troubleshooting (Hard Skills)
- Safety Compliance (Hard Skills)
- Project Assistance (Soft Skills)
- Reporting (Soft Skills)
4. Facilities Maintenance Mechanic, Summit Facility Operations, Charlotte, NC
Job Summary:
- Operation of computer controls for the primary pumps and sand filters for the seawater pump life support systems
- Monitor the aquarium, sea lion tanks, cistern and respond to alarms, adjust and balance flows, operate pumps and valves
- Coordinate the disassembly and cleaning of the pump house, piping and sand filters
- Troubleshoot, repair, rebuild and install actuator valves, pumps, motors and couplings
- Coordinate and document the changeover of seawater intake and discharge lines
- Perform weekly cleaning of the pump screen
- Operate and maintain boilers, air handlers, exhaust fans, lighting systems, DI/RO water system, electrical and plumbing
- Build cabinets, shelves, and desktops, and add walls and doors for office space
- Provide support and guidance to researchers and students for the safe and proper use of shop equipment, tools and materials
Skills on Resume:
- Equipment Operation (Hard Skills)
- Maintenance (Hard Skills)
- Documentation (Hard Skills)
- Carpentry (Hard Skills)
- System Monitoring (Hard Skills)
- Coordination (Soft Skills)
- Problem-Solving (Soft Skills)
- Leadership (Soft Skills)
Relevant Information